Modelling reasonable operation regimes of the main propulsion plant main diesel engine - Propeller - hull on the general cargo ship
The article presents the modeling results of the characteristics of main propulsion plant Diesel
Engine – Propeller – Hull, based on the combination of the analytical method and regressive analysis of
the empirical data. The authors create the algorithms on the base of the created models to select the
reasonable operating regime of the main propulsion plant (MPP) according to the different operating
conditions (in still water, in sea wave, in the canal, etc.). This paper provides the numerical simulation
results of the drawn combination characteristics of MPP on the 34000 DWT general cargo ship built in
Vietnam with the main engine MAN 6S 46 MCC, and of the selected regime respectively the desired
operated conditions. The research results would be used for the simulation of monitoring and controlling
the MPP on the general cargo ship, in order to improve the education quality of the electrical and marine
engineering field at Vietnam Maritime University.
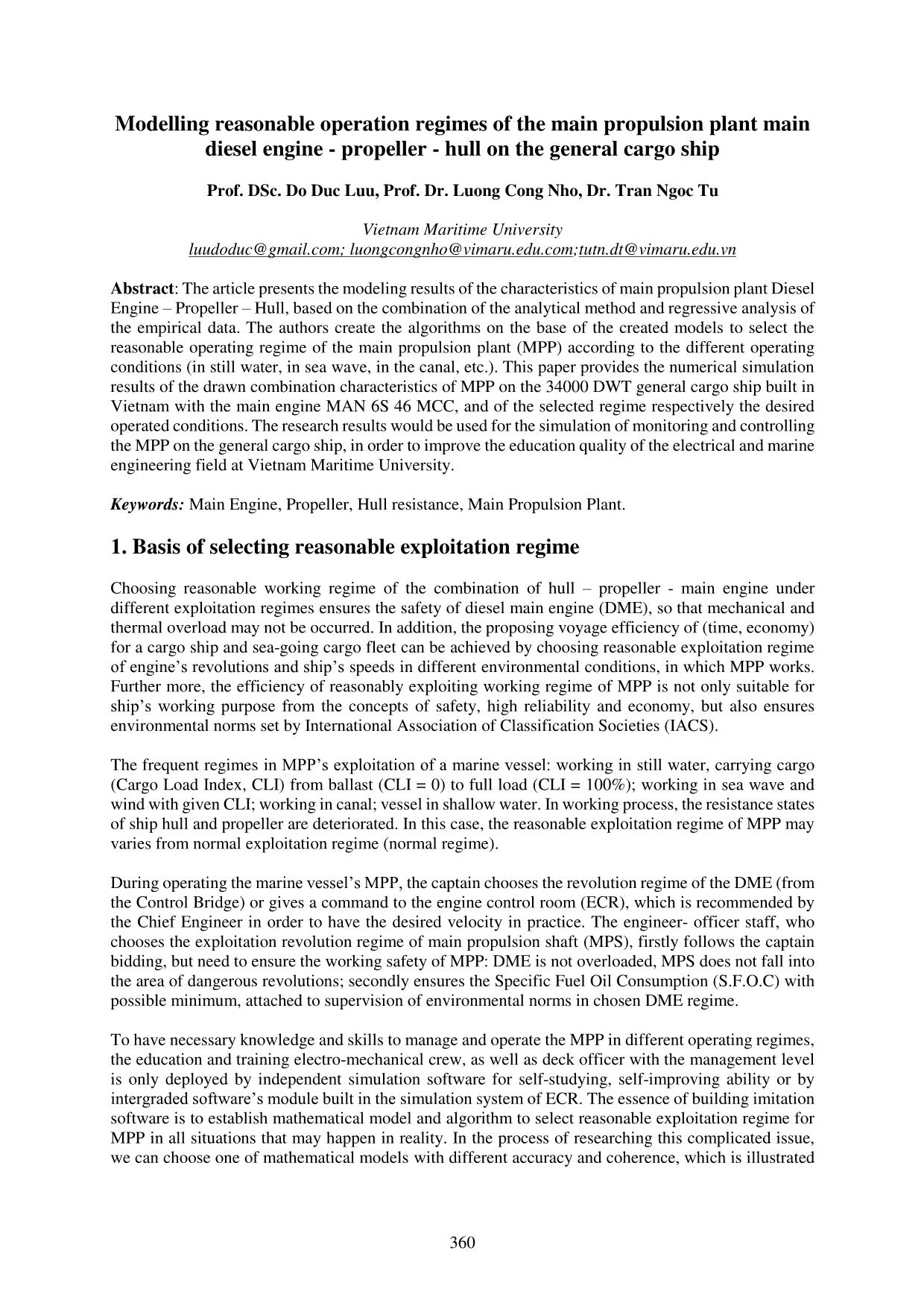
Trang 1

Trang 2
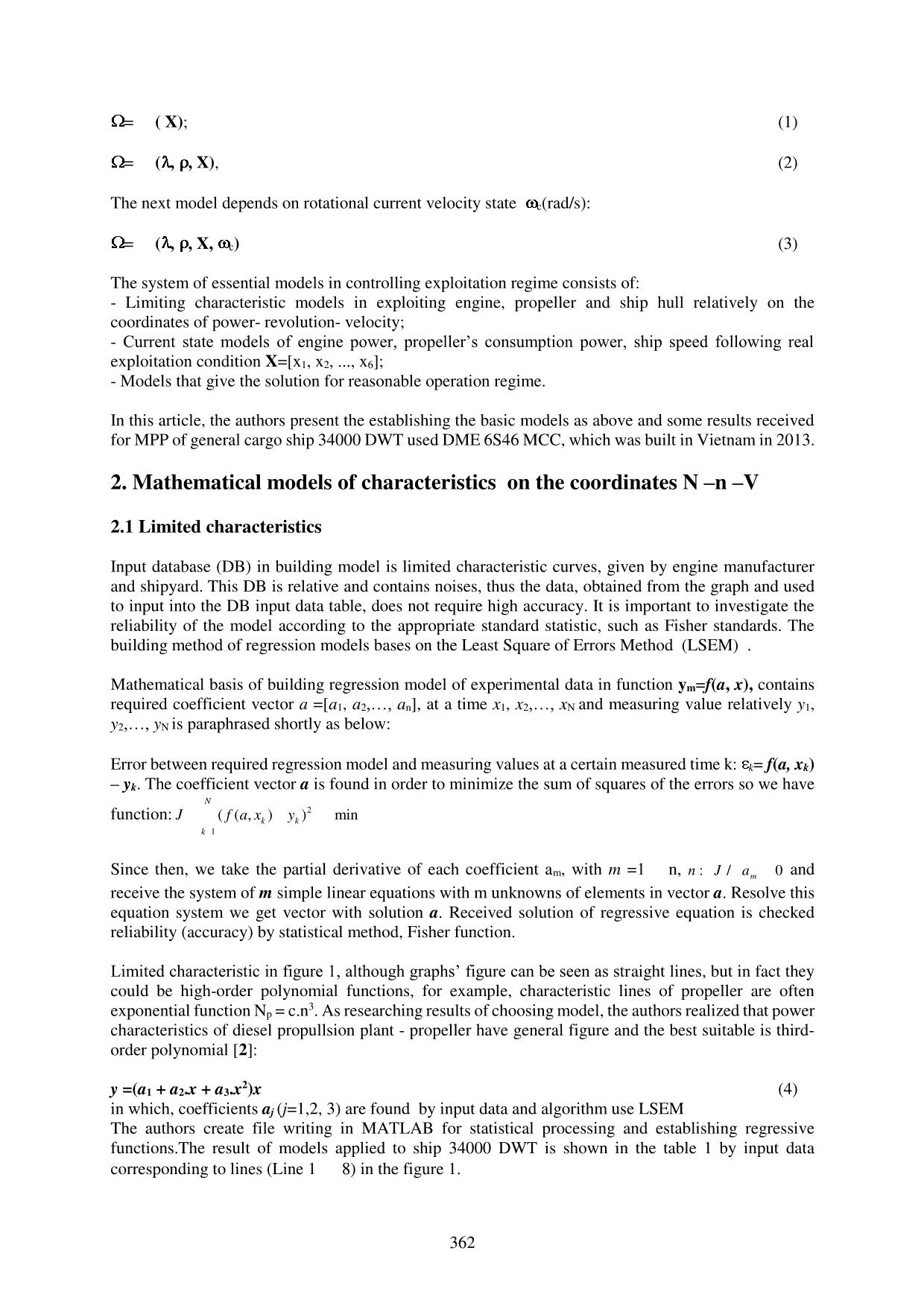
Trang 3
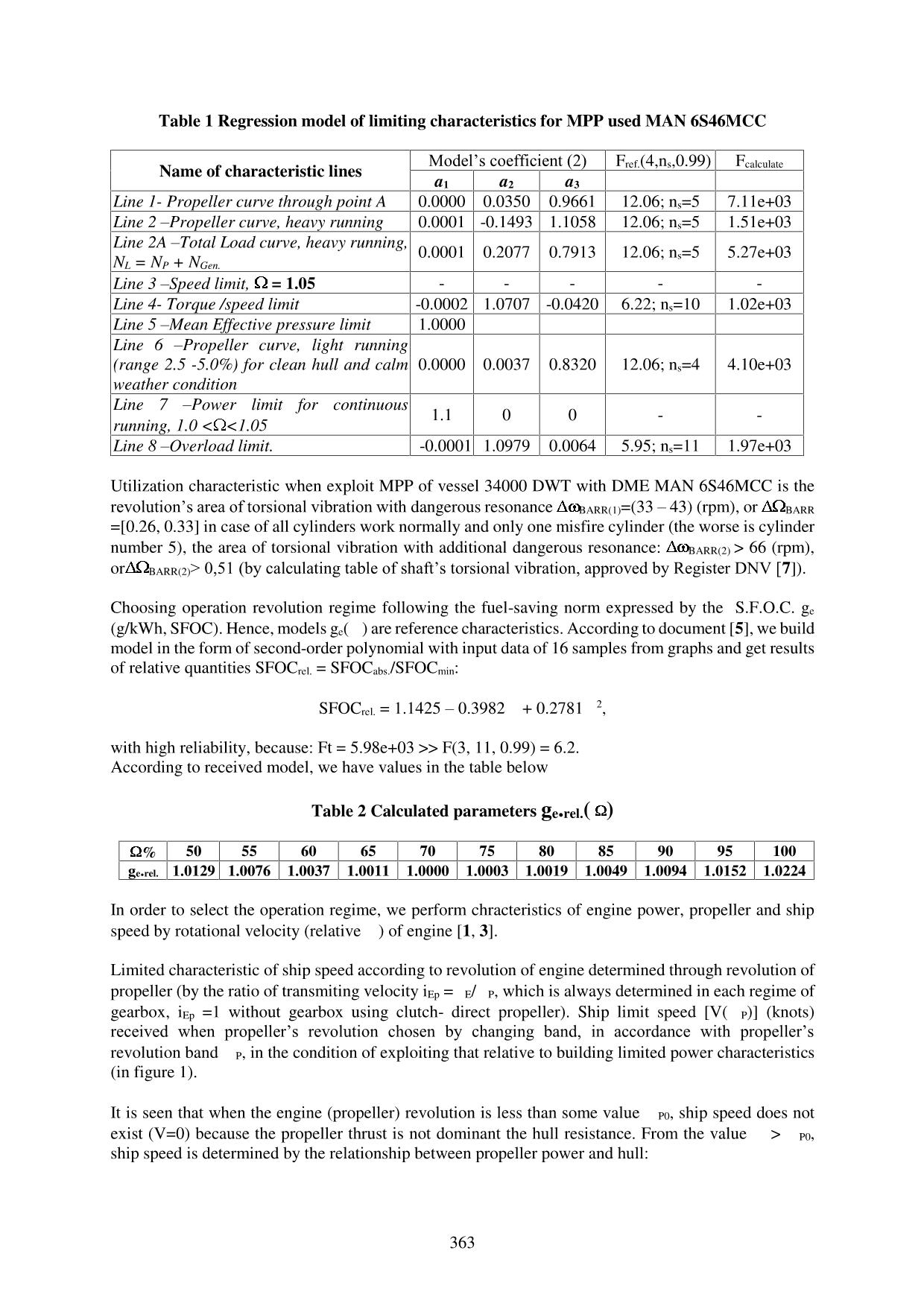
Trang 4
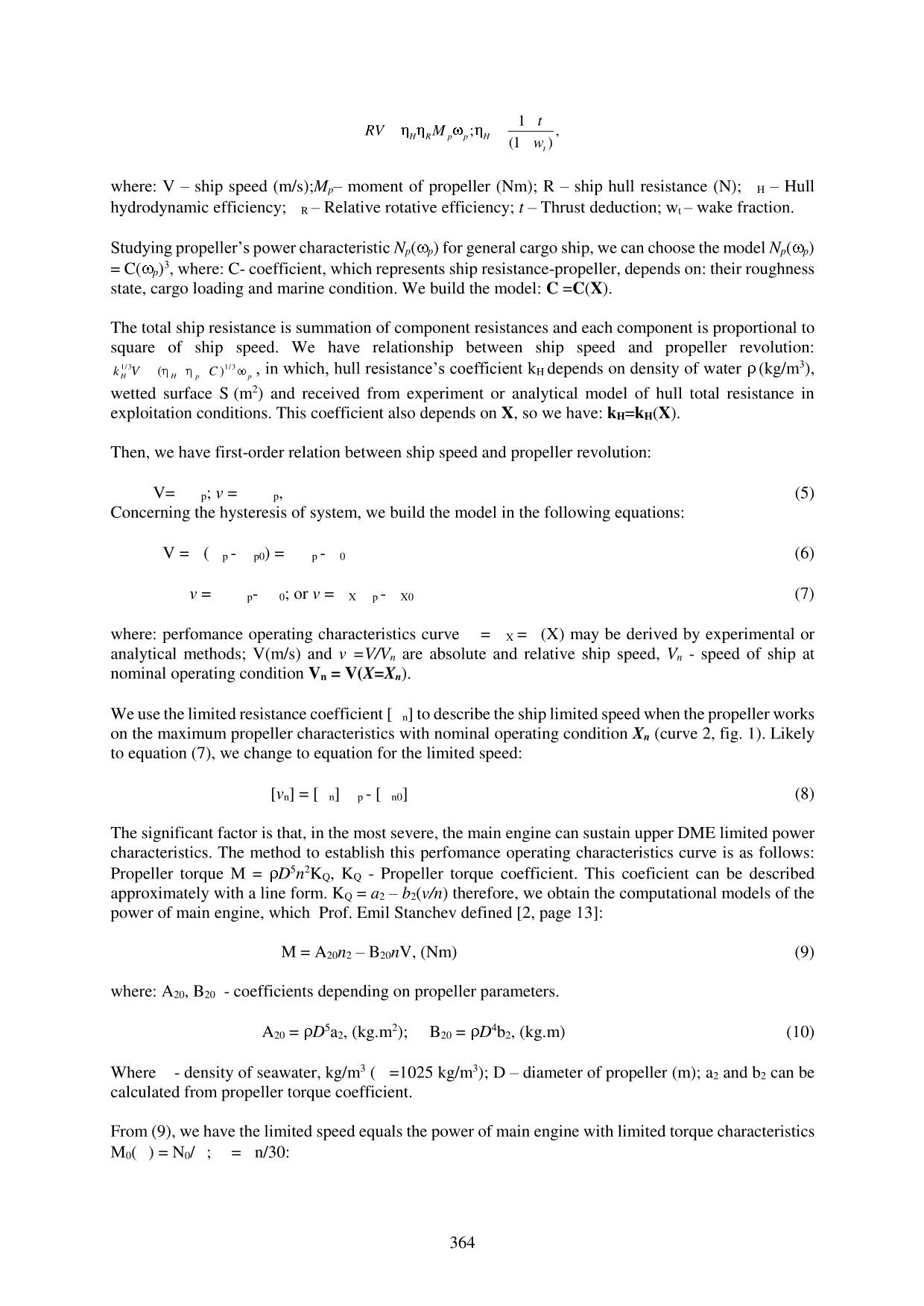
Trang 5
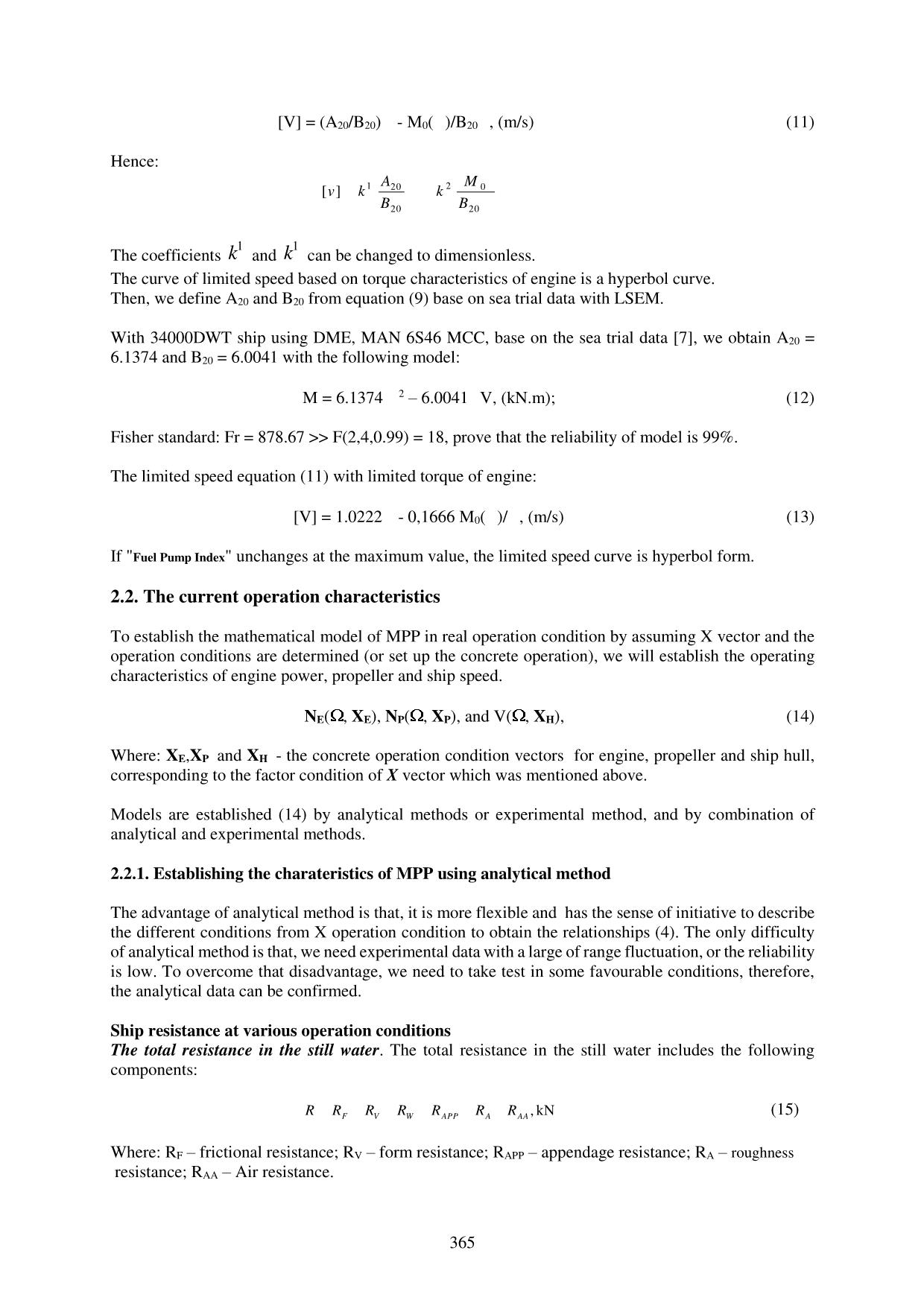
Trang 6
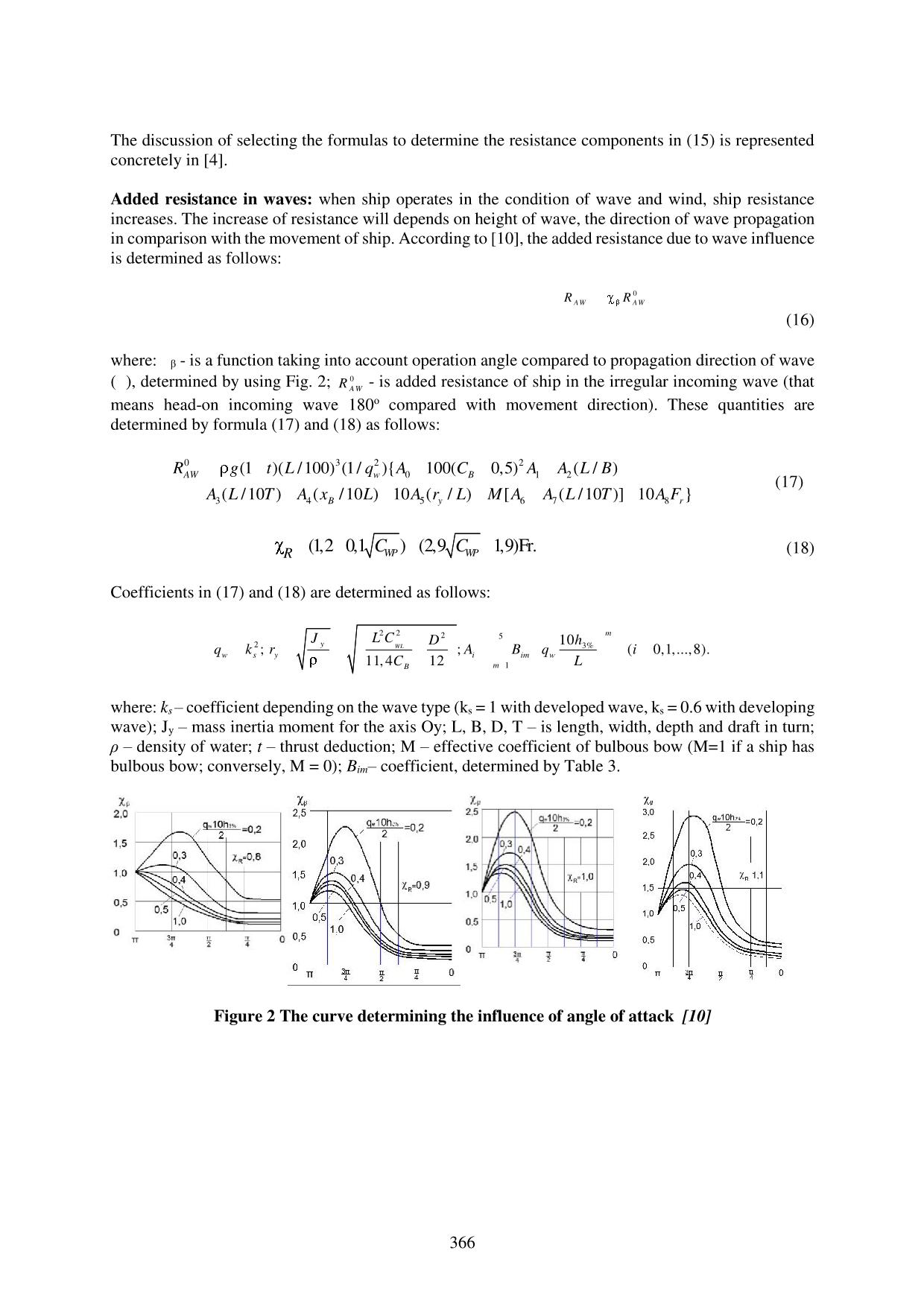
Trang 7
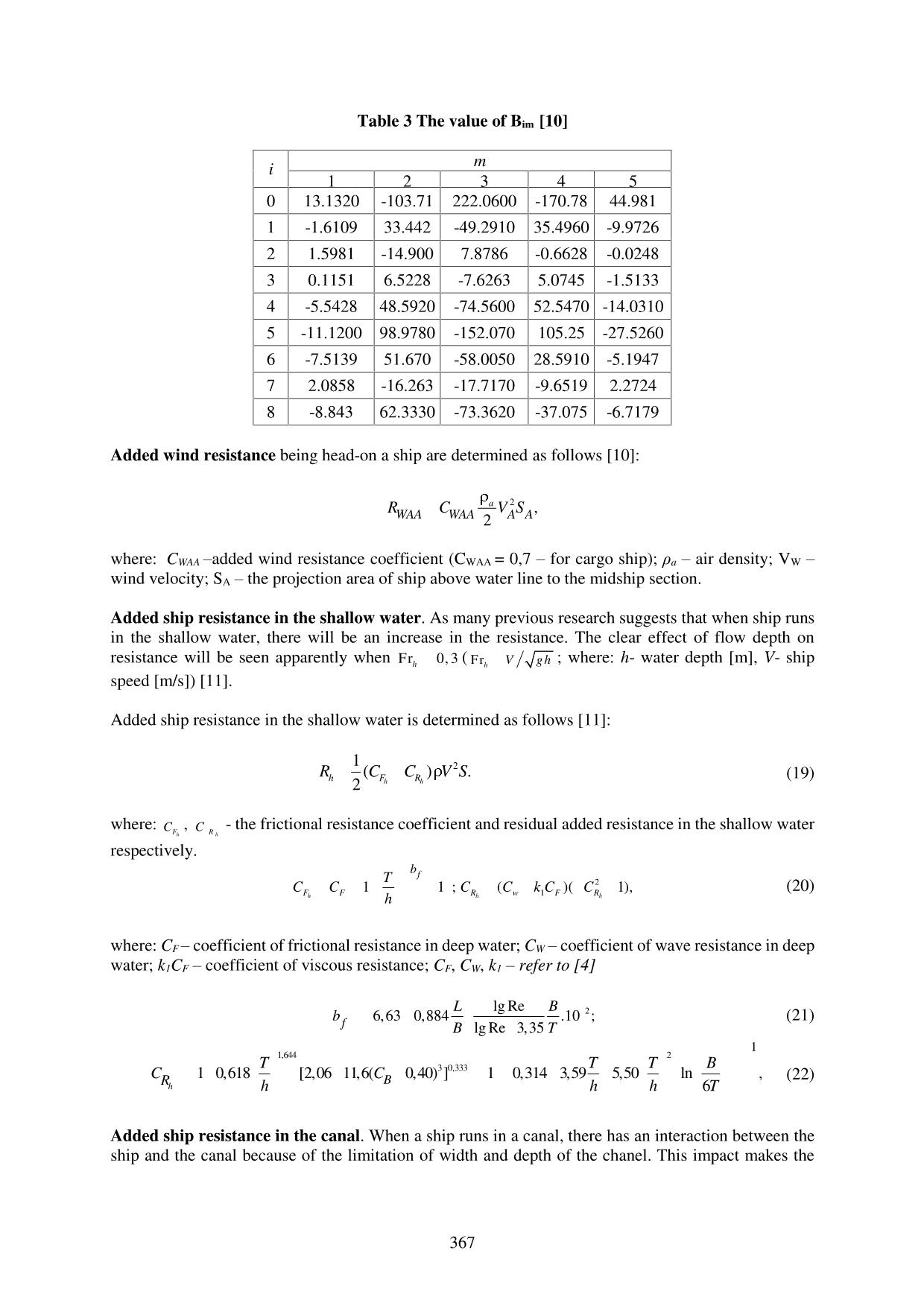
Trang 8
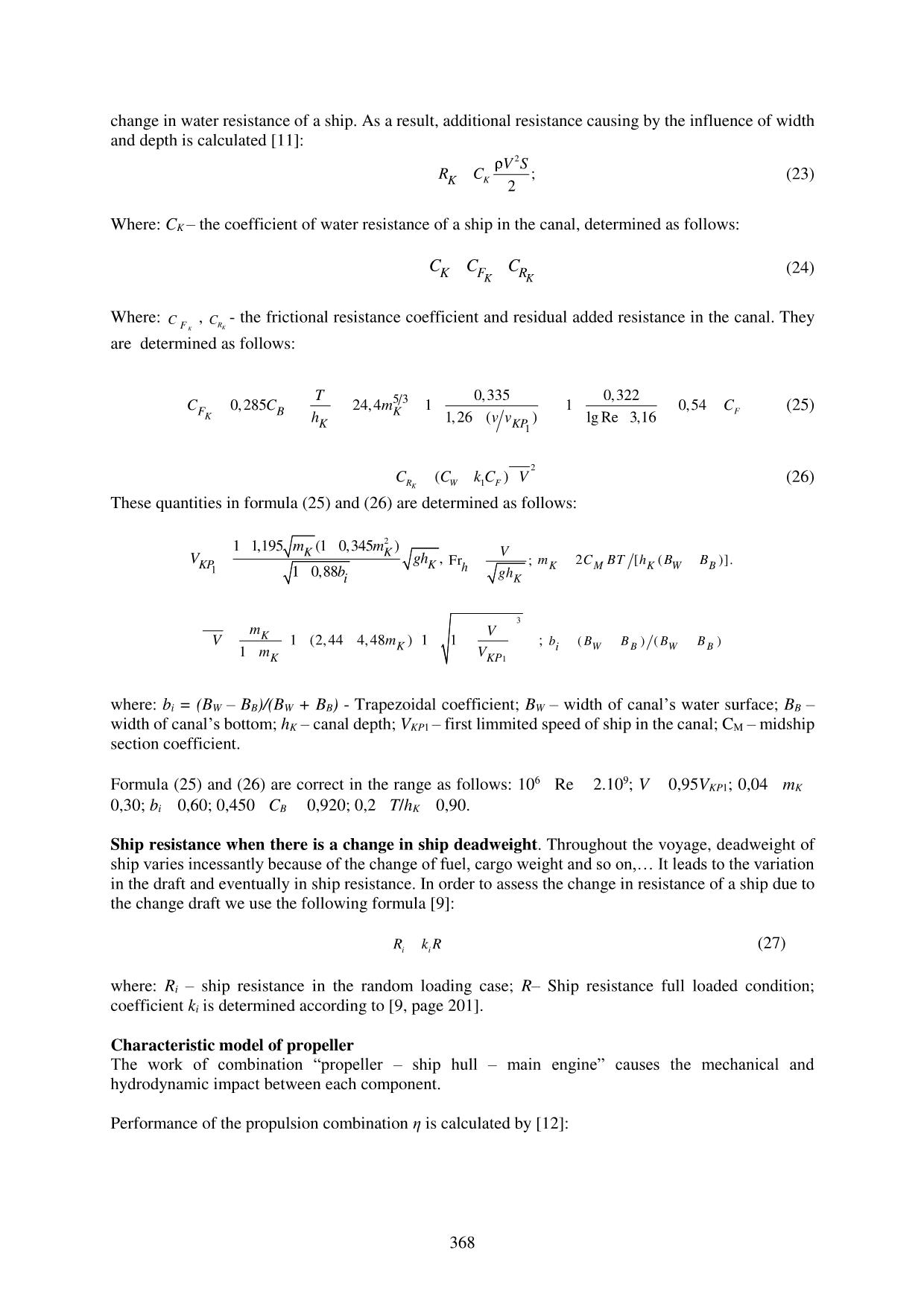
Trang 9
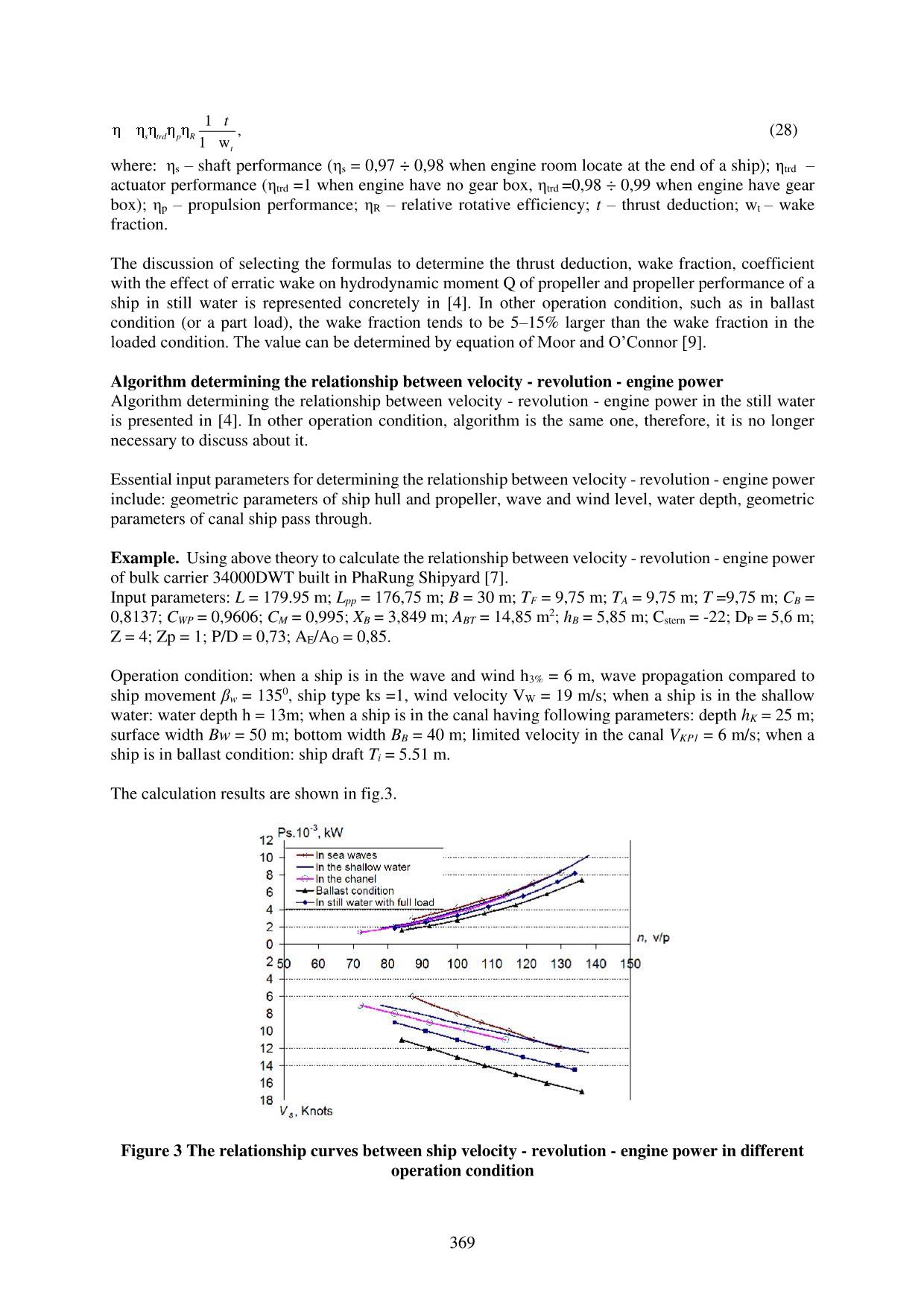
Trang 10
Tải về để xem bản đầy đủ
Tóm tắt nội dung tài liệu: Modelling reasonable operation regimes of the main propulsion plant main diesel engine - Propeller - hull on the general cargo ship
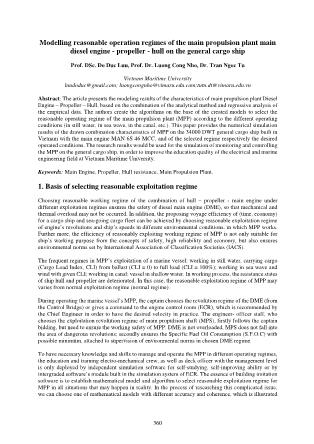
360 Modelling reasonable operation regimes of the main propulsion plant main diesel engine - propeller - hull on the general cargo ship Prof. DSc. Do Duc Luu, Prof. Dr. Luong Cong Nho, Dr. Tran Ngoc Tu Vietnam Maritime University luudoduc@gmail.com; luongcongnho@vimaru.edu.com;tutn.dt@vimaru.edu.vn Abstract: The article presents the modeling results of the characteristics of main propulsion plant Diesel Engine – Propeller – Hull, based on the combination of the analytical method and regressive analysis of the empirical data. The authors create the algorithms on the base of the created models to select the reasonable operating regime of the main propulsion plant (MPP) according to the different operating conditions (in still water, in sea wave, in the canal, etc.). This paper provides the numerical simulation results of the drawn combination characteristics of MPP on the 34000 DWT general cargo ship built in Vietnam with the main engine MAN 6S 46 MCC, and of the selected regime respectively the desired operated conditions. The research results would be used for the simulation of monitoring and controlling the MPP on the general cargo ship, in order to improve the education quality of the electrical and marine engineering field at Vietnam Maritime University. Keywords: Main Engine, Propeller, Hull resistance, Main Propulsion Plant. 1. Basis of selecting reasonable exploitation regime Choosing reasonable working regime of the combination of hull – propeller - main engine under different exploitation regimes ensures the safety of diesel main engine (DME), so that mechanical and thermal overload may not be occurred. In addition, the proposing voyage efficiency of (time, economy) for a cargo ship and sea-going cargo fleet can be achieved by choosing reasonable exploitation regime of engine’s revolutions and ship’s speeds in different environmental conditions, in which MPP works. Further more, the efficiency of reasonably exploiting working regime of MPP is not only suitable for ship’s working purpose from the concepts of safety, high reliability and economy, but also ensures environmental norms set by International Association of Classification Societies (IACS). The frequent regimes in MPP’s exploitation of a marine vessel: working in still water, carrying cargo (Cargo Load Index, CLI) from ballast (CLI = 0) to full load (CLI = 100%); working in sea wave and wind with given CLI; working in canal; vessel in shallow water. In working process, the resistance states of ship hull and propeller are deteriorated. In this case, the reasonable exploitation regime of MPP may varies from normal exploitation regime (normal regime). During operating the marine vessel’s MPP, the captain chooses the revolution regime of the DME (from the Control Bridge) or gives a command to the engine control room (ECR), which is recommended by the Chief Engineer in order to have the desired velocity in practice. The engineer- officer staff, who chooses the exploitation revolution regime of main propulsion shaft (MPS), firstly follows the captain bidding, but need to ensure the working safety of MPP: DME is not overloaded, MPS does not fall into the area of dangerous revolutions; secondly ensures the Specific Fuel Oil Consumption (S.F.O.C) with possible minimum, attached to supervision of environmental norms in chosen DME regime. To have necessary knowledge and skills to manage and operate the MPP in different operating regimes, the education and training electro-mechanical crew, as well as deck officer with the management level is only deployed by independent simulation software for self-studying, self-improving ability or by intergraded software’s module built in the simulation system of ECR. The essence of building imitation software is to establish mathematical model and algorithm to select reasonable exploitation regime for MPP in all situations that may happen in reality. In the process of researching this complicated issue, we can choose one of mathematical models with different accuracy and coherence, which is illustrated 361 by general cargo ship 34000 DWT, used DME of brand MAN 6S 46MCC built in 2013 (in Pha Rung Shipyard, Hai Phong city, Vietnam). Choosing reasonable exploitation regime for MPP of marine vessel, which is set up for educating and training engineering cadets, and officer training courses, is a fundamental problem. In different levels of training programme, the principle of diesel operation follows the guide of diesel operation provided by the engine manufacturer [1, 2, 3] to ensure the DME the thermo-mechanical safety, the working regime with the minimum S.F.O.C (ge =min). In technical file provided by the ship builder or diessel manufacturer as well as the data of sea trial test and the certification of the diesel, there are characteristic curves that allows to exploit engine, by which we may assess the area of the MPP exploitation. For example, for the ship 34000 DWT mentioned above, following the engine document of MAN 6S 45MCC, engine factory [6] provides the table of test data in 4 loading regimes with power 25-50-75- 100% of the normal power and the measured parameters: engine revolution (nE, rpm); fuel pump index (FPI, hp), maximum combustion pressure (Pz, Bar), maximum compression pressure (Pc, Bar), mean effective pressure (MEP, Pme, Bar), the Specific Fuel Oil Consumption (S.F.O.C, ge, g/kWh), air intake pressure (Pscav, Bar), speed of turbo-changer (nT, rpm). In the ship sea trial test document [7], the data table of measured test regimes and parameters: mean revolution of propeller (np, rpm), ship speed (V, mile/h, or Vp, m/s), torque (M, kNm), relatively the 4 test regimes of consumption power (Np%) is given. In addition, the operation guidance of DME – engine MAN 6S 46 MCC [5] shows the characteristics of DME working limit and characteristics of propeller limited by operating revolution as figure 1. The limited power ch ... onents: , kNF V W APP A AAR R R R R R R (15) Where: RF – frictional resistance; RV – form resistance; RAPP – appendage resistance; RA – roughness resistance; RAA – Air resistance. 366 The discussion of selecting the formulas to determine the resistance components in (15) is represented concretely in [4]. Added resistance in waves: when ship operates in the condition of wave and wind, ship resistance increases. The increase of resistance will depends on height of wave, the direction of wave propagation in comparison with the movement of ship. According to [10], the added resistance due to wave influence is determined as follows: 0 AW AWR R (16) where: β - is a function taking into account operation angle compared to propagation direction of wave (), determined by using Fig. 2; 0AWR - is added resistance of ship in the irregular incoming wave (that means head-on incoming wave 180o compared with movement direction). These quantities are determined by formula (17) and (18) as follows: 0 3 2 2 0 1 2 3 4 5 6 7 8 (1 )( /100) (1/ ){ 100( 0,5) ( / ) ( /10 ) ( /10 ) 10 ( / ) [ ( /10 )] 10 } AW w B B y r R g t L q A C A A L B A L T A x L A r L M A A L T A F (17) (1,2 0,1 ) (2,9 1,9)Fr.WP WPR C C (18) Coefficients in (17) and (18) are determined as follows: 2 2 2 5 2 3% 1 10 ; ; ( 0,1,...,8). 11, 4 12 WL m y w s y i im w mB L CJ hDq k r A B q i C L where: ks – coefficient depending on the wave type (ks = 1 with developed wave, ks = 0.6 with developing wave); Jy – mass inertia moment for the axis Oy; L, B, D, T – is length, width, depth and draft in turn; ρ – density of water; t – thrust deduction; M – effective coefficient of bulbous bow (M=1 if a ship has bulbous bow; conversely, M = 0); Bim– coefficient, determined by Table 3. Figure 2 The curve determining the influence of angle of attack [10] 367 Table 3 The value of Bim [10] i m 1 2 3 4 5 0 13.1320 -103.71 222.0600 -170.78 44.981 1 -1.6109 33.442 -49.2910 35.4960 -9.9726 2 1.5981 -14.900 7.8786 -0.6628 -0.0248 3 0.1151 6.5228 -7.6263 5.0745 -1.5133 4 -5.5428 48.5920 -74.5600 52.5470 -14.0310 5 -11.1200 98.9780 -152.070 105.25 -27.5260 6 -7.5139 51.670 -58.0050 28.5910 -5.1947 7 2.0858 -16.263 -17.7170 -9.6519 2.2724 8 -8.843 62.3330 -73.3620 -37.075 -6.7179 Added wind resistance being head-on a ship are determined as follows [10]: 2 , 2 a WAA WAA A AR C V S where: CWAA –added wind resistance coefficient (CWAA = 0,7 – for cargo ship); ρa – air density; VW – wind velocity; SA – the projection area of ship above water line to the midship section. Added ship resistance in the shallow water. As many previous research suggests that when ship runs in the shallow water, there will be an increase in the resistance. The clear effect of flow depth on resistance will be seen apparently when Fr 0, 3h ( Frh V gh ; where: h- water depth [m], V- ship speed [m/s]) [11]. Added ship resistance in the shallow water is determined as follows [11]: 21 ( ) . 2 h hh F R R C C V S (19) where: hF C , hR C - the frictional resistance coefficient and residual added resistance in the shallow water respectively. 2 11 1 ; ( )( 1),h h hF F R w F R fbTC C C C k C C h (20) where: CF – coefficient of frictional resistance in deep water; CW – coefficient of wave resistance in deep water; k1CF – coefficient of viscous resistance; CF, CW, k1 – refer to [4] 2lg Re6,63 0,884 .10 ; lg Re 3,35f L Bb B T (21) 1,644 2 3 0,333 1 1 0,618 [2,06 11,6( 0,40) ] 1 0,314 3,59 5,50 ln , 6h BR T T T BC C h h h T (22) Added ship resistance in the canal. When a ship runs in a canal, there has an interaction between the ship and the canal because of the limitation of width and depth of the chanel. This impact makes the 368 change in water resistance of a ship. As a result, additional resistance causing by the influence of width and depth is calculated [11]: 2 ; 2KK V SR C (23) Where: CK – the coefficient of water resistance of a ship in the canal, determined as follows: K KK F R C C C (24) Where: KFC , KRC - the frictional resistance coefficient and residual added resistance in the canal. They are determined as follows: 1 5 3 0,335 0,3220,285 24,4 1 1 0,54 1,26 ( ) lg Re 3,16 FKF B KK KP TC C m C h v v (25) 2 1( )KR W FC C k C V (26) These quantities in formula (25) and (26) are determined as follows: 2 1 1 1,195 (1 0,345 ) , 1 0,88 K K KP K i m m V gh b Fr ; K h V gh 2 [ ( )].K M K W Bm C BT h B B 3 1 1 (2,44 4,48 ) 1 1 ; 1 K K K KP m VV m m V ( ) ( )W B W Bib B B B B where: bi = (BW – BB)/(BW + BB) - Trapezoidal coefficient; BW – width of canal’s water surface; BB – width of canal’s bottom; hK – canal depth; VKP1 – first limmited speed of ship in the canal; CM – midship section coefficient. Formula (25) and (26) are correct in the range as follows: 106 Re 2.109; V 0,95VKP1; 0,04 mK 0,30; bi 0,60; 0,450 CB 0,920; 0,2 T/hK 0,90. Ship resistance when there is a change in ship deadweight. Throughout the voyage, deadweight of ship varies incessantly because of the change of fuel, cargo weight and so on, It leads to the variation in the draft and eventually in ship resistance. In order to assess the change in resistance of a ship due to the change draft we use the following formula [9]: i iR k R (27) where: Ri – ship resistance in the random loading case; R– Ship resistance full loaded condition; coefficient ki is determined according to [9, page 201]. Characteristic model of propeller The work of combination “propeller – ship hull – main engine” causes the mechanical and hydrodynamic impact between each component. Performance of the propulsion combination η is calculated by [12]: 369 1 , 1 ws trd p R t t (28) where: ηs – shaft performance (ηs = 0,97 ÷ 0,98 when engine room locate at the end of a ship); ηtrd – actuator performance (ηtrd =1 when engine have no gear box, ηtrd =0,98 ÷ 0,99 when engine have gear box); ηp – propulsion performance; ηR – relative rotative efficiency; t – thrust deduction; wt – wake fraction. The discussion of selecting the formulas to determine the thrust deduction, wake fraction, coefficient with the effect of erratic wake on hydrodynamic moment Q of propeller and propeller performance of a ship in still water is represented concretely in [4]. In other operation condition, such as in ballast condition (or a part load), the wake fraction tends to be 5–15% larger than the wake fraction in the loaded condition. The value can be determined by equation of Moor and O’Connor [9]. Algorithm determining the relationship between velocity - revolution - engine power Algorithm determining the relationship between velocity - revolution - engine power in the still water is presented in [4]. In other operation condition, algorithm is the same one, therefore, it is no longer necessary to discuss about it. Essential input parameters for determining the relationship between velocity - revolution - engine power include: geometric parameters of ship hull and propeller, wave and wind level, water depth, geometric parameters of canal ship pass through. Example. Using above theory to calculate the relationship between velocity - revolution - engine power of bulk carrier 34000DWT built in PhaRung Shipyard [7]. Input parameters: L = 179.95 m; Lpp = 176,75 m; B = 30 m; TF = 9,75 m; TA = 9,75 m; T =9,75 m; CB = 0,8137; CWP = 0,9606; CM = 0,995; XB = 3,849 m; ABT = 14,85 m2; hB = 5,85 m; Cstern = -22; DP = 5,6 m; Z = 4; Zp = 1; P/D = 0,73; AE/AO = 0,85. Operation condition: when a ship is in the wave and wind h3% = 6 m, wave propagation compared to ship movement βw = 1350, ship type ks =1, wind velocity VW = 19 m/s; when a ship is in the shallow water: water depth h = 13m; when a ship is in the canal having following parameters: depth hK = 25 m; surface width Bw = 50 m; bottom width BB = 40 m; limited velocity in the canal VKP1 = 6 m/s; when a ship is in ballast condition: ship draft Ti = 5.51 m. The calculation results are shown in fig.3. Figure 3 The relationship curves between ship velocity - revolution - engine power in different operation condition 370 2.2.2. Building the characteristics of MPP by experimental method In operation condition, in some allowable regime, we measure three basic parameters: Engine power DME, propeller revolution and ship velocity. By using measured figures (or indirect calculating), some above parameters allow us to estimate the cooperation of components in MPP. Regression model is built based on database measured in experimental condition, using LSEM. - The propeller characteristics is built by model, formula (4); - Engine power can be indirectly calculated or measure by available devices; - Character V =V(n) is modelled in the form of straight line, formula (7). 2.3. Selection the reasonable revolution for operation of MPP Based on modelling the limited characteristics of ship diesel MPP, working characters of ship hull, propeller in the current operation condition (as well as prognose working characters of ship hull, propeller in the alleged condition) allow us to give database ZREF (reference) in order to make a decision of selecting the reasonable operation regime. In the Fig.4, we suggest a principle scheme of the automatic selecting the reasonable operation mode of the MPP, using a electronic governor with the regime (revolution) selection. The Fig.4, we show the principle of controlling revolution of the DME by speed governor including MPU (Magnet Pulse Unit) and FVC (Frequency to Voltage Convector). The control signals DME in the modern diesel engine are usually fuel oil rack and scavenge air pressure (relative quantities are abbreviated by and ). Based on the decision of optimal selection signal op, the desired signal XD impacts on the PID – controller as a revolution error input. Block optimum solution (BOS) in above principle diagram plays a key role in selecting the reasonable revolution condition for operation. Input data for BOS is information of current operation condition with the limited condition of X0 and database as well as character S.F.O.C. of engine. BOS will put forward the best reasonable mode according to the optimal standard so that controlling function is established, for instance, minimum fuel consumption in the safe range of system, or possible maximum velocity in the scope for MPP working safely. Figure 4 Principle scheme of the automatic selecting the reasonable operation mode of the MPP 371 Standard database includes: The limited characters {[Ne], [Np], [V]} and character SFOC ge, that are regressive models, some of them are shown in the table No1 in the paper; The basic operation characters are built by the analytical method {Ne(, X0), Np(,X0) and V(,X0)}, according to the above mentional bases in the point 2.2. 3. Conclusion This paper builds the system of regression models for limited characteristic curve of DME, limited character of the ship speed when engine works above maximum constant moment characteristic curve; characteristic curve of the S.F.O.C. of DME and propeller characteristic curve in the full loaded condition. Those models have an essential reference data for maintaining the operation mode in a safe and economical way. Based on analytical models determining ship resistance, moment and thrust of propeller in every operation mode MPP will be the prediction of propeller characteristic curve and ship hull so that we are able to select a suitable operation mode. This article puts forward principle diagram of the automatic selecting the reasonable operation regimes; specifically it puts forth round mode of main engine and propeller according to reference data (standard characteristic model system) as well as actual operation mode of ship hull, propeller (these cases depend on working condition vector X of MPP). References [1] Bogdanov H.Marine Energy Equipment (Operation). Military Edition. Sofia, 1983. (In Bulgarian).Богданов Х.Г.Корабни енергични уредби. София, «Военно издателство», 1983. 244 с. [2] Emil Stanchev and others. Dynamic researching on the marine propullsion plants in the exploitation conditions. Military Edition. Sofia, 1982. (In Bulgarian). Емил Станчев и др. Динамични изледвания на корабния пропилсивен комплекс в эксплуатационни условия. София, «Военно издателство», 1982. – 284 с. [3] Ovsianicov M. and Petukhov V. Marine propulsion plants. Leningrad, 1987. (In Russian). Овсянников М.К, Петухов В.А. Дизели в пропульсивном комплексе морских судов: Справочник. Л.: Судостроение, 1987. 256 с. [4] LuuD.D., Nho L.C, Tu Tr.Ng.Modelling characteristics of the hull and propeller of sea-going general cargo ship in normal operating conditions. Maritime Science-Technology Journal, N46, March 2016 (VietNam). ISBN. [5] MAN DIESEL 6S46 MC-C. VOLUME I. Operation. [6] Hồ sơ tàu 34000 DWT. Technical File 6S46 MC MK II. HHM–Shanghai Hujiang Diesel Emission Test Scie-Tech Co.Ltd. Approved DNV 20 -08-2007. [7] Hồ sơ tàu 34000 DWT. Hồ sơ thử tàu 34000 DWT. NMĐT Phà Rừng.2007. [8] Hồ sơ tàu 34000 DWT. Torsional Vibration Calculation Report DE 6S46MC –C7860 kW @ 129 r/min 34,000 DWT. HUDONG HEAVY MACHINERY Co. Ltd. PhaRung Shipyard. DNV (Classification Society) Approved 2007 - 06 -06. [9] Molland, Anthony F. Ship resistance and propulsion: practical estimation of ship propulsive power . ISBN 978-0-521-76052-2 (hardback). [10] Под ред. Я.И. Войткунского. Справочник по теории корабля: В трех томах. Том 1. Гидромеханика. Сопротивление движению судов. Судовые движители. (1985). Л.: Судостроение - 768 с. [11] В.Ф. Бавин, В.И. Зайков и др.; Под ред. В.Г. Павленко.Ходкость и управляемость судов (1991). Учебник для вузов/ – М.: Транспорт. 1991. 397 с. [12] Гайкович А.И. Теория проектирования водоизмещающих коряблей и судов. TOM 2: Изд. НИЦ МОРИНТЕХ, 2014.
File đính kèm:
modelling_reasonable_operation_regimes_of_the_main_propulsio.pdf