Characteristics of hydroxyapatite coating on Ti-6Al-4V substrate fabricated via sequent H2O2-oxidizing and RF-sputtering processes
In this study, we created a hydroxyapatite (HAp) coating layer on top of the Ti-6Al-4V substrate via sequent H2O2-
oxidizing and RF-sputtering processes and determining the effect of H2O2-oxidizing state to the adhesion between HAp
coating layer and Ti-6Al-4V substrate. The results showed that the H2O2-oxidized Ti-6Al-4V surface is rough and
porous, which increases the adhesion strength of the HAp coating layer on the alloy substrate. The shear strength value
of the HAp/H2O2-oxidized Ti-6Al-4V substrate was 69.3 MPa, significantly higher than that of the HAp/original Ti-
6Al-4V substrate (12.9 MPa). The X-ray photoelectron spectroscopy (XPS) proved the denser HAp coating layer
covered the TiO2/Ti-6Al-4V substrate, consequently effectively prevented releasing of the unwanted toxic elements
from the metallic implant.
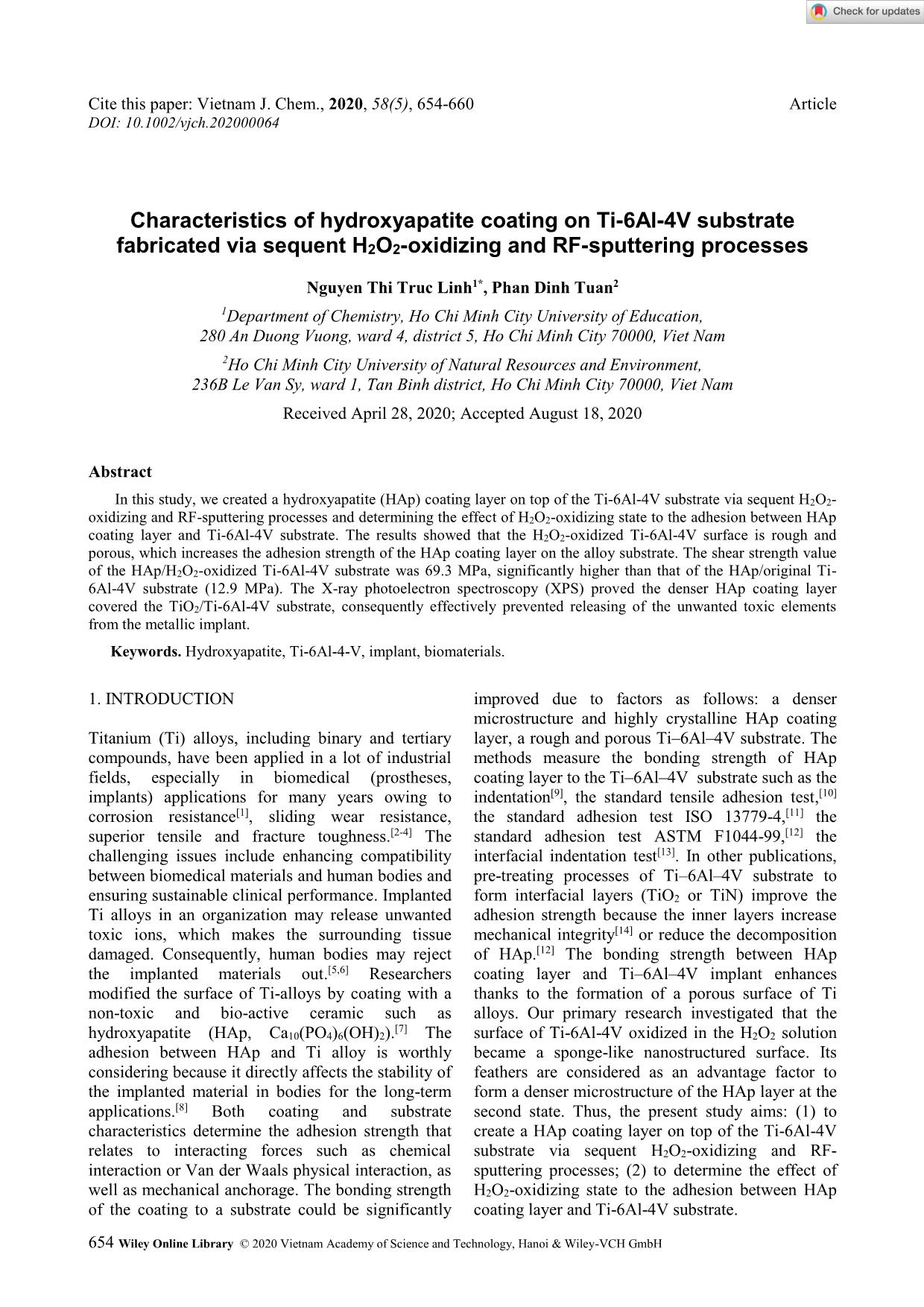
Trang 1
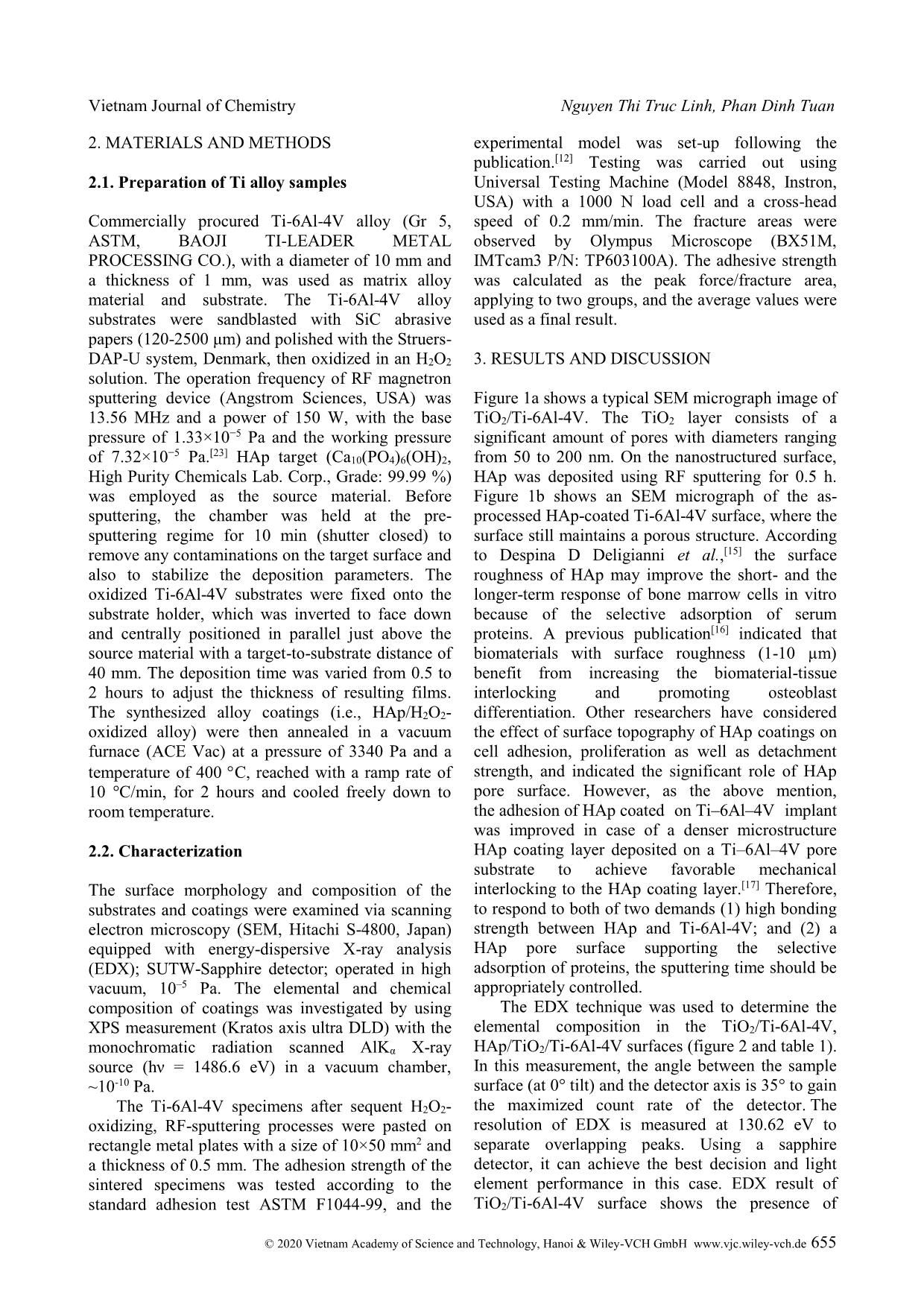
Trang 2
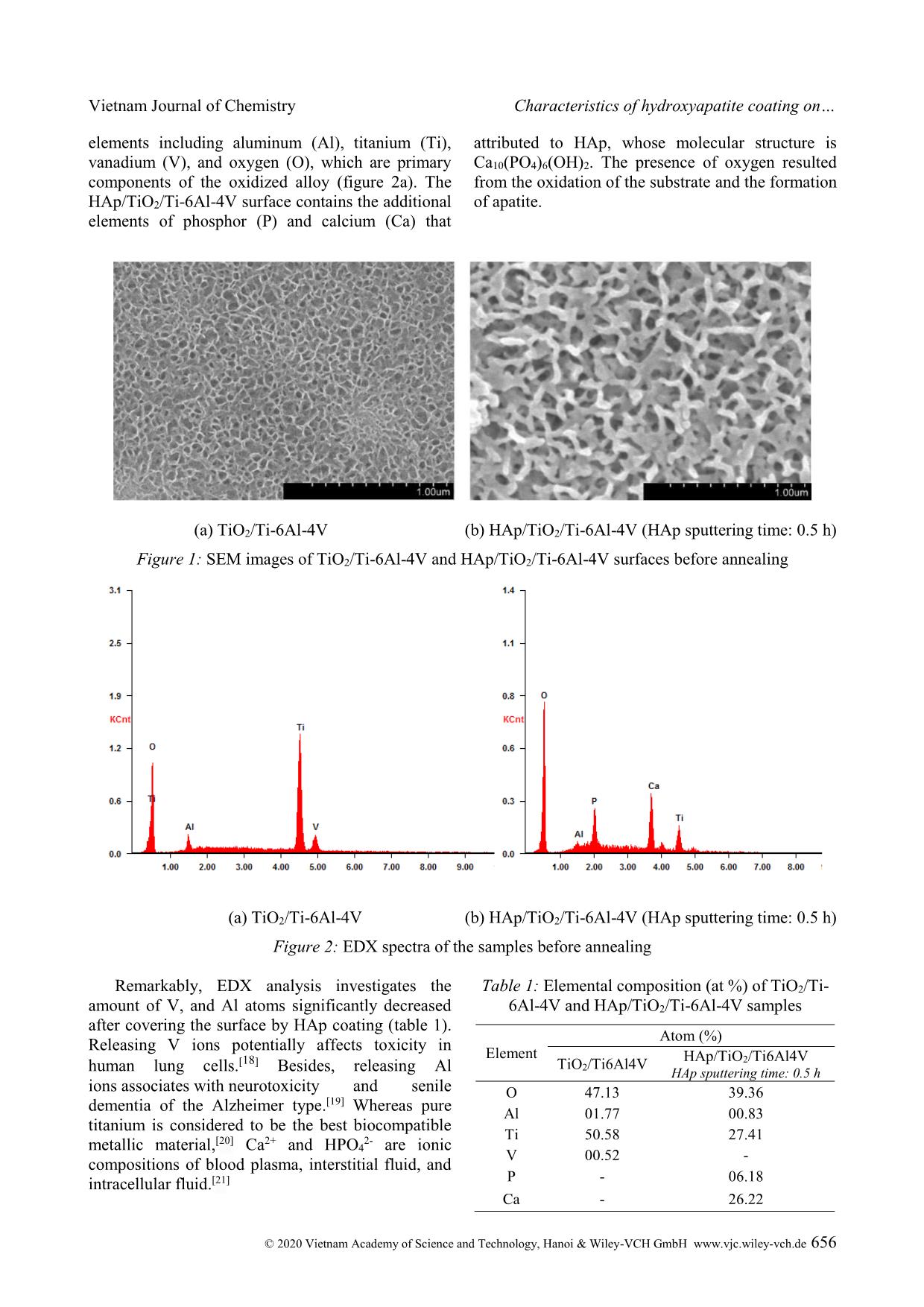
Trang 3
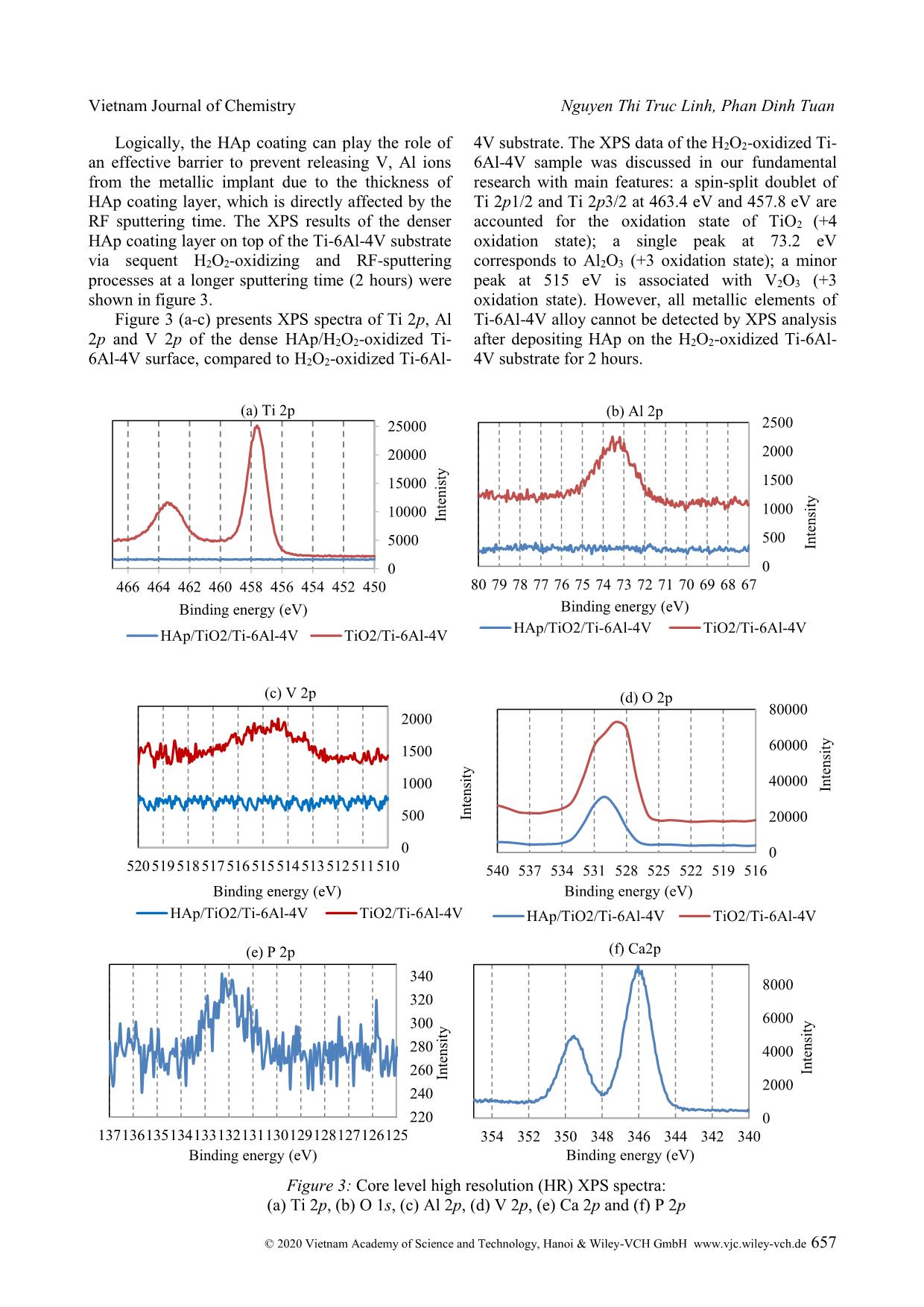
Trang 4
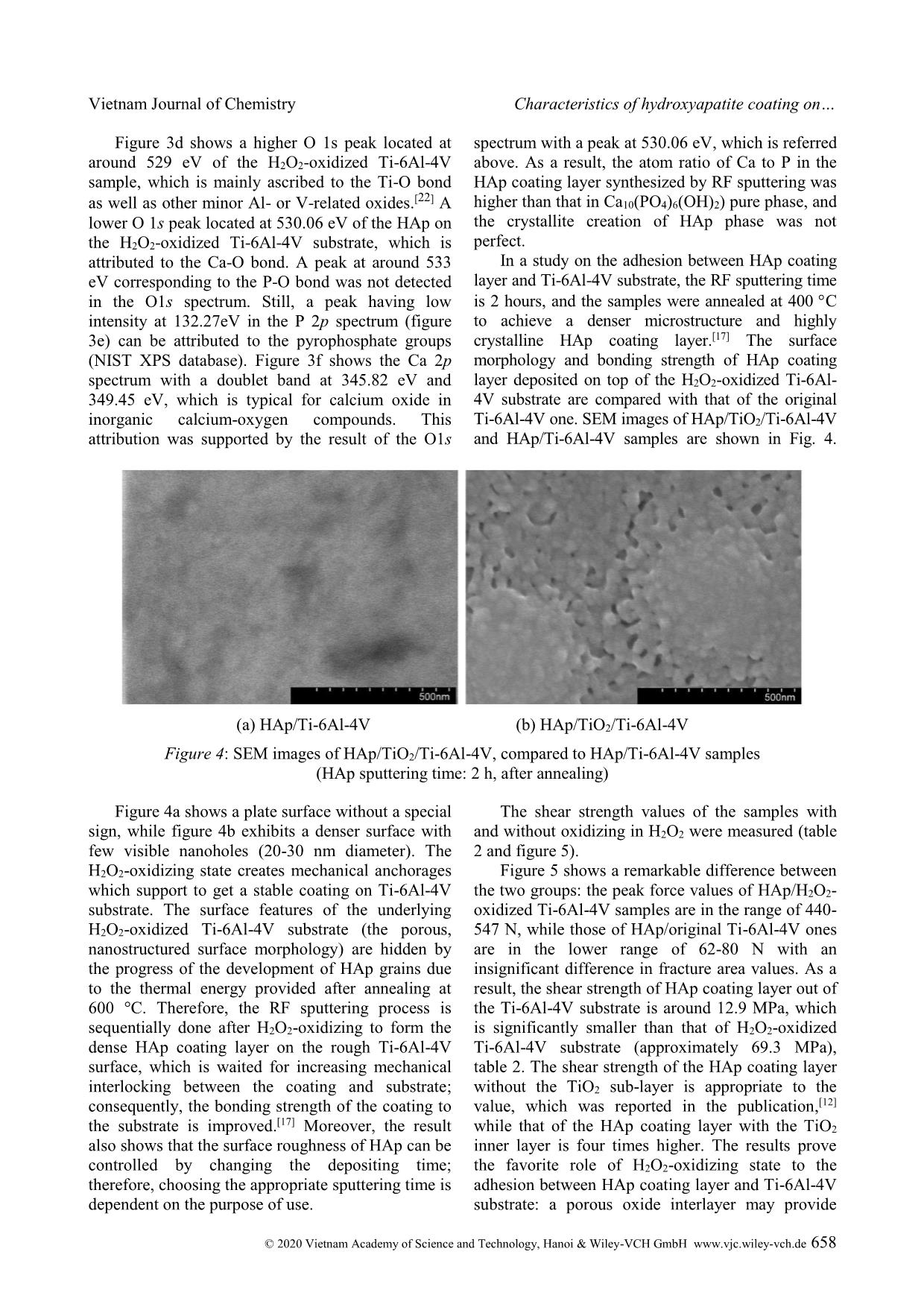
Trang 5
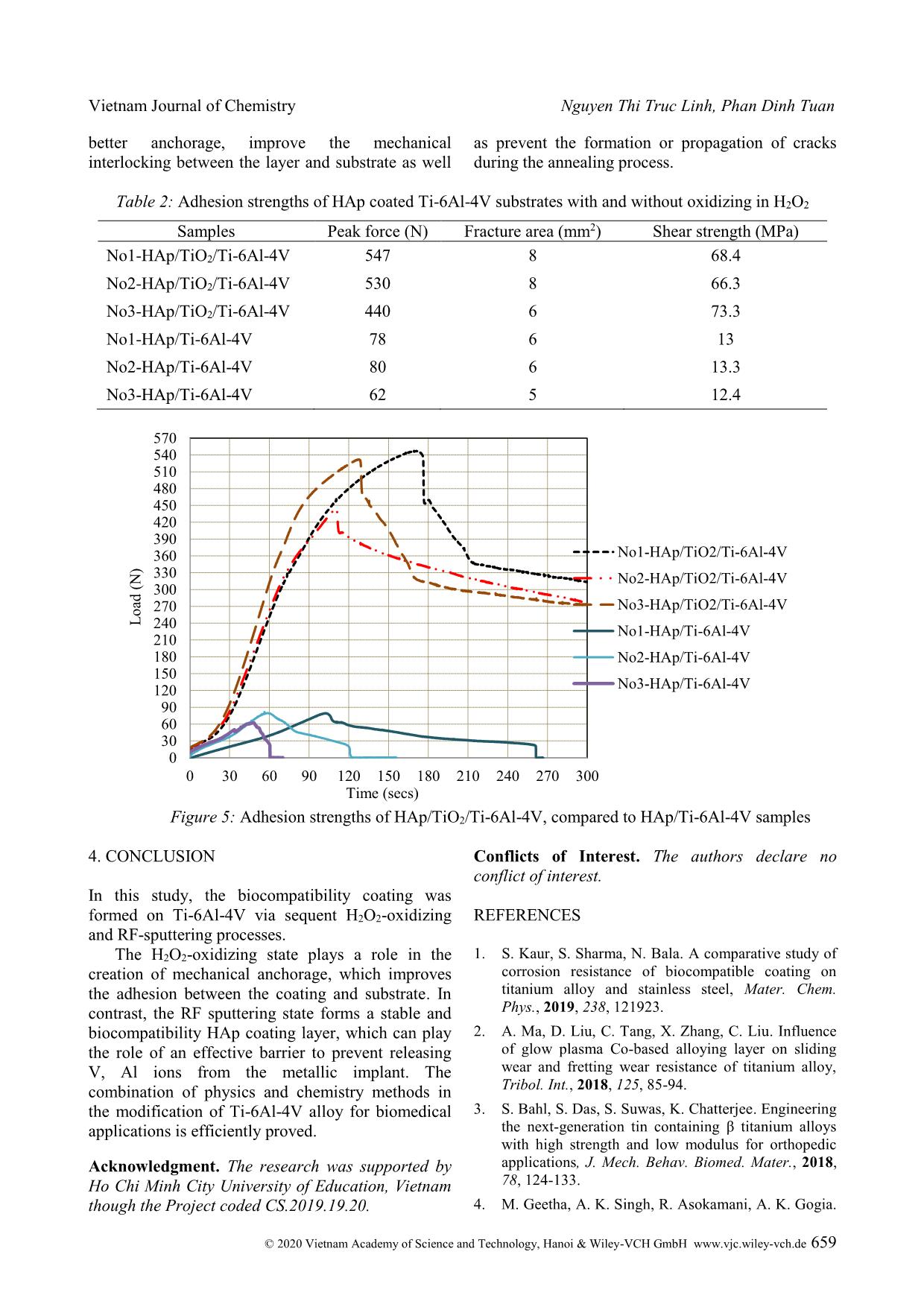
Trang 6
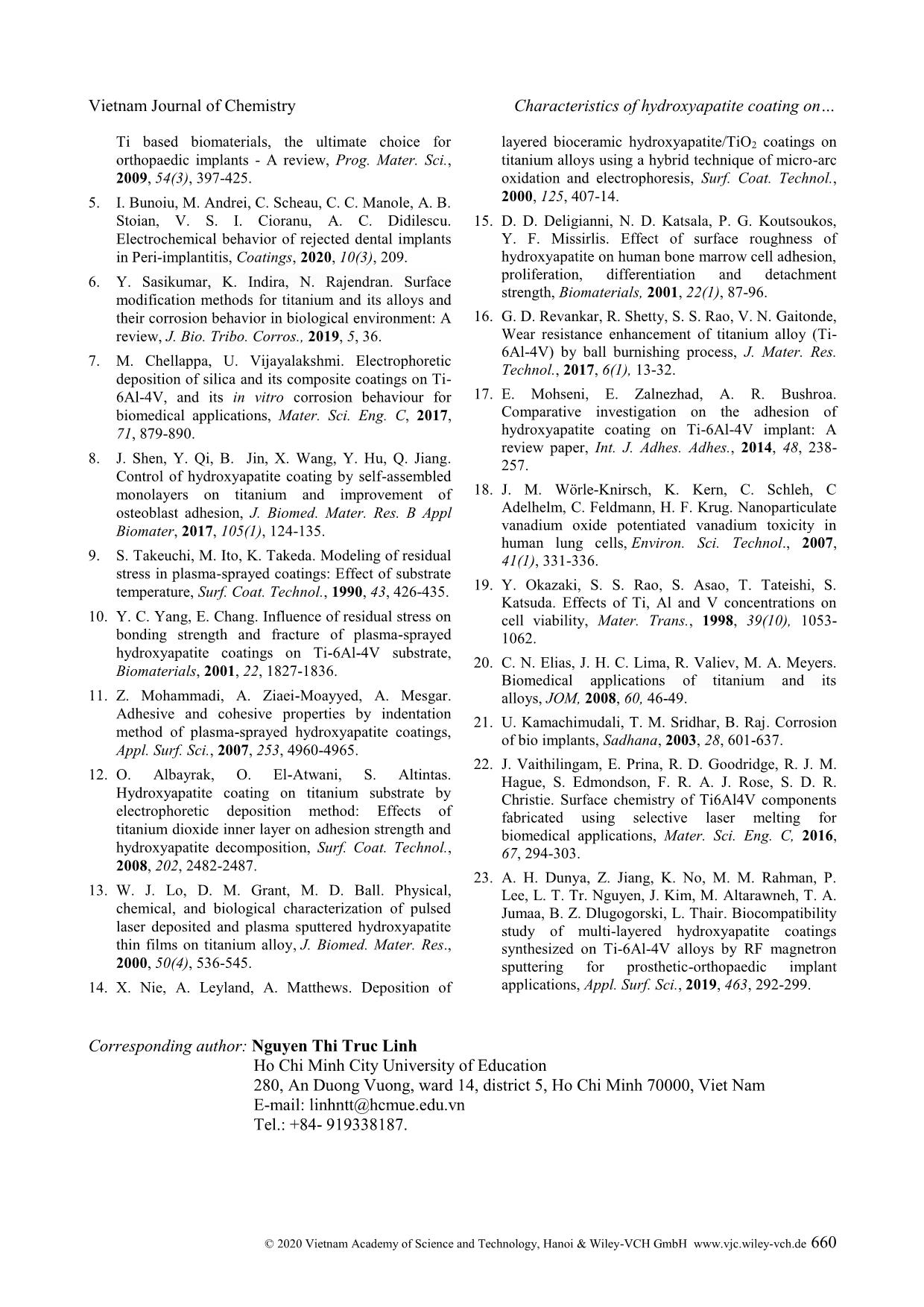
Trang 7
Tóm tắt nội dung tài liệu: Characteristics of hydroxyapatite coating on Ti-6Al-4V substrate fabricated via sequent H2O2-oxidizing and RF-sputtering processes
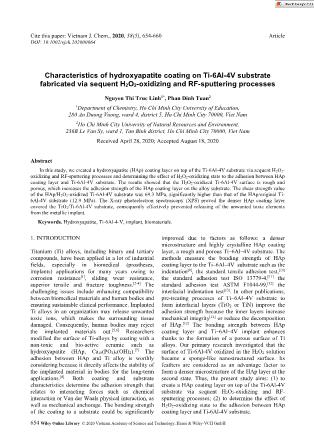
Cite this paper: Vietnam J. Chem., 2020, 58(5), 654-660 Article DOI: 10.1002/vjch.202000064 654 Wiley Online Library © 2020 Vietnam Academy of Science and Technology, Hanoi & Wiley-VCH GmbH Characteristics of hydroxyapatite coating on Ti-6Al-4V substrate fabricated via sequent H2O2-oxidizing and RF-sputtering processes Nguyen Thi Truc Linh1*, Phan Dinh Tuan2 1Department of Chemistry, Ho Chi Minh City University of Education, 280 An Duong Vuong, ward 4, district 5, Ho Chi Minh City 70000, Viet Nam 2Ho Chi Minh City University of Natural Resources and Environment, 236B Le Van Sy, ward 1, Tan Binh district, Ho Chi Minh City 70000, Viet Nam Received April 28, 2020; Accepted August 18, 2020 Abstract In this study, we created a hydroxyapatite (HAp) coating layer on top of the Ti-6Al-4V substrate via sequent H2O2- oxidizing and RF-sputtering processes and determining the effect of H2O2-oxidizing state to the adhesion between HAp coating layer and Ti-6Al-4V substrate. The results showed that the H2O2-oxidized Ti-6Al-4V surface is rough and porous, which increases the adhesion strength of the HAp coating layer on the alloy substrate. The shear strength value of the HAp/H2O2-oxidized Ti-6Al-4V substrate was 69.3 MPa, significantly higher than that of the HAp/original Ti- 6Al-4V substrate (12.9 MPa). The X-ray photoelectron spectroscopy (XPS) proved the denser HAp coating layer covered the TiO2/Ti-6Al-4V substrate, consequently effectively prevented releasing of the unwanted toxic elements from the metallic implant. Keywords. Hydroxyapatite, Ti-6Al-4-V, implant, biomaterials. 1. INTRODUCTION Titanium (Ti) alloys, including binary and tertiary compounds, have been applied in a lot of industrial fields, especially in biomedical (prostheses, implants) applications for many years owing to corrosion resistance[1], sliding wear resistance, superior tensile and fracture toughness.[2-4] The challenging issues include enhancing compatibility between biomedical materials and human bodies and ensuring sustainable clinical performance. Implanted Ti alloys in an organization may release unwanted toxic ions, which makes the surrounding tissue damaged. Consequently, human bodies may reject the implanted materials out.[5,6] Researchers modified the surface of Ti-alloys by coating with a non-toxic and bio-active ceramic such as hydroxyapatite (HAp, Ca10(PO4)6(OH)2).[7] The adhesion between HAp and Ti alloy is worthly considering because it directly affects the stability of the implanted material in bodies for the long-term applications.[8] Both coating and substrate characteristics determine the adhesion strength that relates to interacting forces such as chemical interaction or Van der Waals physical interaction, as well as mechanical anchorage. The bonding strength of the coating to a substrate could be significantly improved due to factors as follows: a denser microstructure and highly crystalline HAp coating layer, a rough and porous Ti–6Al–4V substrate. The methods measure the bonding strength of HAp coating layer to the Ti–6Al–4V substrate such as the indentation[9], the standard tensile adhesion test,[10] the standard adhesion test ISO 13779-4,[11] the standard adhesion test ASTM F1044-99,[12] the interfacial indentation test[13]. In other publications, pre-treating processes of Ti–6Al–4V substrate to form interfacial layers (TiO2 or TiN) improve the adhesion strength because the inner layers increase mechanical integrity[14] or reduce the decomposition of HAp.[12] The bonding strength between HAp coating layer and Ti–6Al–4V implant enhances thanks to the formation of a porous surface of Ti alloys. Our primary research investigated that the surface of Ti-6Al-4V oxidized in the H2O2 solution became a sponge-like nanostructured surface. Its feathers are considered as an advantage factor to form a denser microstructure of the HAp layer at the second state. Thus, the present study aims: (1) to create a HAp coating layer on top of the Ti-6Al-4V substrate via sequent H2O2-oxidizing and RF- sputtering processes; (2) to determine the effect of H2O2-oxidizing state to the adhesion between HAp coating layer and Ti-6Al-4V substrate. Vietnam Journal of Chemistry Nguyen Thi Truc Linh, Phan Dinh Tuan © 2020 Vietnam Academy of Science and Technology, Hanoi & Wiley-VCH GmbH www.vjc.wiley-vch.de 655 2. MATERIALS AND METHODS 2.1. Preparation of Ti alloy samples Commercially procured Ti-6Al-4V alloy (Gr 5, ASTM, BAOJI TI-LEADER METAL PROCESSING CO.), with a diameter of 10 mm and a thickness of 1 mm, was used as matrix alloy material and substrate. The Ti-6Al-4V alloy substrates were sandblasted with SiC abrasive papers (120-2500 μm) and polished with the Struers- DAP-U system, Denmark, then oxidized in an H2O2 solution. The operation frequency of RF magnetron sputtering device (Angstrom Sciences, USA) was 13.56 MHz and a power of 150 W, with the base pressure of 1.33×10−5 Pa and the working pressure of 7.32×10−5 Pa.[23] HAp target (Ca10(PO4)6(OH)2, High Purity Chemicals Lab. Corp., Grade: 99.99 %) was employed as the source material. Before sputtering, the chamber was held at the pre- sputtering regime for 10 min (shutter closed) to remove any contaminations on the target surface and also to stabilize the deposition parameters. The oxidized Ti-6Al-4V substrates were fixed onto the substrate holder, which was inverted to face down and centrally positioned in parallel just above the source material with a target-to-substrate distance of 40 mm. The deposition time was varied from 0.5 to 2 hours to adjust the thickness of resulting films. The synthesized alloy coatings (i.e., HAp/H2O2- oxidized alloy) were then annealed in a vacuum furnace (ACE Vac) at a pressure of 3340 Pa and a temperature of 400 C, reached with a ramp rate o ... ionic compositions of blood plasma, interstitial fluid, and intracellular fluid.[21] Table 1: Elemental composition (at %) of TiO2/Ti- 6Al-4V and HAp/TiO2/Ti-6Al-4V samples Element Atom (%) TiO2/Ti6Al4V HAp/TiO2/Ti6Al4V HAp sputtering time: 0.5 h O 47.13 39.36 Al 01.77 00.83 Ti 50.58 27.41 V 00.52 - P - 06.18 Ca - 26.22 Vietnam Journal of Chemistry Nguyen Thi Truc Linh, Phan Dinh Tuan © 2020 Vietnam Academy of Science and Technology, Hanoi & Wiley-VCH GmbH www.vjc.wiley-vch.de 657 Logically, the HAp coating can play the role of an effective barrier to prevent releasing V, Al ions from the metallic implant due to the thickness of HAp coating layer, which is directly affected by the RF sputtering time. The XPS results of the denser HAp coating layer on top of the Ti-6Al-4V substrate via sequent H2O2-oxidizing and RF-sputtering processes at a longer sputtering time (2 hours) were shown in figure 3. Figure 3 (a-c) presents XPS spectra of Ti 2p, Al 2p and V 2p of the dense HAp/H2O2-oxidized Ti- 6Al-4V surface, compared to H2O2-oxidized Ti-6Al- 4V substrate. The XPS data of the H2O2-oxidized Ti- 6Al-4V sample was discussed in our fundamental research with main features: a spin-split doublet of Ti 2p1/2 and Ti 2p3/2 at 463.4 eV and 457.8 eV are accounted for the oxidation state of TiO2 (+4 oxidation state); a single peak at 73.2 eV corresponds to Al2O3 (+3 oxidation state); a minor peak at 515 eV is associated with V2O3 (+3 oxidation state). However, all metallic elements of Ti-6Al-4V alloy cannot be detected by XPS analysis after depositing HAp on the H2O2-oxidized Ti-6Al- 4V substrate for 2 hours. Figure 3: Core level high resolution (HR) XPS spectra: (a) Ti 2p, (b) O 1s, (c) Al 2p, (d) V 2p, (e) Ca 2p and (f) P 2p 0 5000 10000 15000 20000 25000 450452454456458460462464466 In te n is ty Binding energy (eV) (a) Ti 2p HAp/TiO2/Ti-6Al-4V TiO2/Ti-6Al-4V 0 500 1000 1500 2000 2500 6768697071727374757677787980 In te n si ty Binding energy (eV) (b) Al 2p HAp/TiO2/Ti-6Al-4V TiO2/Ti-6Al-4V 0 500 1000 1500 2000 510511512513514515516517518519520 In te n si ty Binding energy (eV) (c) V 2p HAp/TiO2/Ti-6Al-4V TiO2/Ti-6Al-4V 0 20000 40000 60000 80000 516519522525528531534537540 In te n si ty Binding energy (eV) (d) O 2p HAp/TiO2/Ti-6Al-4V TiO2/Ti-6Al-4V 220 240 260 280 300 320 340 125126127128129130131132133134135136137 In te n si ty Binding energy (eV) (e) P 2p 0 2000 4000 6000 8000 340342344346348350352354 In te n si ty Binding energy (eV) (f) Ca2p Vietnam Journal of Chemistry Characteristics of hydroxyapatite coating on © 2020 Vietnam Academy of Science and Technology, Hanoi & Wiley-VCH GmbH www.vjc.wiley-vch.de 658 Figure 3d shows a higher O 1s peak located at around 529 eV of the H2O2-oxidized Ti-6Al-4V sample, which is mainly ascribed to the Ti-O bond as well as other minor Al- or V-related oxides.[22] A lower O 1s peak located at 530.06 eV of the HAp on the H2O2-oxidized Ti-6Al-4V substrate, which is attributed to the Ca-O bond. A peak at around 533 eV corresponding to the P-O bond was not detected in the O1s spectrum. Still, a peak having low intensity at 132.27eV in the P 2p spectrum (figure 3e) can be attributed to the pyrophosphate groups (NIST XPS database). Figure 3f shows the Ca 2p spectrum with a doublet band at 345.82 eV and 349.45 eV, which is typical for calcium oxide in inorganic calcium-oxygen compounds. This attribution was supported by the result of the O1s spectrum with a peak at 530.06 eV, which is referred above. As a result, the atom ratio of Ca to P in the HAp coating layer synthesized by RF sputtering was higher than that in Ca10(PO4)6(OH)2) pure phase, and the crystallite creation of HAp phase was not perfect. In a study on the adhesion between HAp coating layer and Ti-6Al-4V substrate, the RF sputtering time is 2 hours, and the samples were annealed at 400 C to achieve a denser microstructure and highly crystalline HAp coating layer.[17] The surface morphology and bonding strength of HAp coating layer deposited on top of the H2O2-oxidized Ti-6Al- 4V substrate are compared with that of the original Ti-6Al-4V one. SEM images of HAp/TiO2/Ti-6Al-4V and HAp/Ti-6Al-4V samples are shown in Fig. 4. (a) HAp/Ti-6Al-4V (b) HAp/TiO2/Ti-6Al-4V Figure 4: SEM images of HAp/TiO2/Ti-6Al-4V, compared to HAp/Ti-6Al-4V samples (HAp sputtering time: 2 h, after annealing) Figure 4a shows a plate surface without a special sign, while figure 4b exhibits a denser surface with few visible nanoholes (20-30 nm diameter). The H2O2-oxidizing state creates mechanical anchorages which support to get a stable coating on Ti-6Al-4V substrate. The surface features of the underlying H2O2-oxidized Ti-6Al-4V substrate (the porous, nanostructured surface morphology) are hidden by the progress of the development of HAp grains due to the thermal energy provided after annealing at 600 °C. Therefore, the RF sputtering process is sequentially done after H2O2-oxidizing to form the dense HAp coating layer on the rough Ti-6Al-4V surface, which is waited for increasing mechanical interlocking between the coating and substrate; consequently, the bonding strength of the coating to the substrate is improved.[17] Moreover, the result also shows that the surface roughness of HAp can be controlled by changing the depositing time; therefore, choosing the appropriate sputtering time is dependent on the purpose of use. The shear strength values of the samples with and without oxidizing in H2O2 were measured (table 2 and figure 5). Figure 5 shows a remarkable difference between the two groups: the peak force values of HAp/H2O2- oxidized Ti-6Al-4V samples are in the range of 440- 547 N, while those of HAp/original Ti-6Al-4V ones are in the lower range of 62-80 N with an insignificant difference in fracture area values. As a result, the shear strength of HAp coating layer out of the Ti-6Al-4V substrate is around 12.9 MPa, which is significantly smaller than that of H2O2-oxidized Ti-6Al-4V substrate (approximately 69.3 MPa), table 2. The shear strength of the HAp coating layer without the TiO2 sub-layer is appropriate to the value, which was reported in the publication,[12] while that of the HAp coating layer with the TiO2 inner layer is four times higher. The results prove the favorite role of H2O2-oxidizing state to the adhesion between HAp coating layer and Ti-6Al-4V substrate: a porous oxide interlayer may provide Vietnam Journal of Chemistry Nguyen Thi Truc Linh, Phan Dinh Tuan © 2020 Vietnam Academy of Science and Technology, Hanoi & Wiley-VCH GmbH www.vjc.wiley-vch.de 659 better anchorage, improve the mechanical interlocking between the layer and substrate as well as prevent the formation or propagation of cracks during the annealing process. Table 2: Adhesion strengths of HAp coated Ti-6Al-4V substrates with and without oxidizing in H2O2 Samples Peak force (N) Fracture area (mm2) Shear strength (MPa) No1-HAp/TiO2/Ti-6Al-4V 547 8 68.4 No2-HAp/TiO2/Ti-6Al-4V 530 8 66.3 No3-HAp/TiO2/Ti-6Al-4V 440 6 73.3 No1-HAp/Ti-6Al-4V 78 6 13 No2-HAp/Ti-6Al-4V 80 6 13.3 No3-HAp/Ti-6Al-4V 62 5 12.4 Figure 5: Adhesion strengths of HAp/TiO2/Ti-6Al-4V, compared to HAp/Ti-6Al-4V samples 4. CONCLUSION In this study, the biocompatibility coating was formed on Ti-6Al-4V via sequent H2O2-oxidizing and RF-sputtering processes. The H2O2-oxidizing state plays a role in the creation of mechanical anchorage, which improves the adhesion between the coating and substrate. In contrast, the RF sputtering state forms a stable and biocompatibility HAp coating layer, which can play the role of an effective barrier to prevent releasing V, Al ions from the metallic implant. The combination of physics and chemistry methods in the modification of Ti-6Al-4V alloy for biomedical applications is efficiently proved. Acknowledgment. The research was supported by Ho Chi Minh City University of Education, Vietnam though the Project coded CS.2019.19.20. Conflicts of Interest. The authors declare no conflict of interest. REFERENCES 1. S. Kaur, S. Sharma, N. Bala. A comparative study of corrosion resistance of biocompatible coating on titanium alloy and stainless steel, Mater. Chem. Phys., 2019, 238, 121923. 2. A. Ma, D. Liu, C. Tang, X. Zhang, C. Liu. Influence of glow plasma Co-based alloying layer on sliding wear and fretting wear resistance of titanium alloy, Tribol. Int., 2018, 125, 85-94. 3. S. Bahl, S. Das, S. Suwas, K. Chatterjee. Engineering the next-generation tin containing β titanium alloys with high strength and low modulus for orthopedic applications, J. Mech. Behav. Biomed. Mater., 2018, 78, 124-133. 4. M. Geetha, A. K. Singh, R. Asokamani, A. K. Gogia. 0 30 60 90 120 150 180 210 240 270 300 330 360 390 420 450 480 510 540 570 0 30 60 90 120 150 180 210 240 270 300 L o ad ( N ) Time (secs) No1-HAp/TiO2/Ti-6Al-4V No2-HAp/TiO2/Ti-6Al-4V No3-HAp/TiO2/Ti-6Al-4V No1-HAp/Ti-6Al-4V No2-HAp/Ti-6Al-4V No3-HAp/Ti-6Al-4V Vietnam Journal of Chemistry Characteristics of hydroxyapatite coating on © 2020 Vietnam Academy of Science and Technology, Hanoi & Wiley-VCH GmbH www.vjc.wiley-vch.de 660 Ti based biomaterials, the ultimate choice for orthopaedic implants - A review, Prog. Mater. Sci., 2009, 54(3), 397-425. 5. I. Bunoiu, M. Andrei, C. Scheau, C. C. Manole, A. B. Stoian, V. S. I. Cioranu, A. C. Didilescu. Electrochemical behavior of rejected dental implants in Peri-implantitis, Coatings, 2020, 10(3), 209. 6. Y. Sasikumar, K. Indira, N. Rajendran. Surface modification methods for titanium and its alloys and their corrosion behavior in biological environment: A review, J. Bio. Tribo. Corros., 2019, 5, 36. 7. M. Chellappa, U. Vijayalakshmi. Electrophoretic deposition of silica and its composite coatings on Ti- 6Al-4V, and its in vitro corrosion behaviour for biomedical applications, Mater. Sci. Eng. C, 2017, 71, 879-890. 8. J. Shen, Y. Qi, B. Jin, X. Wang, Y. Hu, Q. Jiang. Control of hydroxyapatite coating by self-assembled monolayers on titanium and improvement of osteoblast adhesion, J. Biomed. Mater. Res. B Appl Biomater, 2017, 105(1), 124-135. 9. S. Takeuchi, M. Ito, K. Takeda. Modeling of residual stress in plasma-sprayed coatings: Effect of substrate temperature, Surf. Coat. Technol., 1990, 43, 426-435. 10. Y. C. Yang, E. Chang. Influence of residual stress on bonding strength and fracture of plasma-sprayed hydroxyapatite coatings on Ti-6Al-4V substrate, Biomaterials, 2001, 22, 1827-1836. 11. Z. Mohammadi, A. Ziaei-Moayyed, A. Mesgar. Adhesive and cohesive properties by indentation method of plasma-sprayed hydroxyapatite coatings, Appl. Surf. Sci., 2007, 253, 4960-4965. 12. O. Albayrak, O. El-Atwani, S. Altintas. Hydroxyapatite coating on titanium substrate by electrophoretic deposition method: Effects of titanium dioxide inner layer on adhesion strength and hydroxyapatite decomposition, Surf. Coat. Technol., 2008, 202, 2482-2487. 13. W. J. Lo, D. M. Grant, M. D. Ball. Physical, chemical, and biological characterization of pulsed laser deposited and plasma sputtered hydroxyapatite thin films on titanium alloy, J. Biomed. Mater. Res., 2000, 50(4), 536-545. 14. X. Nie, A. Leyland, A. Matthews. Deposition of layered bioceramic hydroxyapatite/TiO2 coatings on titanium alloys using a hybrid technique of micro-arc oxidation and electrophoresis, Surf. Coat. Technol., 2000, 125, 407-14. 15. D. D. Deligianni, N. D. Katsala, P. G. Koutsoukos, Y. F. Missirlis. Effect of surface roughness of hydroxyapatite on human bone marrow cell adhesion, proliferation, differentiation and detachment strength, Biomaterials, 2001, 22(1), 87-96. 16. G. D. Revankar, R. Shetty, S. S. Rao, V. N. Gaitonde, Wear resistance enhancement of titanium alloy (Ti- 6Al-4V) by ball burnishing process, J. Mater. Res. Technol., 2017, 6(1), 13-32. 17. E. Mohseni, E. Zalnezhad, A. R. Bushroa. Comparative investigation on the adhesion of hydroxyapatite coating on Ti-6Al-4V implant: A review paper, Int. J. Adhes. Adhes., 2014, 48, 238- 257. 18. J. M. Wörle-Knirsch, K. Kern, C. Schleh, C Adelhelm, C. Feldmann, H. F. Krug. Nanoparticulate vanadium oxide potentiated vanadium toxicity in human lung cells, Environ. Sci. Technol., 2007, 41(1), 331-336. 19. Y. Okazaki, S. S. Rao, S. Asao, T. Tateishi, S. Katsuda. Effects of Ti, Al and V concentrations on cell viability, Mater. Trans., 1998, 39(10), 1053- 1062. 20. C. N. Elias, J. H. C. Lima, R. Valiev, M. A. Meyers. Biomedical applications of titanium and its alloys, JOM, 2008, 60, 46-49. 21. U. Kamachimudali, T. M. Sridhar, B. Raj. Corrosion of bio implants, Sadhana, 2003, 28, 601-637. 22. J. Vaithilingam, E. Prina, R. D. Goodridge, R. J. M. Hague, S. Edmondson, F. R. A. J. Rose, S. D. R. Christie. Surface chemistry of Ti6Al4V components fabricated using selective laser melting for biomedical applications, Mater. Sci. Eng. C, 2016, 67, 294-303. 23. A. H. Dunya, Z. Jiang, K. No, M. M. Rahman, P. Lee, L. T. Tr. Nguyen, J. Kim, M. Altarawneh, T. A. Jumaa, B. Z. Dlugogorski, L. Thair. Biocompatibility study of multi-layered hydroxyapatite coatings synthesized on Ti-6Al-4V alloys by RF magnetron sputtering for prosthetic-orthopaedic implant applications, Appl. Surf. Sci., 2019, 463, 292-299. Corresponding author: Nguyen Thi Truc Linh Ho Chi Minh City University of Education 280, An Duong Vuong, ward 14, district 5, Ho Chi Minh 70000, Viet Nam E-mail: linhntt@hcmue.edu.vn Tel.: +84- 919338187.
File đính kèm:
characteristics_of_hydroxyapatite_coating_on_ti_6al_4v_subst.pdf