Validation and calibration of diesel engine model using DME
Diesel engines are utilized in most of heavy duty vehicles due to their high efficiency and
performance. However, fossil fuel is being depleted currently, and emissions from diesel engine contains
many toxic substances such as CO, HC, NOx, PM which effect adversely on environment and human
health. Therefore, research and application of renewable alternative fuels are under consideration in
many countries and Vietnam as well. Recently, Dimethyl ether (DME) has been considered as a potential
alternative fuel for diesel engine. DME can be produced from a variety of raw materials such as biomass,
coal and natural gas. It is also easy to liquefy and suitable to use in diesel engines. DME is not a nature
product but a synthetic product is produced either through the dehydration of methanol or a direct
synthesis from syngas. Using DME for diesel engine may reduce not only dependence on fossil fuel but
also environmental pollution. Certain amounts of DME have been commercially produced as a
propellant for spray cans because of its non-toxicity and suitable solubility and vapor pressure at room
temperature. Some experimental investigations were conducted on diesel engine to clarify how DME
injection characteristics affect the engine performance and exhaust emissions. Most of the results
showed that emissions when fueled DME reduced significantly, especially CO and soot.
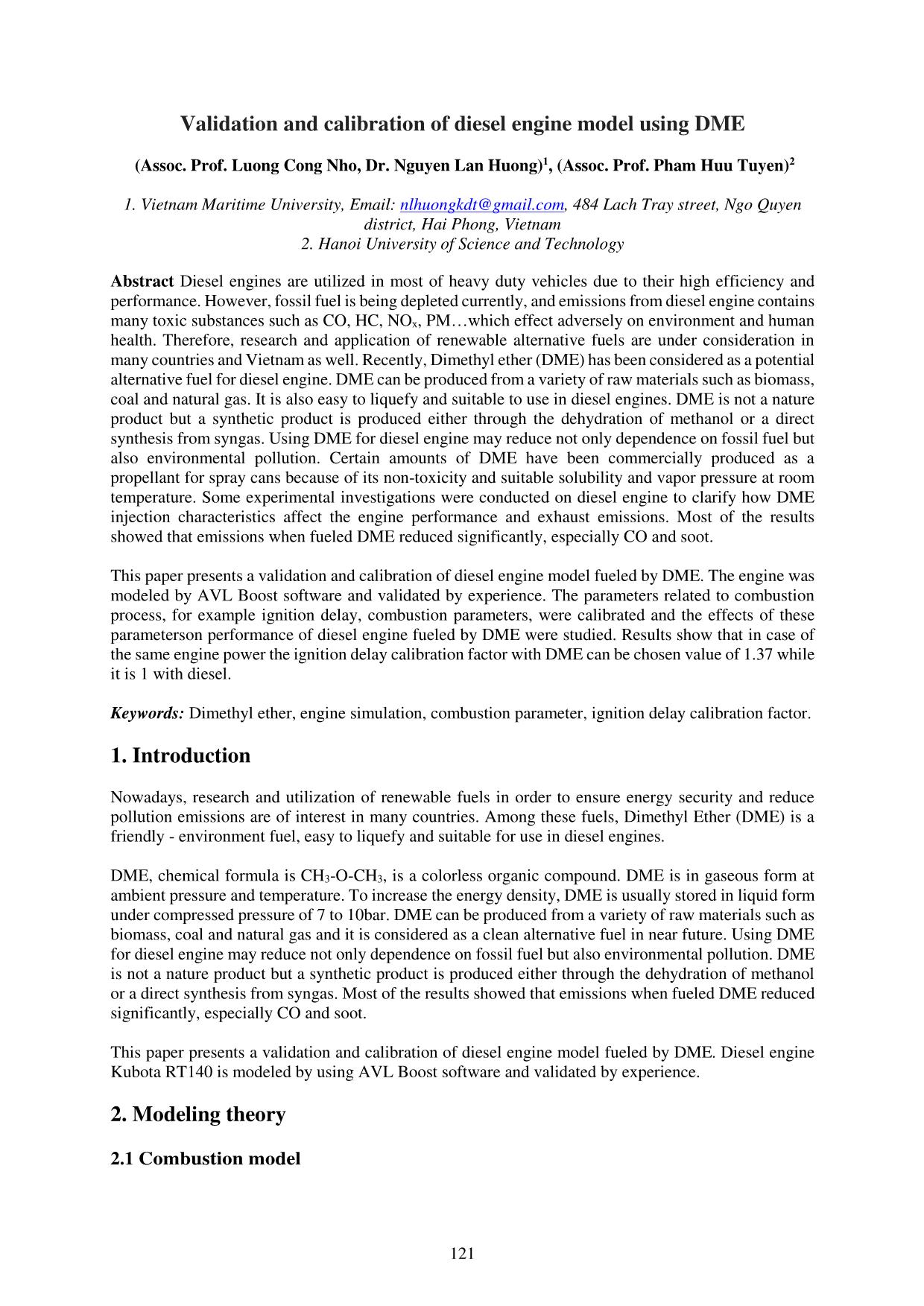
Trang 1
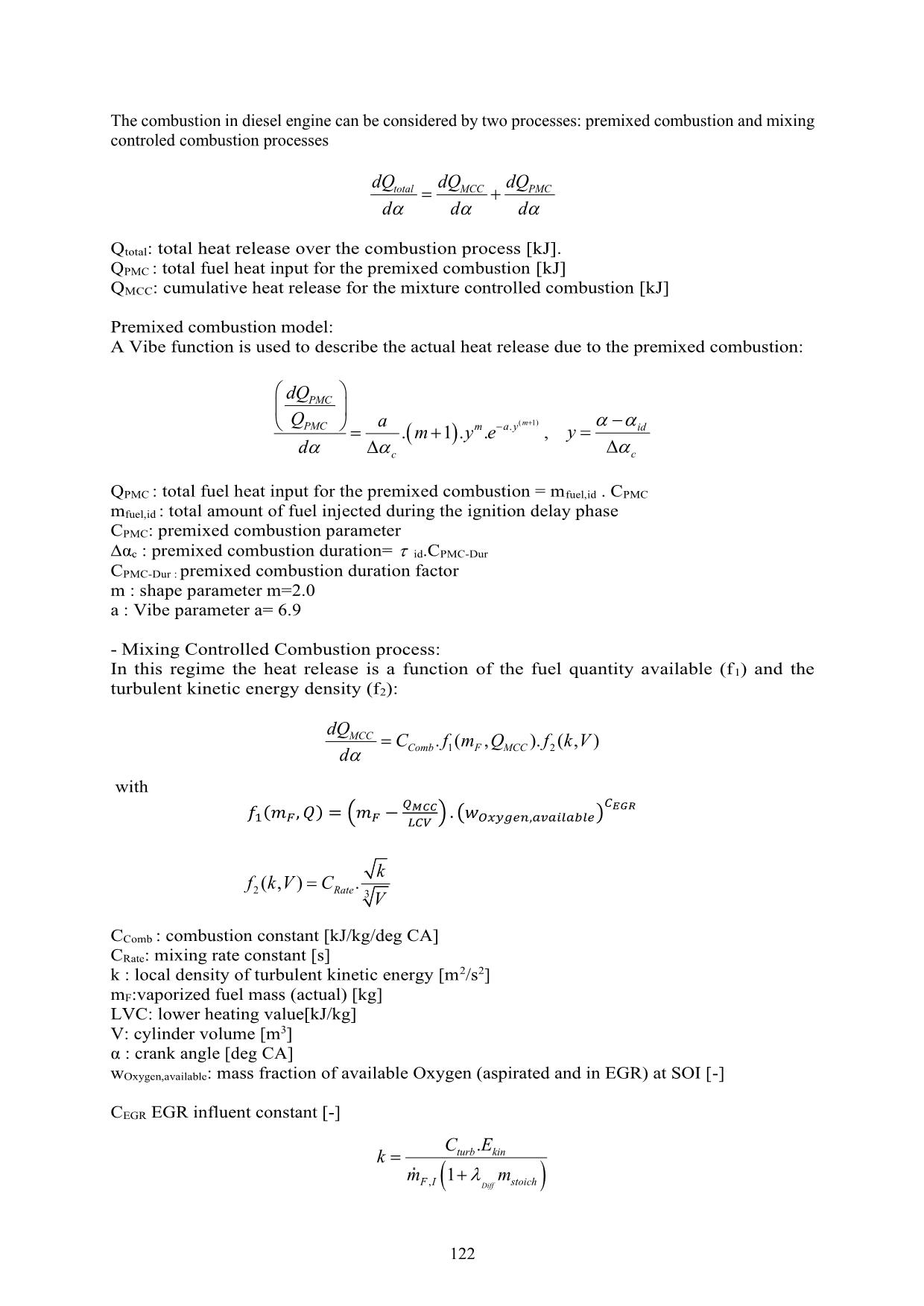
Trang 2
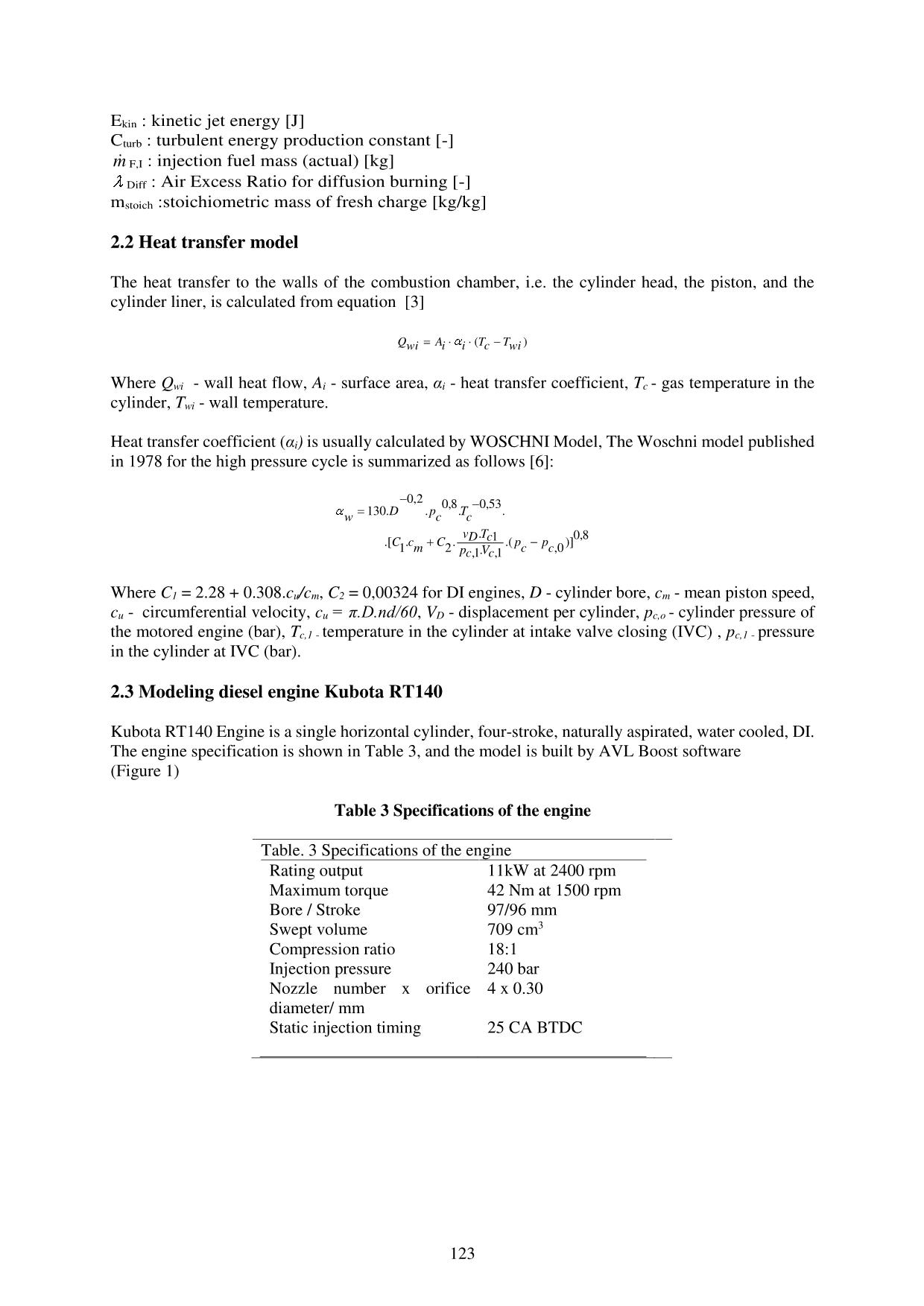
Trang 3
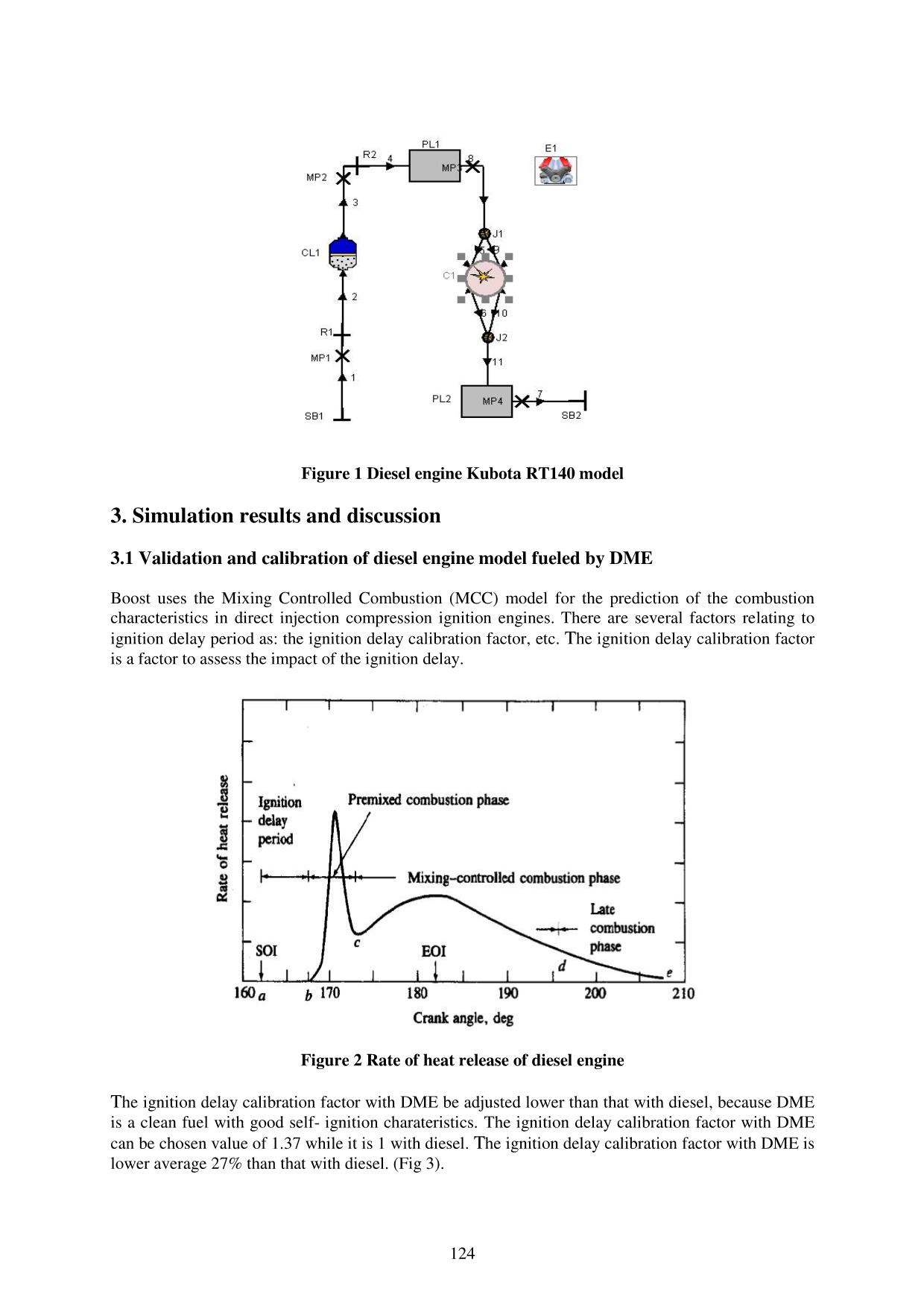
Trang 4
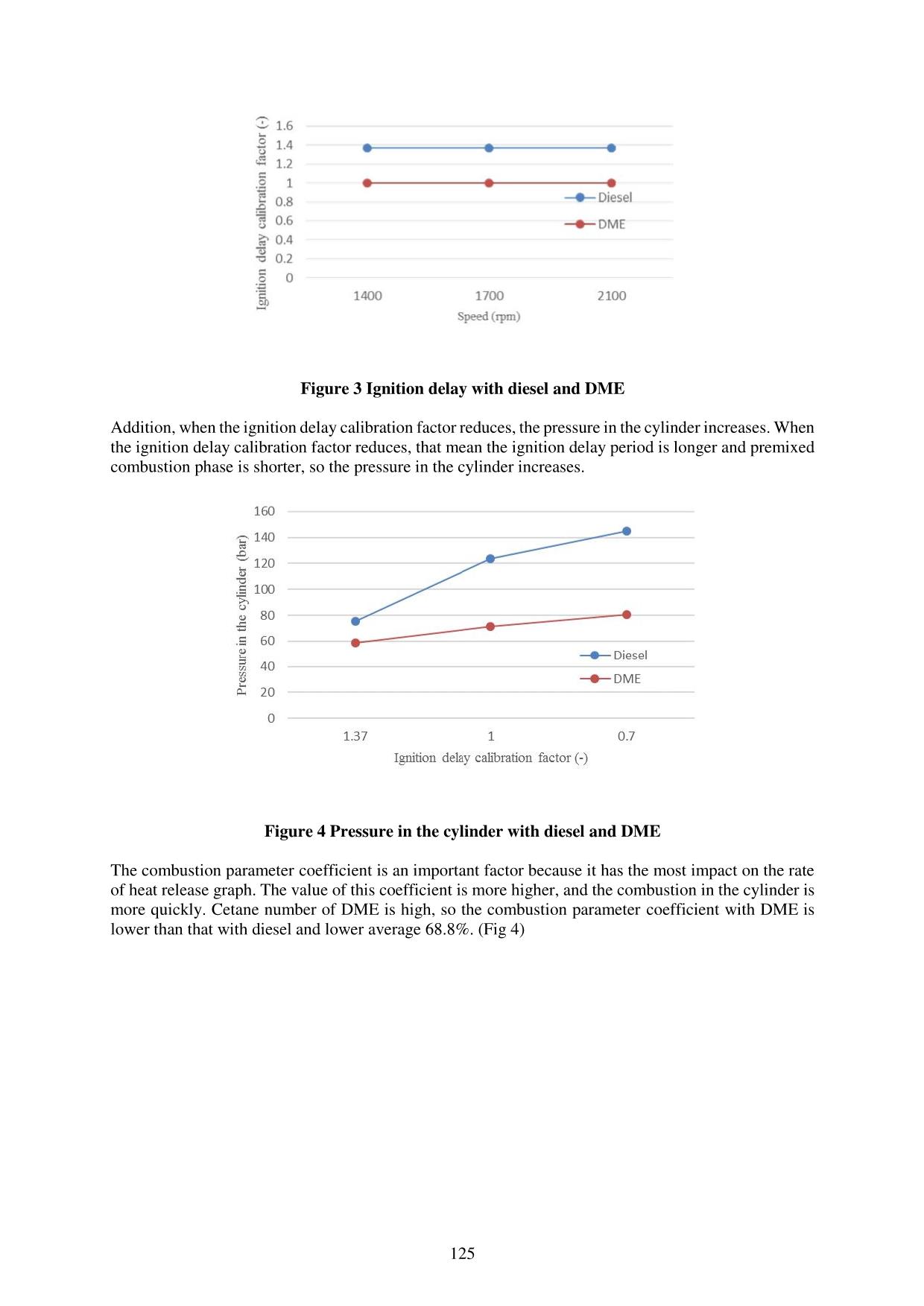
Trang 5
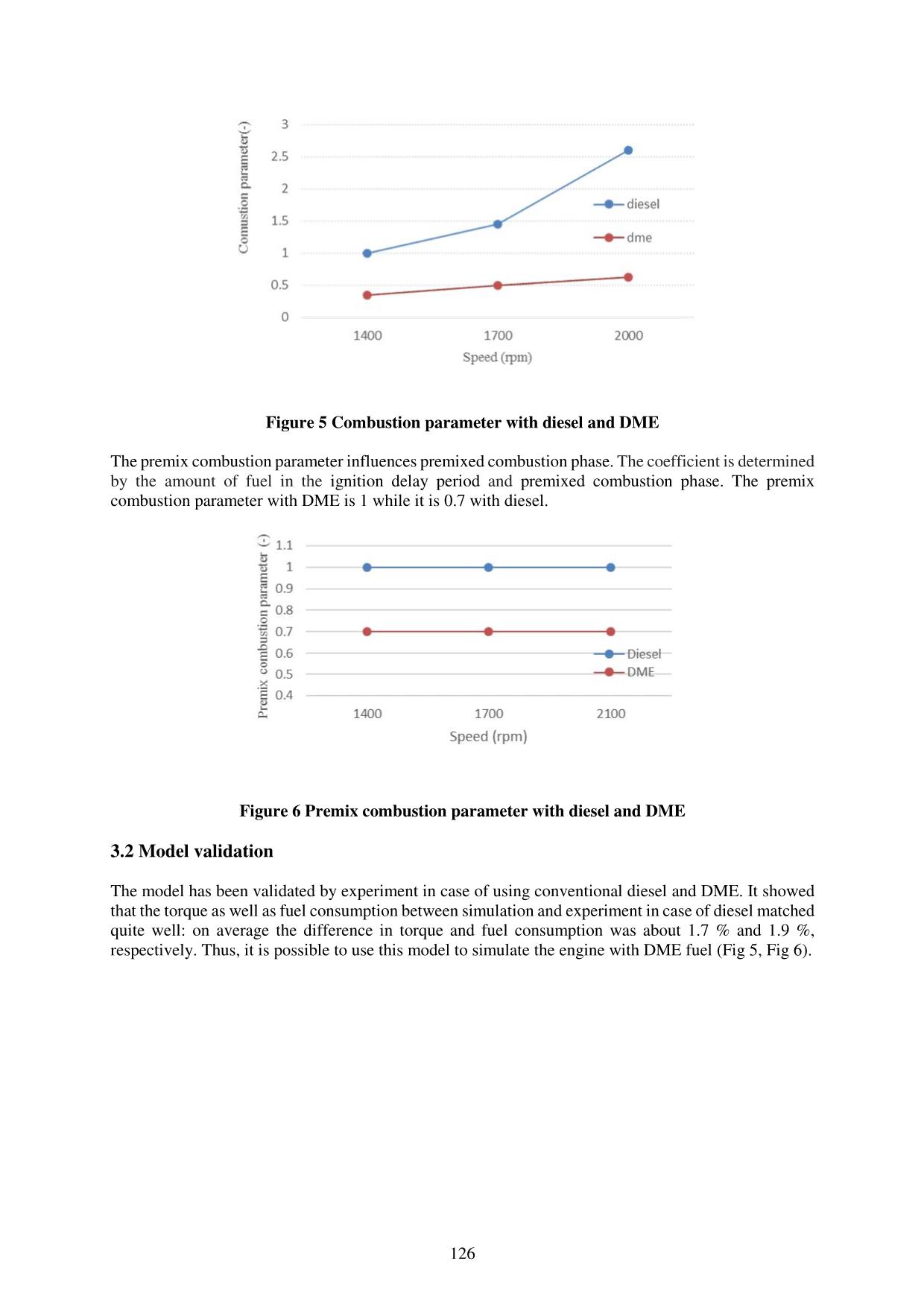
Trang 6

Trang 7
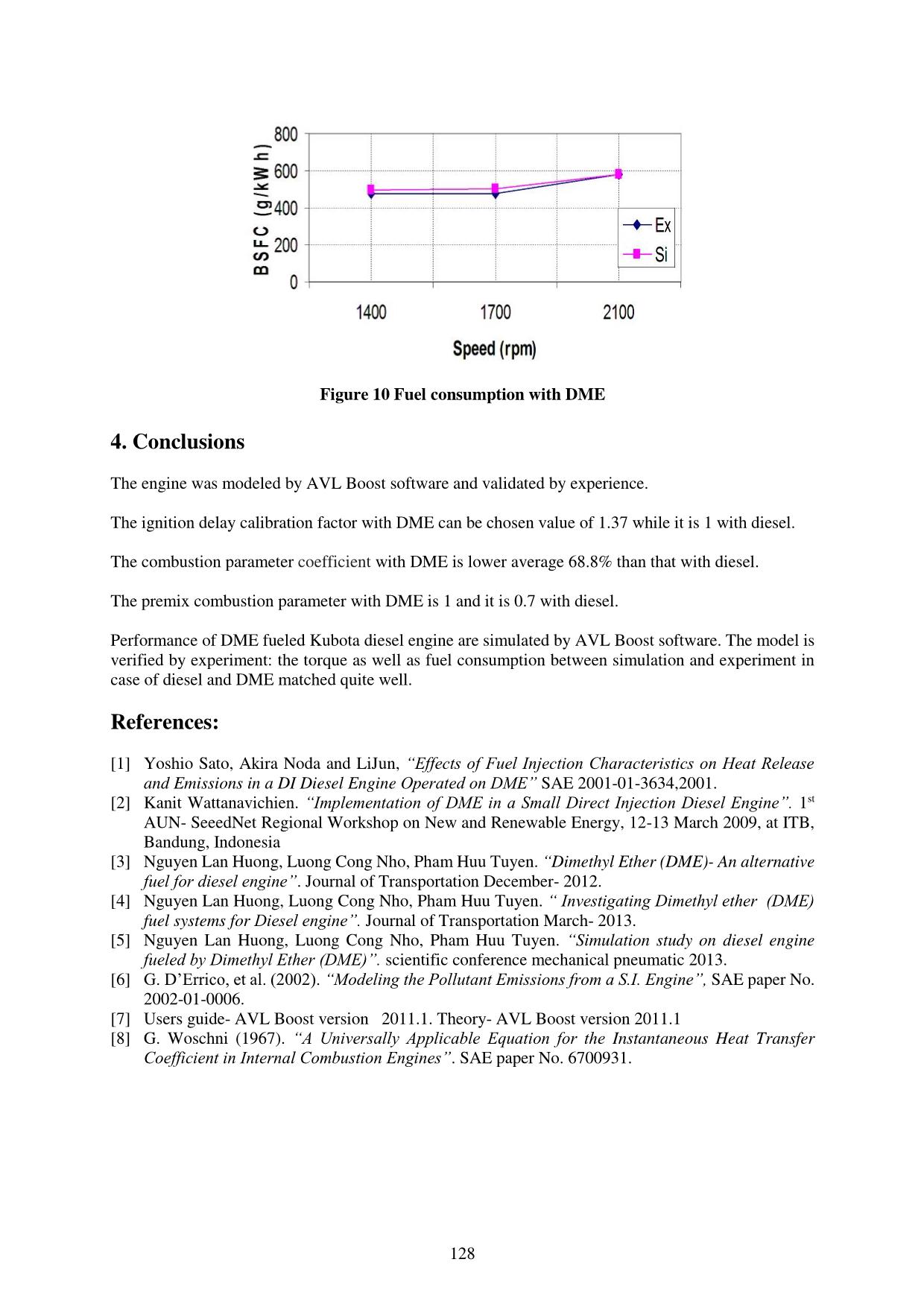
Trang 8
Tóm tắt nội dung tài liệu: Validation and calibration of diesel engine model using DME
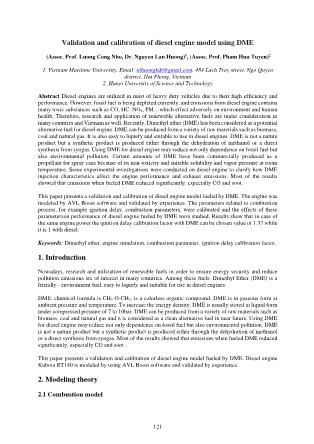
121 Validation and calibration of diesel engine model using DME (Assoc. Prof. Luong Cong Nho, Dr. Nguyen Lan Huong)1, (Assoc. Prof. Pham Huu Tuyen)2 1. Vietnam Maritime University, Email: nlhuongkdt@gmail.com, 484 Lach Tray street, Ngo Quyen district, Hai Phong, Vietnam 2. Hanoi University of Science and Technology Abstract Diesel engines are utilized in most of heavy duty vehicles due to their high efficiency and performance. However, fossil fuel is being depleted currently, and emissions from diesel engine contains many toxic substances such as CO, HC, NOx, PMwhich effect adversely on environment and human health. Therefore, research and application of renewable alternative fuels are under consideration in many countries and Vietnam as well. Recently, Dimethyl ether (DME) has been considered as a potential alternative fuel for diesel engine. DME can be produced from a variety of raw materials such as biomass, coal and natural gas. It is also easy to liquefy and suitable to use in diesel engines. DME is not a nature product but a synthetic product is produced either through the dehydration of methanol or a direct synthesis from syngas. Using DME for diesel engine may reduce not only dependence on fossil fuel but also environmental pollution. Certain amounts of DME have been commercially produced as a propellant for spray cans because of its non-toxicity and suitable solubility and vapor pressure at room temperature. Some experimental investigations were conducted on diesel engine to clarify how DME injection characteristics affect the engine performance and exhaust emissions. Most of the results showed that emissions when fueled DME reduced significantly, especially CO and soot. This paper presents a validation and calibration of diesel engine model fueled by DME. The engine was modeled by AVL Boost software and validated by experience. The parameters related to combustion process, for example ignition delay, combustion parameters, were calibrated and the effects of these parameterson performance of diesel engine fueled by DME were studied. Results show that in case of the same engine power the ignition delay calibration factor with DME can be chosen value of 1.37 while it is 1 with diesel. Keywords: Dimethyl ether, engine simulation, combustion parameter, ignition delay calibration factor. 1. Introduction Nowadays, research and utilization of renewable fuels in order to ensure energy security and reduce pollution emissions are of interest in many countries. Among these fuels, Dimethyl Ether (DME) is a friendly - environment fuel, easy to liquefy and suitable for use in diesel engines. DME, chemical formula is CH3-O-CH3, is a colorless organic compound. DME is in gaseous form at ambient pressure and temperature. To increase the energy density, DME is usually stored in liquid form under compressed pressure of 7 to 10bar. DME can be produced from a variety of raw materials such as biomass, coal and natural gas and it is considered as a clean alternative fuel in near future. Using DME for diesel engine may reduce not only dependence on fossil fuel but also environmental pollution. DME is not a nature product but a synthetic product is produced either through the dehydration of methanol or a direct synthesis from syngas. Most of the results showed that emissions when fueled DME reduced significantly, especially CO and soot. This paper presents a validation and calibration of diesel engine model fueled by DME. Diesel engine Kubota RT140 is modeled by using AVL Boost software and validated by experience. 2. Modeling theory 2.1 Combustion model 122 1 2. ( , ). ( , ) MCC Comb F MCC dQ C f m Q f k V d 2 3 ( , ) .Rate k f k V C V , . 1 Diff turb kin F I stoich C E k m m The combustion in diesel engine can be considered by two processes: premixed combustion and mixing controled combustion processes total MCC PMCdQ dQ dQ d d d Qtotal: total heat release over the combustion process [kJ]. QPMC : total fuel heat input for the premixed combustion [kJ] QMCC: cumulative heat release for the mixture controlled combustion [kJ] Premixed combustion model: A Vibe function is used to describe the actual heat release due to the premixed combustion: ( 1).. 1 . . m PMC PMC m a y c dQ Q a m y e d , id c y QPMC : total fuel heat input for the premixed combustion = mfuel,id . CPMC mfuel,id : total amount of fuel injected during the ignition delay phase CPMC: premixed combustion parameter ∆αc : premixed combustion duration= id.CPMC-Dur CPMC-Dur : premixed combustion duration factor m : shape parameter m=2.0 a : Vibe parameter a= 6.9 - Mixing Controlled Combustion process: In this regime the heat release is a function of the fuel quantity available (f1) and the turbulent kinetic energy density (f2): with 𝑓1(𝑚𝐹 , 𝑄) = (𝑚𝐹 − 𝑄𝑀𝐶𝐶 𝐿𝐶𝑉 ) . (𝑤𝑂𝑥𝑦𝑔𝑒𝑛,𝑎𝑣𝑎𝑖𝑙𝑎𝑏𝑙𝑒) 𝐶𝐸𝐺𝑅 CComb : combustion constant [kJ/kg/deg CA] CRate: mixing rate constant [s] k : local density of turbulent kinetic energy [m2/s2] mF:vaporized fuel mass (actual) [kg] LVC: lower heating value[kJ/kg] V: cylinder volume [m3] α : crank angle [deg CA] wOxygen,available: mass fraction of available Oxygen (aspirated and in EGR) at SOI [-] CEGR EGR influent constant [-] 123 Ekin : kinetic jet energy [J] Cturb : turbulent energy production constant [-] F,I : injection fuel mass (actual) [kg] Diff : Air Excess Ratio for diffusion burning [-] mstoich :stoichiometric mass of fresh charge [kg/kg] 2.2 Heat transfer model The heat transfer to the walls of the combustion chamber, i.e. the cylinder head, the piston, and the cylinder liner, is calculated from equation [3] ( )Q A T Tcwi i i wi Where Qwi - wall heat flow, Ai - surface area, αi - heat transfer coefficient, Tc - gas temperature in the cylinder, Twi - wall temperature. Heat transfer coefficient (αi) is usually calculated by WOSCHNI Model, The Woschni model published in 1978 for the high pressure cycle is summarized as follows [6]: 0,2 0,8 0,53130. . . . . 0,81 .[ . . .( )]1 2 ,0 .,1 ,1 D p T w c c v TD cC c C p p m c cp Vc c Where C1 = 2.28 + 0.308.cu/cm, C2 = 0,00324 for DI engines, D - cylinder bore, cm - mean piston speed, cu - circumferential velocity, cu = π.D.nd/60, VD - displacement per cylinder, pc,o - cylinder pressure of the motored engine (bar), Tc,1 - temperature in the cylinder at intake valve closing (IVC) , pc,1 - pressure in the cylinder at IVC (bar). 2.3 Modeling diesel engine Kubota RT140 Kubota RT140 Engine is a single horizontal cylinder, four-stroke, naturally aspirated, water cooled, DI. The engine specification is shown in Table 3, and the model is built by AVL Boost software (Figure 1) Table 3 Specifications of the engine Table. 3 Specifications of the engine Rating output Maximum torque Bore / Stroke Swept volume Compression ratio Injection pressure Nozzle number x orifice diameter/ mm Static injection timing 11kW at 2400 rpm 42 Nm at 1500 rpm 97/96 mm 709 cm3 18:1 240 bar 4 x 0.30 25 CA BTDC m 124 Figure 1 Diesel engine Kubota RT140 model 3. Simulation results and discussion 3.1 Validation and calibration of diesel engine model fueled by DME Boost uses the Mixing Controlled Combustion (MCC) model for the prediction of the combustion characteristics in direct injection compression ignition engines. There are several factors relating to ignition delay period as: the ignition delay calibration factor, etc. The ignition delay calibration factor is a factor to assess the impact of the ignition delay. Figure 2 Rate of heat release of diesel engine The ignition delay calibration factor with DME be adjusted lower than that with diesel, because DME is a clean fuel with good self- ignition charateristics. The ignition delay calibration factor with DME can be chosen value of 1.37 while it is 1 with diesel. The ignition delay calibration factor with DME is lower average 27% than that with diesel. (Fig 3). 125 Figure 3 Ignition delay with diesel and DME Addition, when the ignition delay calibration factor reduces, the pressure in the cylinder increases. When the ignition delay calibration factor reduces, that mean the ignition delay period is longer and premixed combustion phase is shorter, so the pressure in the cylinder increases. Figure 4 Pressure in the cylinder with diesel and DME The combustion parameter coefficient is an important factor because it has the most impact on the rate of heat release graph. The value of this coefficient is more higher, and the combustion in the cylinder is more quickly. Cetane number of DME is high, so the combustion parameter coefficient with DME is lower than that with diesel and lower average 68.8%. (Fig 4) 126 Figure 5 Combustion parameter with diesel and DME The premix combustion parameter influences premixed combustion phase. The coefficient is determined by the amount of fuel in the ignition delay period and premixed combustion phase. The premix combustion parameter with DME is 1 while it is 0.7 with diesel. Figure 6 Premix combustion parameter with diesel and DME 3.2 Model validation The model has been validated by experiment in case of using conventional diesel and DME. It showed that the torque as well as fuel consumption between simulation and experiment in case of diesel matched quite well: on average the difference in torque and fuel consumption was about 1.7 % and 1.9 %, respectively. Thus, it is possible to use this model to simulate the engine with DME fuel (Fig 5, Fig 6). 127 Figure 7 Torque with diesel Figure 8 Fuel consumption with diesel In case of DME, the torque as well as fuel consumption between simulation and experiment are similar, on average the difference in torque and fuel consumption was about 1.7 % and 3.1 % (Fig 7, Fig 8). Figure 9 Torque with DME 128 Figure 10 Fuel consumption with DME 4. Conclusions The engine was modeled by AVL Boost software and validated by experience. The ignition delay calibration factor with DME can be chosen value of 1.37 while it is 1 with diesel. The combustion parameter coefficient with DME is lower average 68.8% than that with diesel. The premix combustion parameter with DME is 1 and it is 0.7 with diesel. Performance of DME fueled Kubota diesel engine are simulated by AVL Boost software. The model is verified by experiment: the torque as well as fuel consumption between simulation and experiment in case of diesel and DME matched quite well. References: [1] Yoshio Sato, Akira Noda and LiJun, “Effects of Fuel Injection Characteristics on Heat Release and Emissions in a DI Diesel Engine Operated on DME” SAE 2001-01-3634,2001. [2] Kanit Wattanavichien. “Implementation of DME in a Small Direct Injection Diesel Engine”. 1st AUN- SeeedNet Regional Workshop on New and Renewable Energy, 12-13 March 2009, at ITB, Bandung, Indonesia [3] Nguyen Lan Huong, Luong Cong Nho, Pham Huu Tuyen. “Dimethyl Ether (DME)- An alternative fuel for diesel engine”. Journal of Transportation December- 2012. [4] Nguyen Lan Huong, Luong Cong Nho, Pham Huu Tuyen. “ Investigating Dimethyl ether (DME) fuel systems for Diesel engine”. Journal of Transportation March- 2013. [5] Nguyen Lan Huong, Luong Cong Nho, Pham Huu Tuyen. “Simulation study on diesel engine fueled by Dimethyl Ether (DME)”. scientific conference mechanical pneumatic 2013. [6] G. D’Errico, et al. (2002). “Modeling the Pollutant Emissions from a S.I. Engine”, SAE paper No. 2002-01-0006. [7] Users guide- AVL Boost version 2011.1. Theory- AVL Boost version 2011.1 [8] G. Woschni (1967). “A Universally Applicable Equation for the Instantaneous Heat Transfer Coefficient in Internal Combustion Engines”. SAE paper No. 6700931.
File đính kèm:
validation_and_calibration_of_diesel_engine_model_using_dme.pdf