Effect of epoxydized carbon nanotube master batch on polypropylene film properties
First, the surface of carbon nanotubes (CNTs) was modified by epoxidation reaction to create epoxidized CNTs
(O
were prepared by melt mixing in the presence of anhydride grafted polypropylene (PPgMAH). The CNTs content
dispersed uniformly in master batch is 7 wt%. Finally, the effect of MB-O
polypropylene film (PP film) was studied. The PP film samples with different MB-O
O
contents on the mechanical, thermal and electrical properties of PP film samples were investigated. The study found that
tensile strength of PP films increased significantly with increasing O
decreased. In addition, the presence of O
temperature of PP films while the melting behavior did not change much. From FE-SEM analysis, the good dispersion
of O
presence of O
O
O
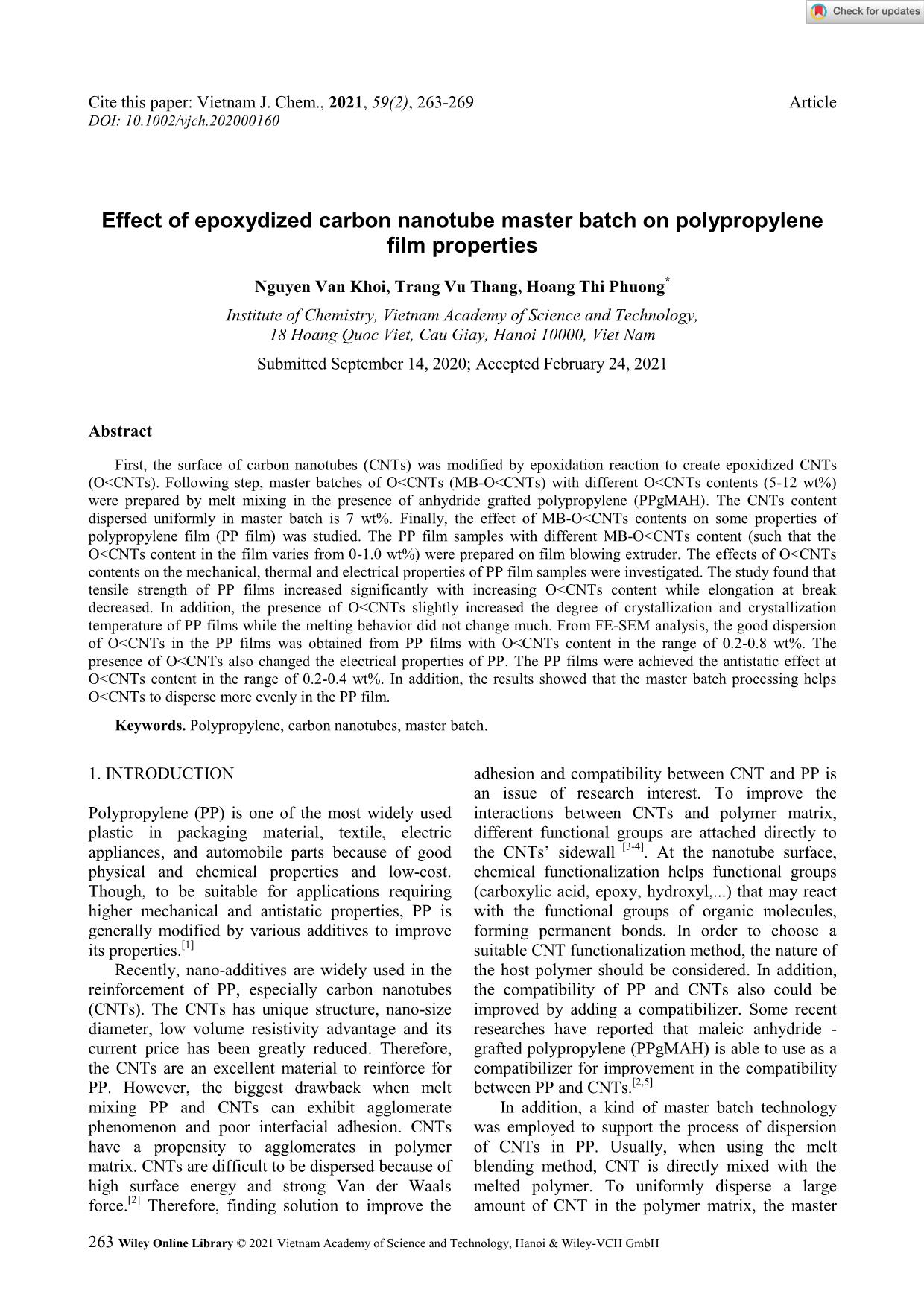
Trang 1
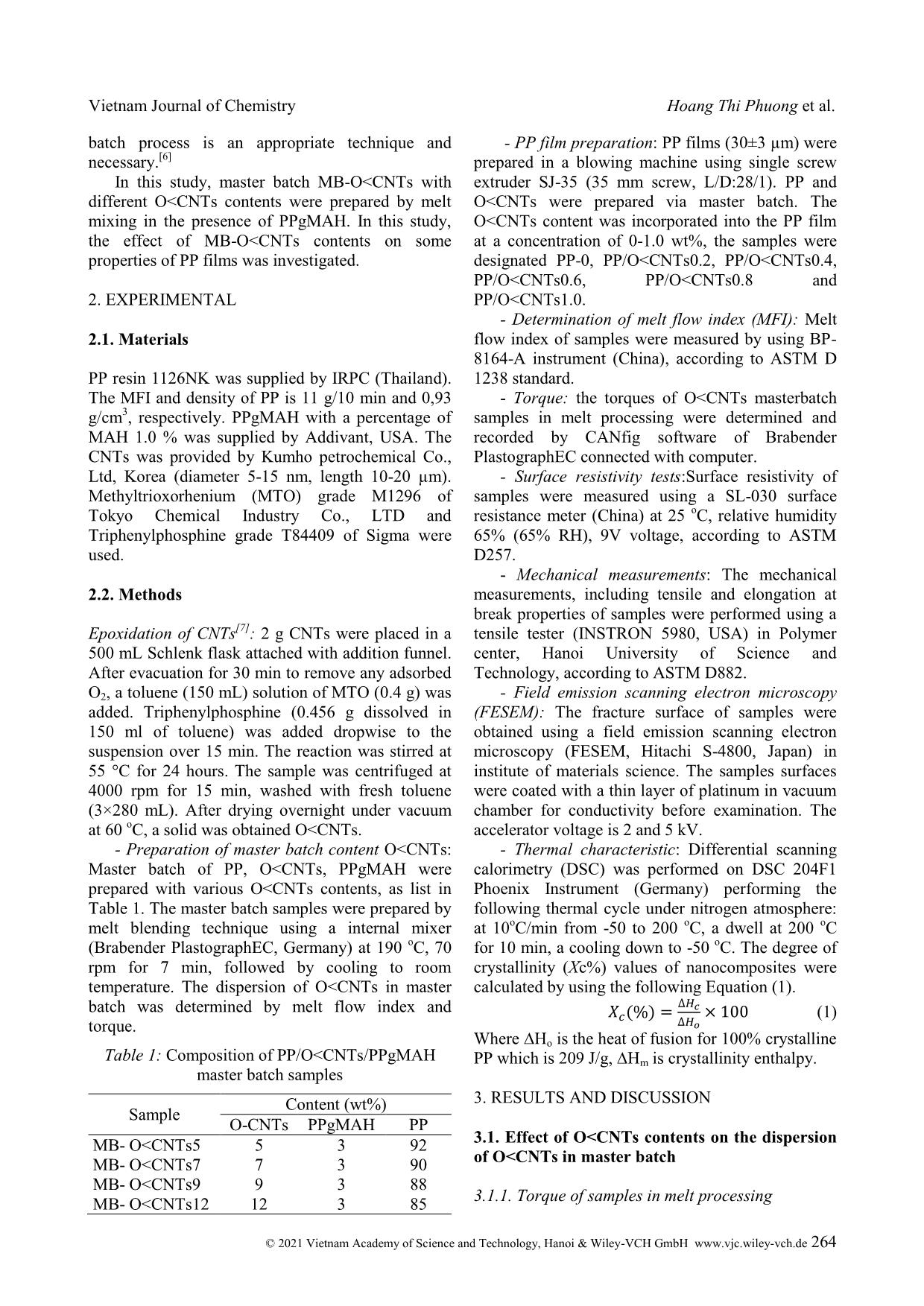
Trang 2
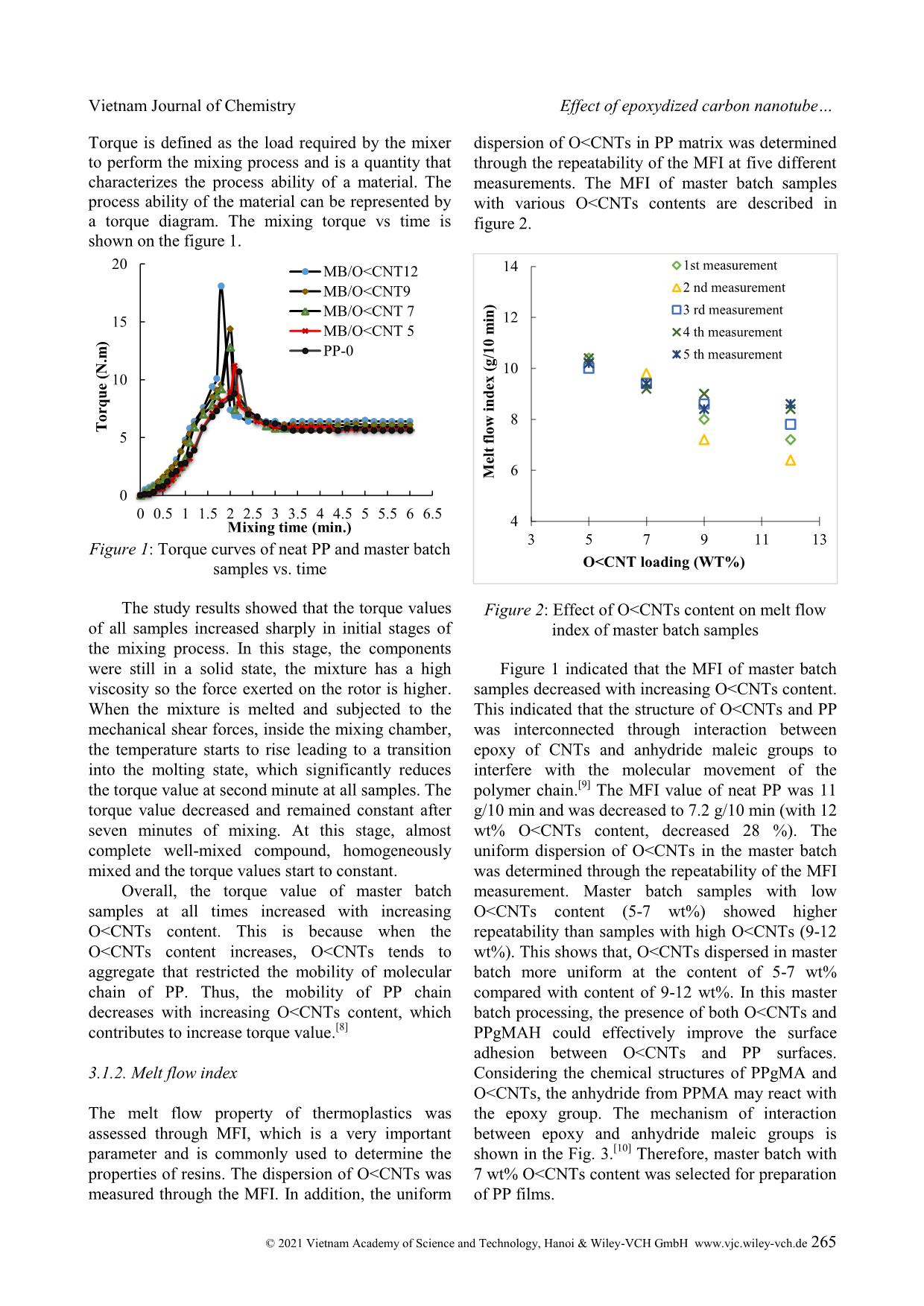
Trang 3
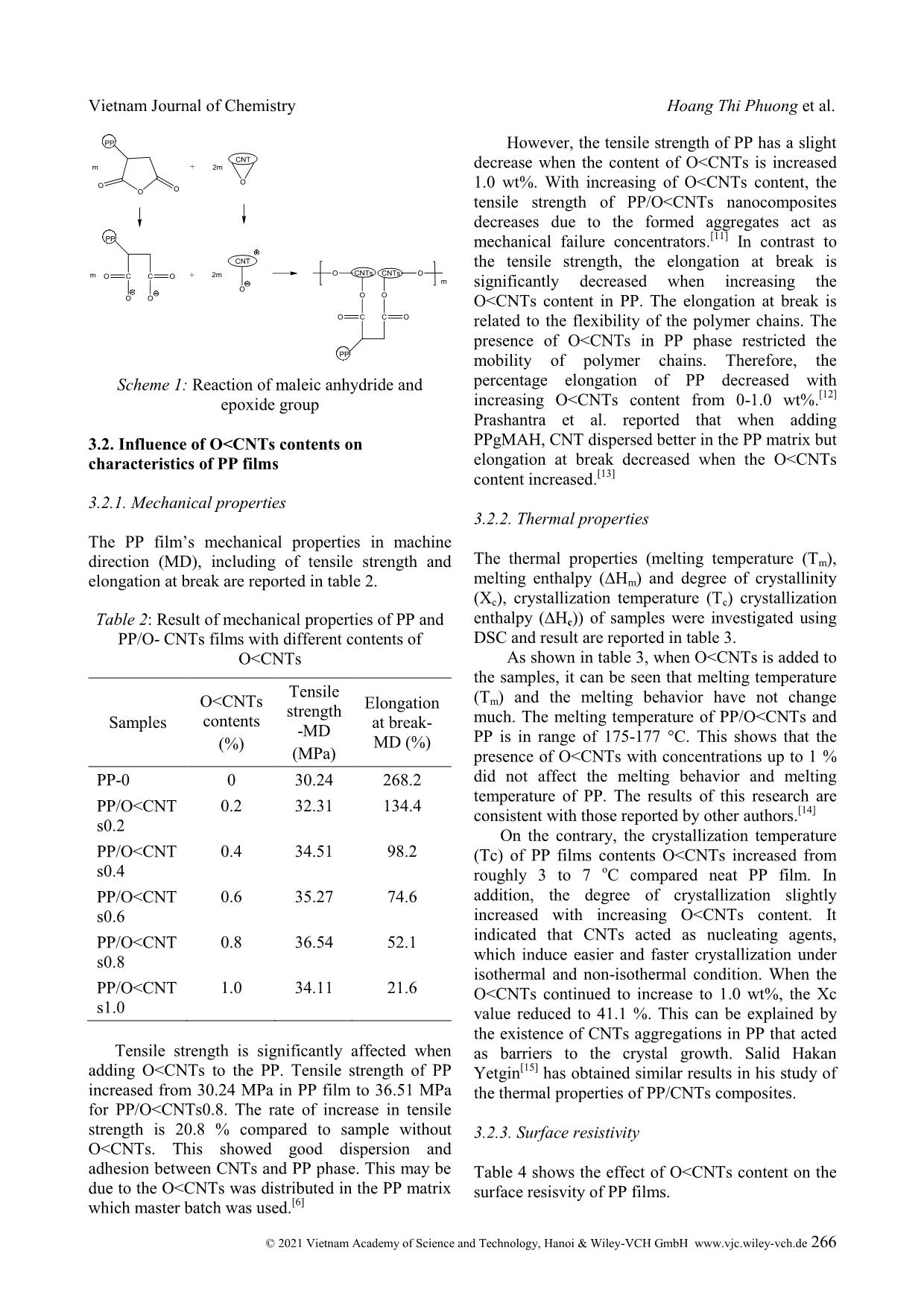
Trang 4
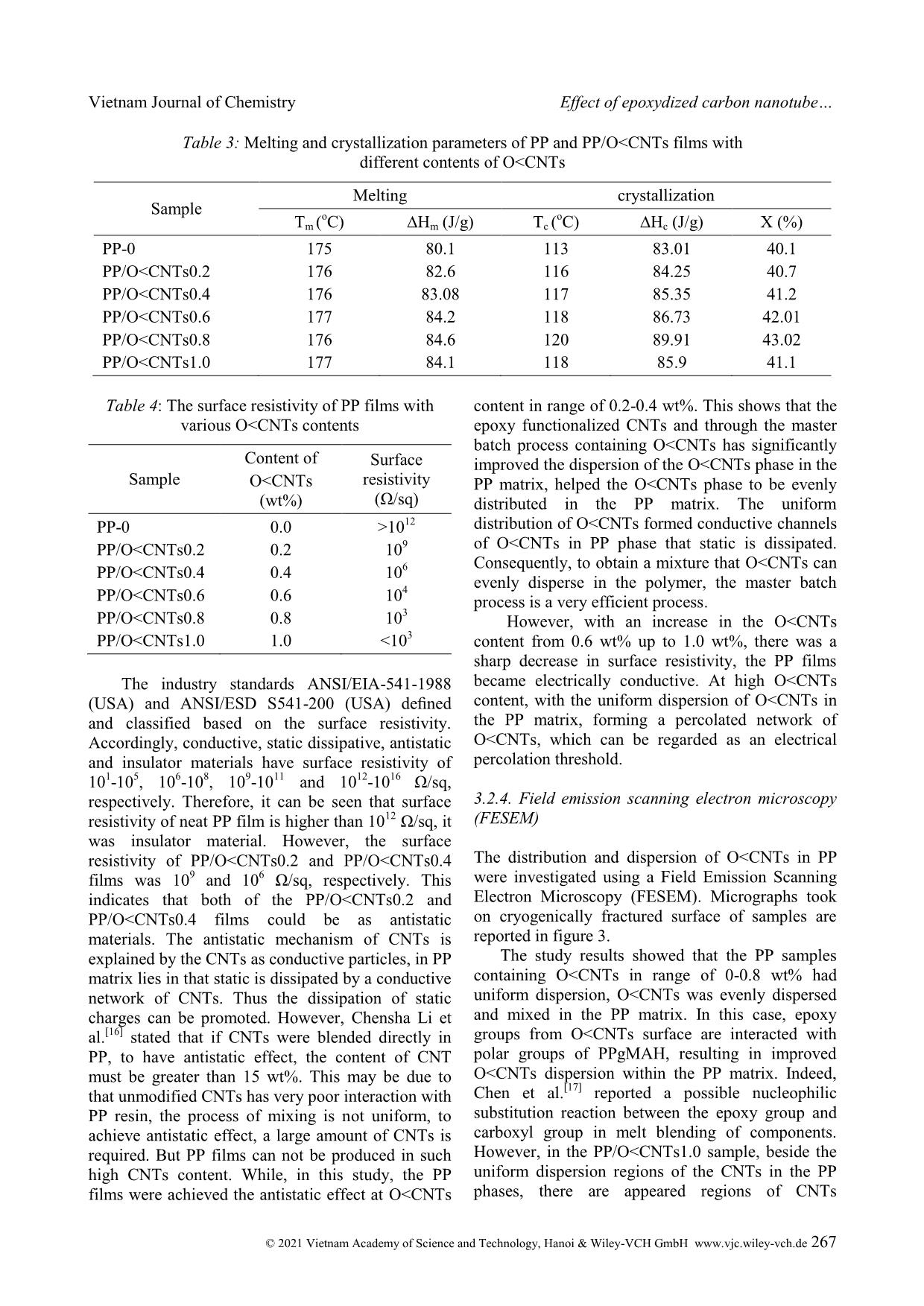
Trang 5
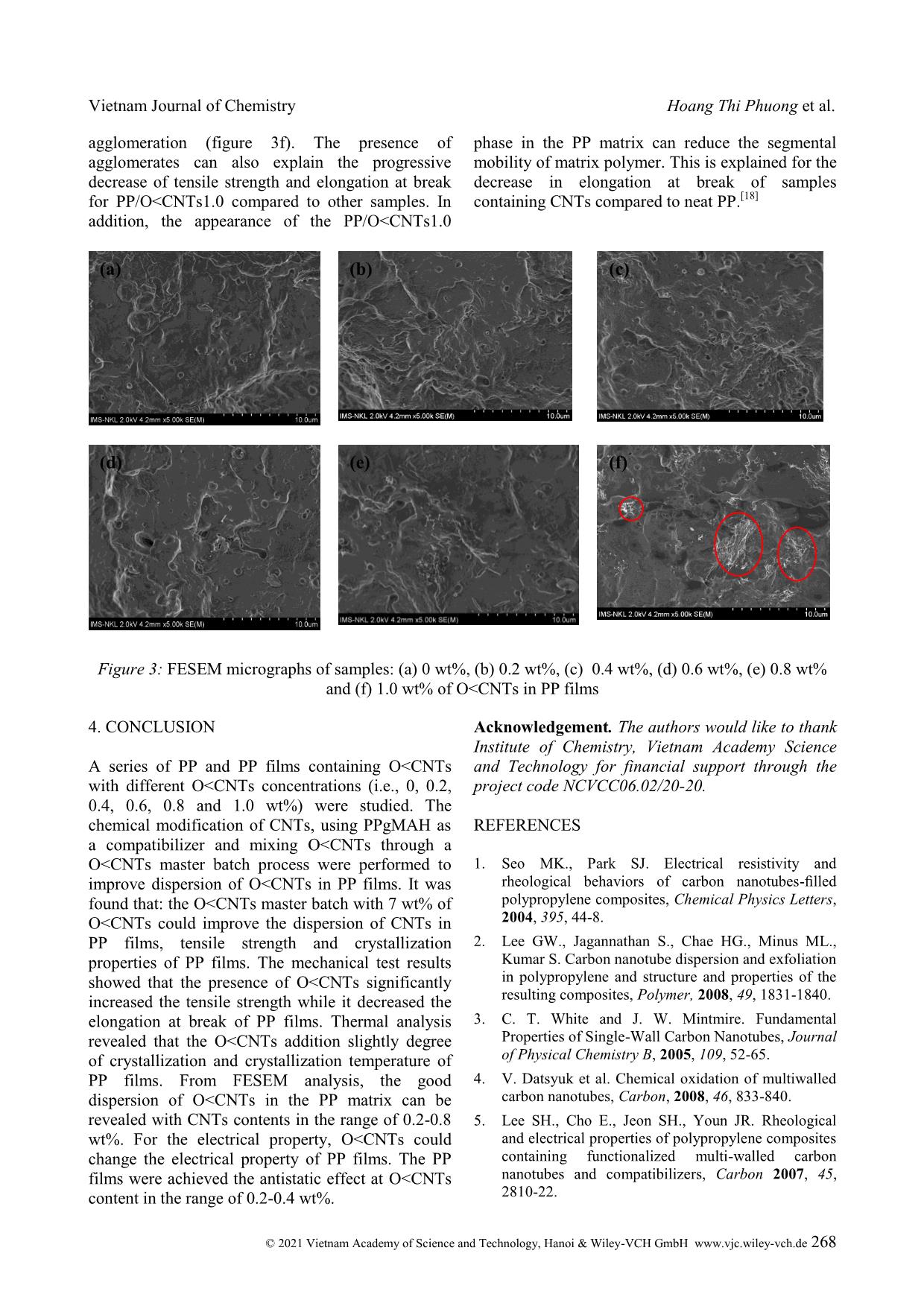
Trang 6
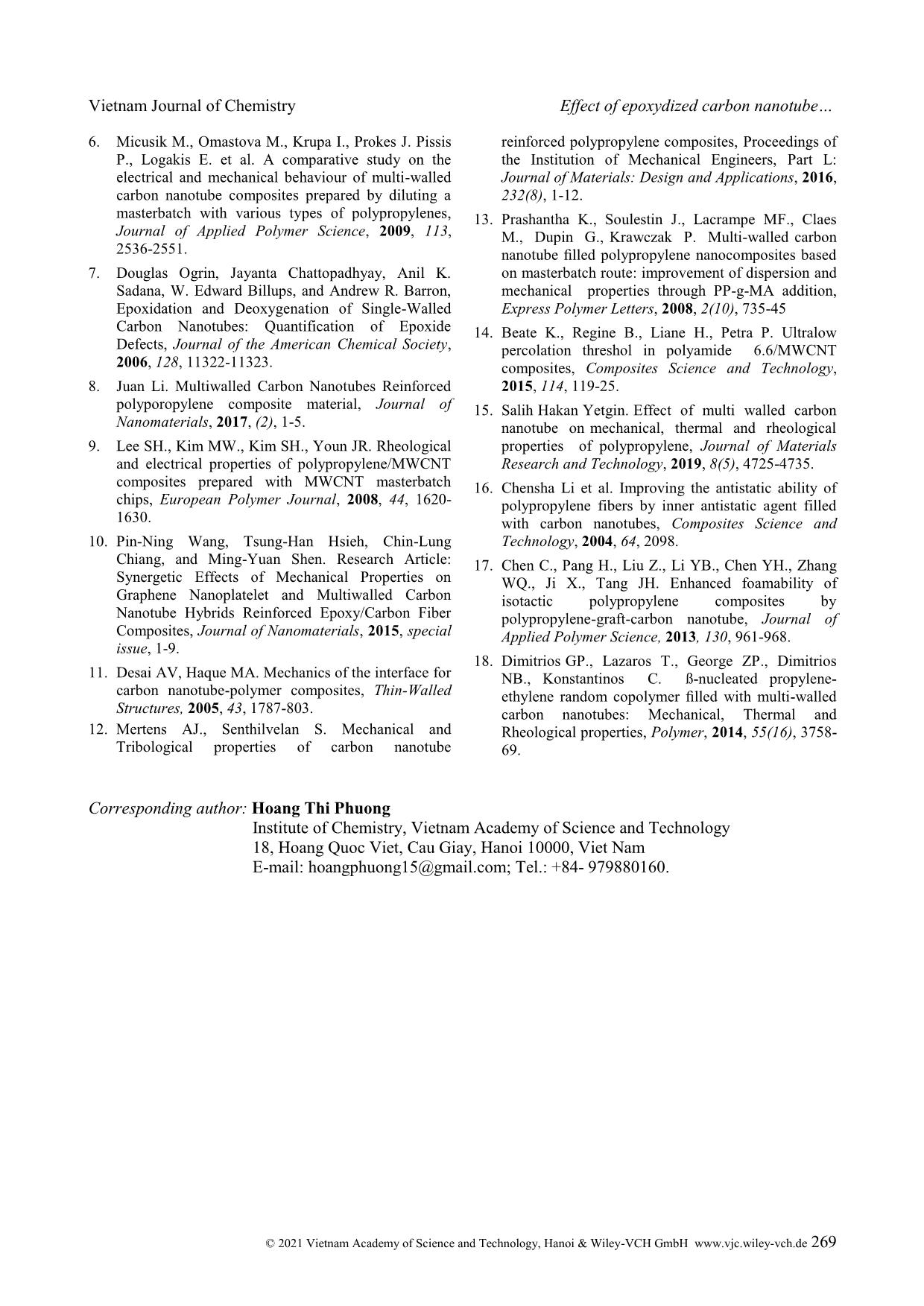
Trang 7
Tóm tắt nội dung tài liệu: Effect of epoxydized carbon nanotube master batch on polypropylene film properties
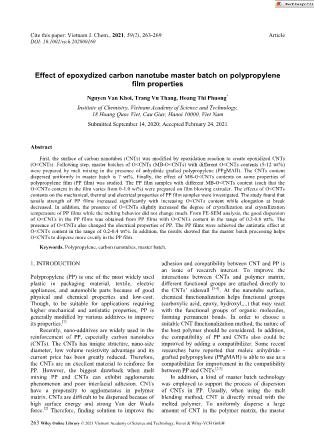
Cite this paper: Vietnam J. Chem., 2021, 59(2), 263-269 Article DOI: 10.1002/vjch.202000160 263 Wiley Online Library © 2021 Vietnam Academy of Science and Technology, Hanoi & Wiley-VCH GmbH Effect of epoxydized carbon nanotube master batch on polypropylene film properties Nguyen Van Khoi, Trang Vu Thang, Hoang Thi Phuong * Institute of Chemistry, Vietnam Academy of Science and Technology, 18 Hoang Quoc Viet, Cau Giay, Hanoi 10000, Viet Nam Submitted September 14, 2020; Accepted February 24, 2021 Abstract First, the surface of carbon nanotubes (CNTs) was modified by epoxidation reaction to create epoxidized CNTs (O<CNTs). Following step, master batches of O<CNTs (MB-O<CNTs) with different O<CNTs contents (5-12 wt%) were prepared by melt mixing in the presence of anhydride grafted polypropylene (PPgMAH). The CNTs content dispersed uniformly in master batch is 7 wt%. Finally, the effect of MB-O<CNTs contents on some properties of polypropylene film (PP film) was studied. The PP film samples with different MB-O<CNTs content (such that the O<CNTs content in the film varies from 0-1.0 wt%) were prepared on film blowing extruder. The effects of O<CNTs contents on the mechanical, thermal and electrical properties of PP film samples were investigated. The study found that tensile strength of PP films increased significantly with increasing O<CNTs content while elongation at break decreased. In addition, the presence of O<CNTs slightly increased the degree of crystallization and crystallization temperature of PP films while the melting behavior did not change much. From FE-SEM analysis, the good dispersion of O<CNTs in the PP films was obtained from PP films with O<CNTs content in the range of 0.2-0.8 wt%. The presence of O<CNTs also changed the electrical properties of PP. The PP films were achieved the antistatic effect at O<CNTs content in the range of 0.2-0.4 wt%. In addition, the results showed that the master batch processing helps O<CNTs to disperse more evenly in the PP film. Keywords. Polypropylene, carbon nanotubes, master batch. 1. INTRODUCTION Polypropylene (PP) is one of the most widely used plastic in packaging material, textile, electric appliances, and automobile parts because of good physical and chemical properties and low-cost. Though, to be suitable for applications requiring higher mechanical and antistatic properties, PP is generally modified by various additives to improve its properties. [1] Recently, nano-additives are widely used in the reinforcement of PP, especially carbon nanotubes (CNTs). The CNTs has unique structure, nano-size diameter, low volume resistivity advantage and its current price has been greatly reduced. Therefore, the CNTs are an excellent material to reinforce for PP. However, the biggest drawback when melt mixing PP and CNTs can exhibit agglomerate phenomenon and poor interfacial adhesion. CNTs have a propensity to agglomerates in polymer matrix. CNTs are difficult to be dispersed because of high surface energy and strong Van der Waals force. [2] Therefore, finding solution to improve the adhesion and compatibility between CNT and PP is an issue of research interest. To improve the interactions between CNTs and polymer matrix, different functional groups are attached directly to the CNTs’ sidewall [3-4]. At the nanotube surface, chemical functionalization helps functional groups (carboxylic acid, epoxy, hydroxyl,...) that may react with the functional groups of organic molecules, forming permanent bonds. In order to choose a suitable CNT functionalization method, the nature of the host polymer should be considered. In addition, the compatibility of PP and CNTs also could be improved by adding a compatibilizer. Some recent researches have reported that maleic anhydride - grafted polypropylene (PPgMAH) is able to use as a compatibilizer for improvement in the compatibility between PP and CNTs. [2,5] In addition, a kind of master batch technology was employed to support the process of dispersion of CNTs in PP. Usually, when using the melt blending method, CNT is directly mixed with the melted polymer. To uniformly disperse a large amount of CNT in the polymer matrix, the master Vietnam Journal of Chemistry Hoang Thi Phuong et al. © 2021 Vietnam Academy of Science and Technology, Hanoi & Wiley-VCH GmbH www.vjc.wiley-vch.de 264 batch process is an appropriate technique and necessary. [6] In this study, master batch MB-O<CNTs with different O<CNTs contents were prepared by melt mixing in the presence of PPgMAH. In this study, the effect of MB-O<CNTs contents on some properties of PP films was investigated. 2. EXPERIMENTAL 2.1. Materials PP resin 1126NK was supplied by IRPC (Thailand). The MFI and density of PP is 11 g/10 min and 0,93 g/cm 3 , respectively. PPgMAH with a percentage of MAH 1.0 % was supplied by Addivant, USA. The CNTs was provided by Kumho petrochemical Co., Ltd, Korea (diameter 5-15 nm, length 10-20 µm). Methyltrioxorhenium (MTO) grade M1296 of Tokyo Chemical Industry Co., LTD and Triphenylphosphine grade T84409 of Sigma were used. 2.2. Methods Epoxidation of CNTs [7] : 2 g CNTs were placed in a 500 mL Schlenk flask attached with addition funnel. After evacuation for 30 min to remove any adsorbed O2, a toluene (150 mL) solution of MTO (0.4 g) was added. Triphenylphosphine (0.456 g dissolved in 150 ml of toluene) was added dropwise to the suspension over 15 min. The reaction was stirred at 55 °C for 24 hours. The sample was centrifuged at 4000 rpm for 15 min, washed with fresh toluene (3×280 mL). After drying overnight under vacuum at 60 o C, a solid was obtained O<CNTs. - Preparation of master batch content O<CNTs: Master batch of PP, O<CNTs, PPgMAH were prepared ... Samples O<CNTs contents (%) Tensile strength -MD (MPa) Elongation at break- MD (%) PP-0 0 30.24 268.2 PP/O<CNT s0.2 0.2 32.31 134.4 PP/O<CNT s0.4 0.4 34.51 98.2 PP/O<CNT s0.6 0.6 35.27 74.6 PP/O<CNT s0.8 0.8 36.54 52.1 PP/O<CNT s1.0 1.0 34.11 21.6 Tensile strength is significantly affected when adding O<CNTs to the PP. Tensile strength of PP increased from 30.24 MPa in PP film to 36.51 MPa for PP/O<CNTs0.8. The rate of increase in tensile strength is 20.8 % compared to sample without O<CNTs. This showed good dispersion and adhesion between CNTs and PP phase. This may be due to the O<CNTs was distributed in the PP matrix which master batch was used. [6] However, the tensile strength of PP has a slight decrease when the content of O<CNTs is increased 1.0 wt%. With increasing of O<CNTs content, the tensile strength of PP/O<CNTs nanocomposites decreases due to the formed aggregates act as mechanical failure concentrators. [11] In contrast to the tensile strength, the elongation at break is significantly decreased when increasing the O<CNTs content in PP. The elongation at break is related to the flexibility of the polymer chains. The presence of O<CNTs in PP phase restricted the mobility of polymer chains. Therefore, the percentage elongation of PP decreased with increasing O<CNTs content from 0-1.0 wt%. [12] Prashantra et al. reported that when adding PPgMAH, CNT dispersed better in the PP matrix but elongation at break decreased when the O<CNTs content increased. [13] 3.2.2. Thermal properties The thermal properties (melting temperature (Tm), melting enthalpy (∆Hm) and degree of crystallinity (Xc), crystallization temperature (Tc) crystallization enthalpy (∆Hc)) of samples were investigated using DSC and result are reported in table 3. As shown in table 3, when O<CNTs is added to the samples, it can be seen that melting temperature (Tm) and the melting behavior have not change much. The melting temperature of PP/O<CNTs and PP is in range of 175-177 °C. This shows that the presence of O<CNTs with concentrations up to 1 % did not affect the melting behavior and melting temperature of PP. The results of this research are consistent with those reported by other authors. [14] On the contrary, the crystallization temperature (Tc) of PP films contents O<CNTs increased from roughly 3 to 7 o C compared neat PP film. In addition, the degree of crystallization slightly increased with increasing O<CNTs content. It indicated that CNTs acted as nucleating agents, which induce easier and faster crystallization under isothermal and non-isothermal condition. When the O<CNTs continued to increase to 1.0 wt%, the Xc value reduced to 41.1 %. This can be explained by the existence of CNTs aggregations in PP that acted as barriers to the crystal growth. Salid Hakan Yetgin [15] has obtained similar results in his study of the thermal properties of PP/CNTs composites. 3.2.3. Surface resistivity Table 4 shows the effect of O<CNTs content on the surface resisvity of PP films. Vietnam Journal of Chemistry Effect of epoxydized carbon nanotube © 2021 Vietnam Academy of Science and Technology, Hanoi & Wiley-VCH GmbH www.vjc.wiley-vch.de 267 Table 3: Melting and crystallization parameters of PP and PP/O<CNTs films with different contents of O<CNTs Sample Melting crystallization Tm ( o C) ∆Hm (J/g) Tc ( o C) ∆Hc (J/g) X (%) PP-0 175 80.1 113 83.01 40.1 PP/O<CNTs0.2 176 82.6 116 84.25 40.7 PP/O<CNTs0.4 176 83.08 117 85.35 41.2 PP/O<CNTs0.6 177 84.2 118 86.73 42.01 PP/O<CNTs0.8 176 84.6 120 89.91 43.02 PP/O<CNTs1.0 177 84.1 118 85.9 41.1 Table 4: The surface resistivity of PP films with various O<CNTs contents Sample Content of O<CNTs (wt%) Surface resistivity (Ω/sq) PP-0 0.0 >10 12 PP/O<CNTs0.2 0.2 10 9 PP/O<CNTs0.4 0.4 10 6 PP/O<CNTs0.6 0.6 10 4 PP/O<CNTs0.8 0.8 10 3 PP/O<CNTs1.0 1.0 <10 3 The industry standards ANSI/EIA-541-1988 (USA) and ANSI/ESD S541-200 (USA) defined and classified based on the surface resistivity. Accordingly, conductive, static dissipative, antistatic and insulator materials have surface resistivity of 10 1 -10 5 , 10 6 -10 8 , 10 9 -10 11 and 10 12 -10 16 Ω/sq, respectively. Therefore, it can be seen that surface resistivity of neat PP film is higher than 10 12 Ω/sq, it was insulator material. However, the surface resistivity of PP/O<CNTs0.2 and PP/O<CNTs0.4 films was 10 9 and 10 6 Ω/sq, respectively. This indicates that both of the PP/O<CNTs0.2 and PP/O<CNTs0.4 films could be as antistatic materials. The antistatic mechanism of CNTs is explained by the CNTs as conductive particles, in PP matrix lies in that static is dissipated by a conductive network of CNTs. Thus the dissipation of static charges can be promoted. However, Chensha Li et al. [16] stated that if CNTs were blended directly in PP, to have antistatic effect, the content of CNT must be greater than 15 wt%. This may be due to that unmodified CNTs has very poor interaction with PP resin, the process of mixing is not uniform, to achieve antistatic effect, a large amount of CNTs is required. But PP films can not be produced in such high CNTs content. While, in this study, the PP films were achieved the antistatic effect at O<CNTs content in range of 0.2-0.4 wt%. This shows that the epoxy functionalized CNTs and through the master batch process containing O<CNTs has significantly improved the dispersion of the O<CNTs phase in the PP matrix, helped the O<CNTs phase to be evenly distributed in the PP matrix. The uniform distribution of O<CNTs formed conductive channels of O<CNTs in PP phase that static is dissipated. Consequently, to obtain a mixture that O<CNTs can evenly disperse in the polymer, the master batch process is a very efficient process. However, with an increase in the O<CNTs content from 0.6 wt% up to 1.0 wt%, there was a sharp decrease in surface resistivity, the PP films became electrically conductive. At high O<CNTs content, with the uniform dispersion of O<CNTs in the PP matrix, forming a percolated network of O<CNTs, which can be regarded as an electrical percolation threshold. 3.2.4. Field emission scanning electron microscopy (FESEM) The distribution and dispersion of O<CNTs in PP were investigated using a Field Emission Scanning Electron Microscopy (FESEM). Micrographs took on cryogenically fractured surface of samples are reported in figure 3. The study results showed that the PP samples containing O<CNTs in range of 0-0.8 wt% had uniform dispersion, O<CNTs was evenly dispersed and mixed in the PP matrix. In this case, epoxy groups from O<CNTs surface are interacted with polar groups of PPgMAH, resulting in improved O<CNTs dispersion within the PP matrix. Indeed, Chen et al. [17] reported a possible nucleophilic substitution reaction between the epoxy group and carboxyl group in melt blending of components. However, in the PP/O<CNTs1.0 sample, beside the uniform dispersion regions of the CNTs in the PP phases, there are appeared regions of CNTs Vietnam Journal of Chemistry Hoang Thi Phuong et al. © 2021 Vietnam Academy of Science and Technology, Hanoi & Wiley-VCH GmbH www.vjc.wiley-vch.de 268 agglomeration (figure 3f). The presence of agglomerates can also explain the progressive decrease of tensile strength and elongation at break for PP/O<CNTs1.0 compared to other samples. In addition, the appearance of the PP/O<CNTs1.0 phase in the PP matrix can reduce the segmental mobility of matrix polymer. This is explained for the decrease in elongation at break of samples containing CNTs compared to neat PP. [18] Figure 3: FESEM micrographs of samples: (a) 0 wt%, (b) 0.2 wt%, (c) 0.4 wt%, (d) 0.6 wt%, (e) 0.8 wt% and (f) 1.0 wt% of O<CNTs in PP films 4. CONCLUSION A series of PP and PP films containing O<CNTs with different O<CNTs concentrations (i.e., 0, 0.2, 0.4, 0.6, 0.8 and 1.0 wt%) were studied. The chemical modification of CNTs, using PPgMAH as a compatibilizer and mixing O<CNTs through a O<CNTs master batch process were performed to improve dispersion of O<CNTs in PP films. It was found that: the O<CNTs master batch with 7 wt% of O<CNTs could improve the dispersion of CNTs in PP films, tensile strength and crystallization properties of PP films. The mechanical test results showed that the presence of O<CNTs significantly increased the tensile strength while it decreased the elongation at break of PP films. Thermal analysis revealed that the O<CNTs addition slightly degree of crystallization and crystallization temperature of PP films. From FESEM analysis, the good dispersion of O<CNTs in the PP matrix can be revealed with CNTs contents in the range of 0.2-0.8 wt%. For the electrical property, O<CNTs could change the electrical property of PP films. The PP films were achieved the antistatic effect at O<CNTs content in the range of 0.2-0.4 wt%. Acknowledgement. The authors would like to thank Institute of Chemistry, Vietnam Academy Science and Technology for financial support through the project code NCVCC06.02/20-20. REFERENCES 1. Seo MK., Park SJ. Electrical resistivity and rheological behaviors of carbon nanotubes-filled polypropylene composites, Chemical Physics Letters, 2004, 395, 44-8. 2. Lee GW., Jagannathan S., Chae HG., Minus ML., Kumar S. Carbon nanotube dispersion and exfoliation in polypropylene and structure and properties of the resulting composites, Polymer, 2008, 49, 1831-1840. 3. C. T. White and J. W. Mintmire. Fundamental Properties of Single-Wall Carbon Nanotubes, Journal of Physical Chemistry B, 2005, 109, 52-65. 4. V. Datsyuk et al. Chemical oxidation of multiwalled carbon nanotubes, Carbon, 2008, 46, 833-840. 5. Lee SH., Cho E., Jeon SH., Youn JR. Rheological and electrical properties of polypropylene composites containing functionalized multi-walled carbon nanotubes and compatibilizers, Carbon 2007, 45, 2810-22. (a) (b) (c) (d) (e) (f) Vietnam Journal of Chemistry Effect of epoxydized carbon nanotube © 2021 Vietnam Academy of Science and Technology, Hanoi & Wiley-VCH GmbH www.vjc.wiley-vch.de 269 6. Micusik M., Omastova M., Krupa I., Prokes J. Pissis P., Logakis E. et al. A comparative study on the electrical and mechanical behaviour of multi-walled carbon nanotube composites prepared by diluting a masterbatch with various types of polypropylenes, Journal of Applied Polymer Science, 2009, 113, 2536-2551. 7. Douglas Ogrin, Jayanta Chattopadhyay, Anil K. Sadana, W. Edward Billups, and Andrew R. Barron, Epoxidation and Deoxygenation of Single-Walled Carbon Nanotubes: Quantification of Epoxide Defects, Journal of the American Chemical Society, 2006, 128, 11322-11323. 8. Juan Li. Multiwalled Carbon Nanotubes Reinforced polyporopylene composite material, Journal of Nanomaterials, 2017, (2), 1-5. 9. Lee SH., Kim MW., Kim SH., Youn JR. Rheological and electrical properties of polypropylene/MWCNT composites prepared with MWCNT masterbatch chips, European Polymer Journal, 2008, 44, 1620- 1630. 10. Pin-Ning Wang, Tsung-Han Hsieh, Chin-Lung Chiang, and Ming-Yuan Shen. Research Article: Synergetic Effects of Mechanical Properties on Graphene Nanoplatelet and Multiwalled Carbon Nanotube Hybrids Reinforced Epoxy/Carbon Fiber Composites, Journal of Nanomaterials, 2015, special issue, 1-9. 11. Desai AV, Haque MA. Mechanics of the interface for carbon nanotube-polymer composites, Thin-Walled Structures, 2005, 43, 1787-803. 12. Mertens AJ., Senthilvelan S. Mechanical and Tribological properties of carbon nanotube reinforced polypropylene composites, Proceedings of the Institution of Mechanical Engineers, Part L: Journal of Materials: Design and Applications, 2016, 232(8), 1-12. 13. Prashantha K., Soulestin J., Lacrampe MF., Claes M., Dupin G., Krawczak P. Multi-walled carbon nanotube filled polypropylene nanocomposites based on masterbatch route: improvement of dispersion and mechanical properties through PP-g-MA addition, Express Polymer Letters, 2008, 2(10), 735-45 14. Beate K., Regine B., Liane H., Petra P. Ultralow percolation threshol in polyamide 6.6/MWCNT composites, Composites Science and Technology, 2015, 114, 119-25. 15. Salih Hakan Yetgin. Effect of multi walled carbon nanotube on mechanical, thermal and rheological properties of polypropylene, Journal of Materials Research and Technology, 2019, 8(5), 4725-4735. 16. Chensha Li et al. Improving the antistatic ability of polypropylene fibers by inner antistatic agent filled with carbon nanotubes, Composites Science and Technology, 2004, 64, 2098. 17. Chen C., Pang H., Liu Z., Li YB., Chen YH., Zhang WQ., Ji X., Tang JH. Enhanced foamability of isotactic polypropylene composites by polypropylene-graft-carbon nanotube, Journal of Applied Polymer Science, 2013, 130, 961-968. 18. Dimitrios GP., Lazaros T., George ZP., Dimitrios NB., Konstantinos C. ß-nucleated propylene- ethylene random copolymer filled with multi-walled carbon nanotubes: Mechanical, Thermal and Rheological properties, Polymer, 2014, 55(16), 3758- 69. Corresponding author: Hoang Thi Phuong Institute of Chemistry, Vietnam Academy of Science and Technology 18, Hoang Quoc Viet, Cau Giay, Hanoi 10000, Viet Nam E-mail: hoangphuong15@gmail.com; Tel.: +84- 979880160.
File đính kèm:
effect_of_epoxydized_carbon_nanotube_master_batch_on_polypro.pdf