Research on film coating formulation of sustained release pellets of verapamil hydrochloride
Objectives: To determine the optimized parameters of the technical process and the
adequate excipient ingredients of the pellet film coat which control release to develop the
basic formula of the sustained release (SR) pellet of Verapamil hydrochloride (VER.HCl).
Materials and method: Prepare SR VER.HCl pellet with film coating using Mini-Glatt
fluidized bed; quantify VER.HCl with UV spectroscopy method; examine the effect of excipients
(EC, HPMC, DBP, TEC and Talc) on the dissolution of SR VER.HCl pellet. Results: With
excipients EC N20, HPMC E15, HPMC E5, TEC and Talc, the release rate of VER.HCl was
9.02%, 26.55%, 48.90% and 83.73% at the time of 1, 2, 4 and 8 hours, respectively.
Conclusion: EC N10, HPMC E15 and HPMC E5 controlled release excipients suitable for
formula of SR VER.HCl pellet film 120 mg.
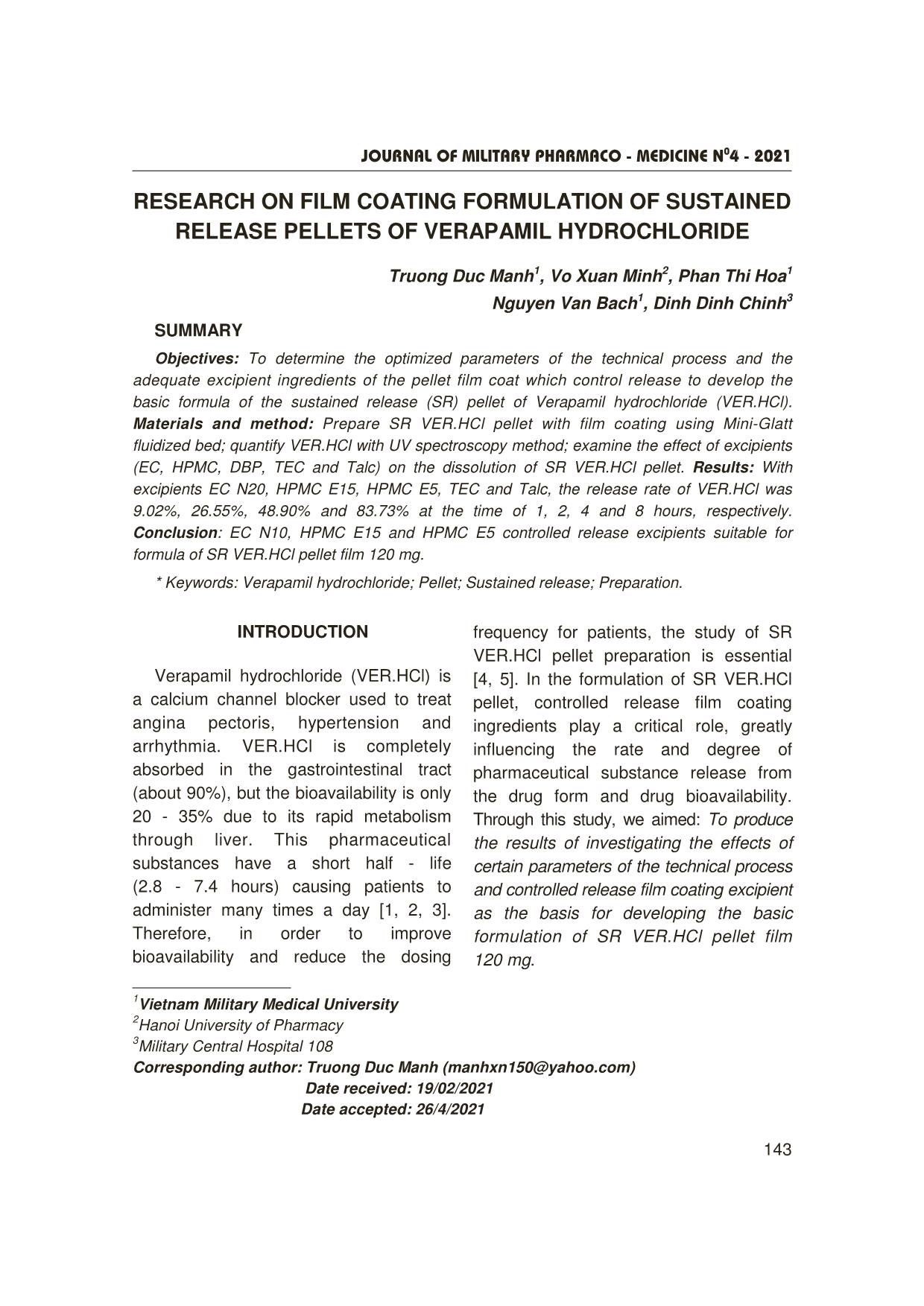
Trang 1
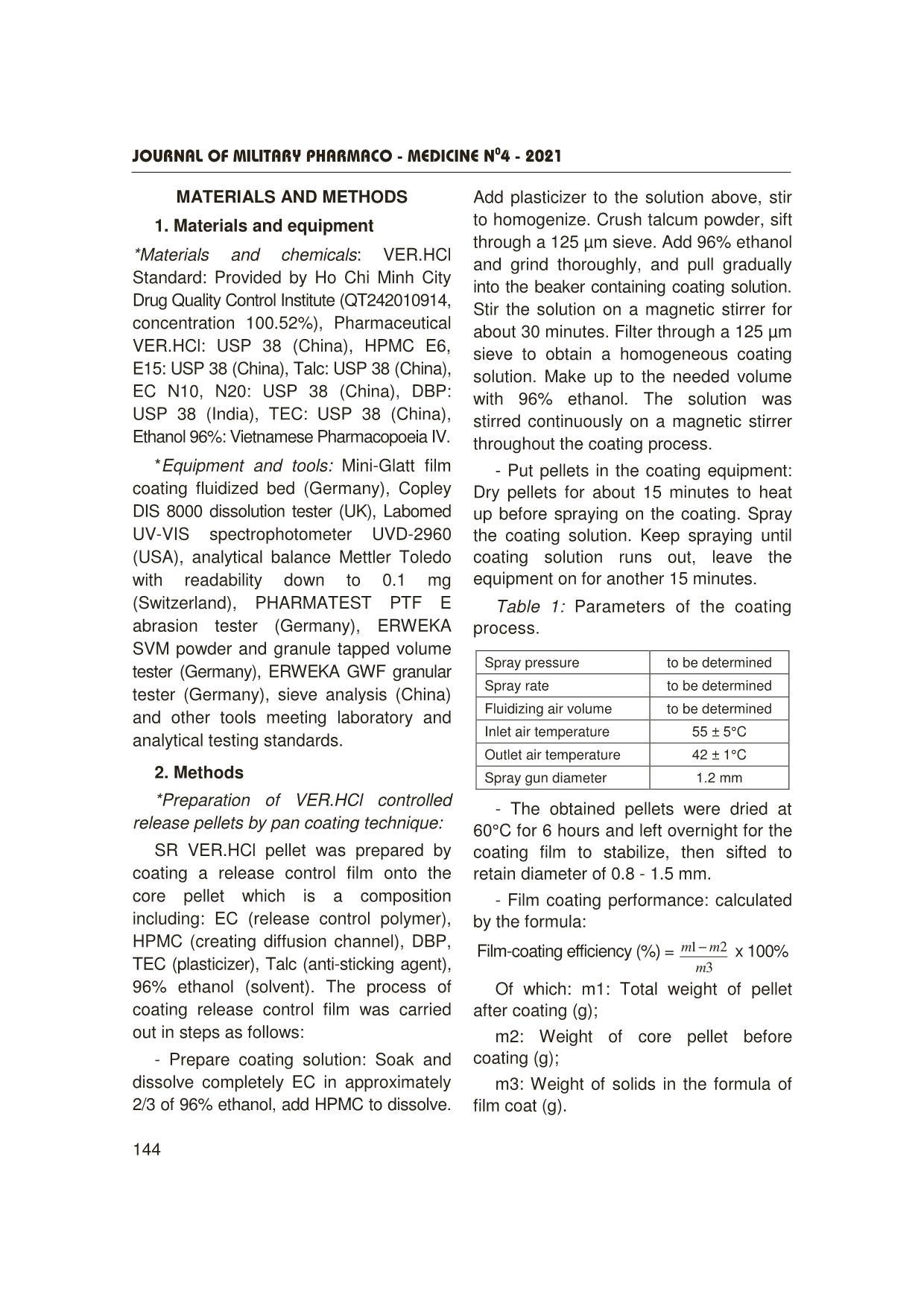
Trang 2

Trang 3
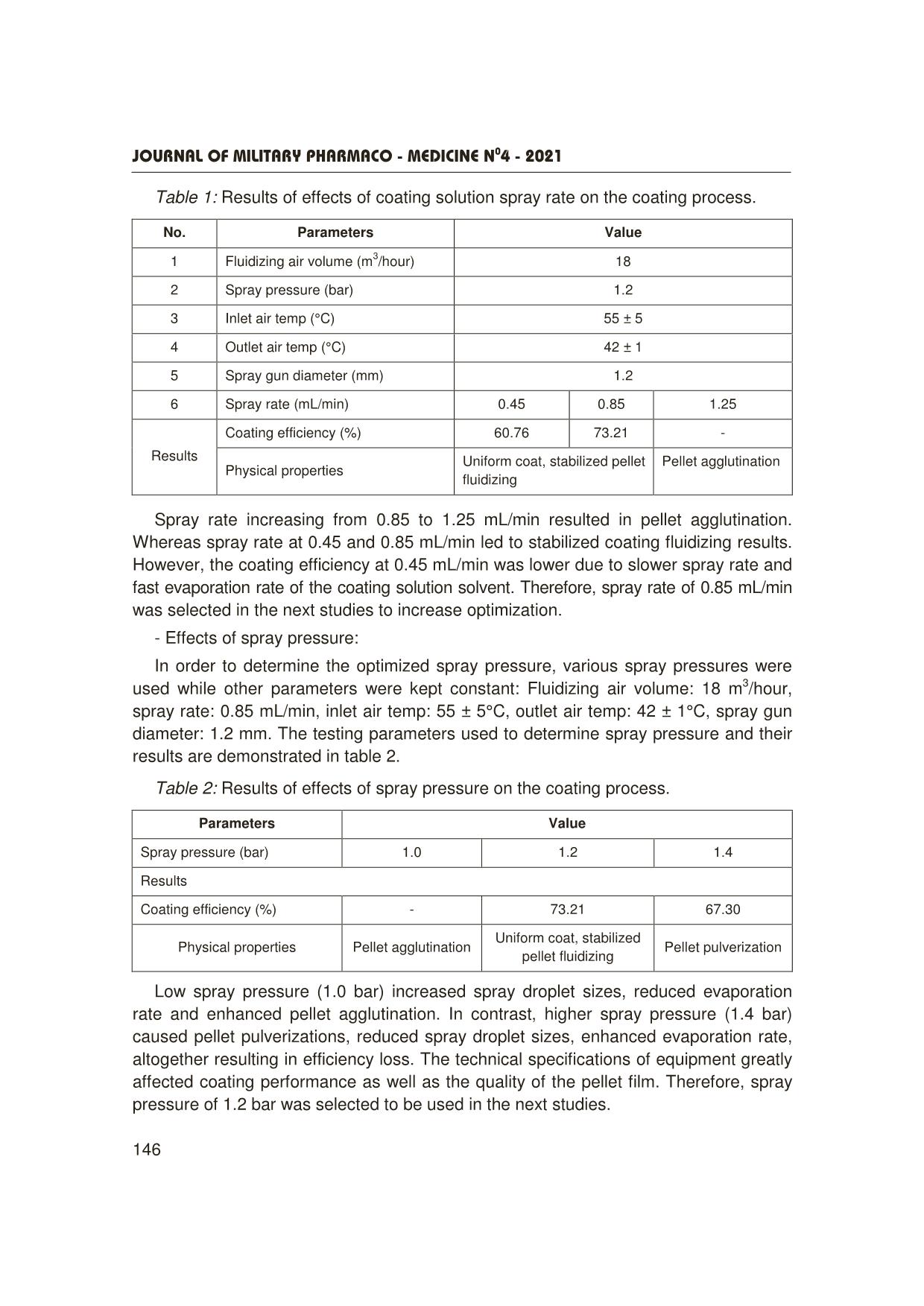
Trang 4
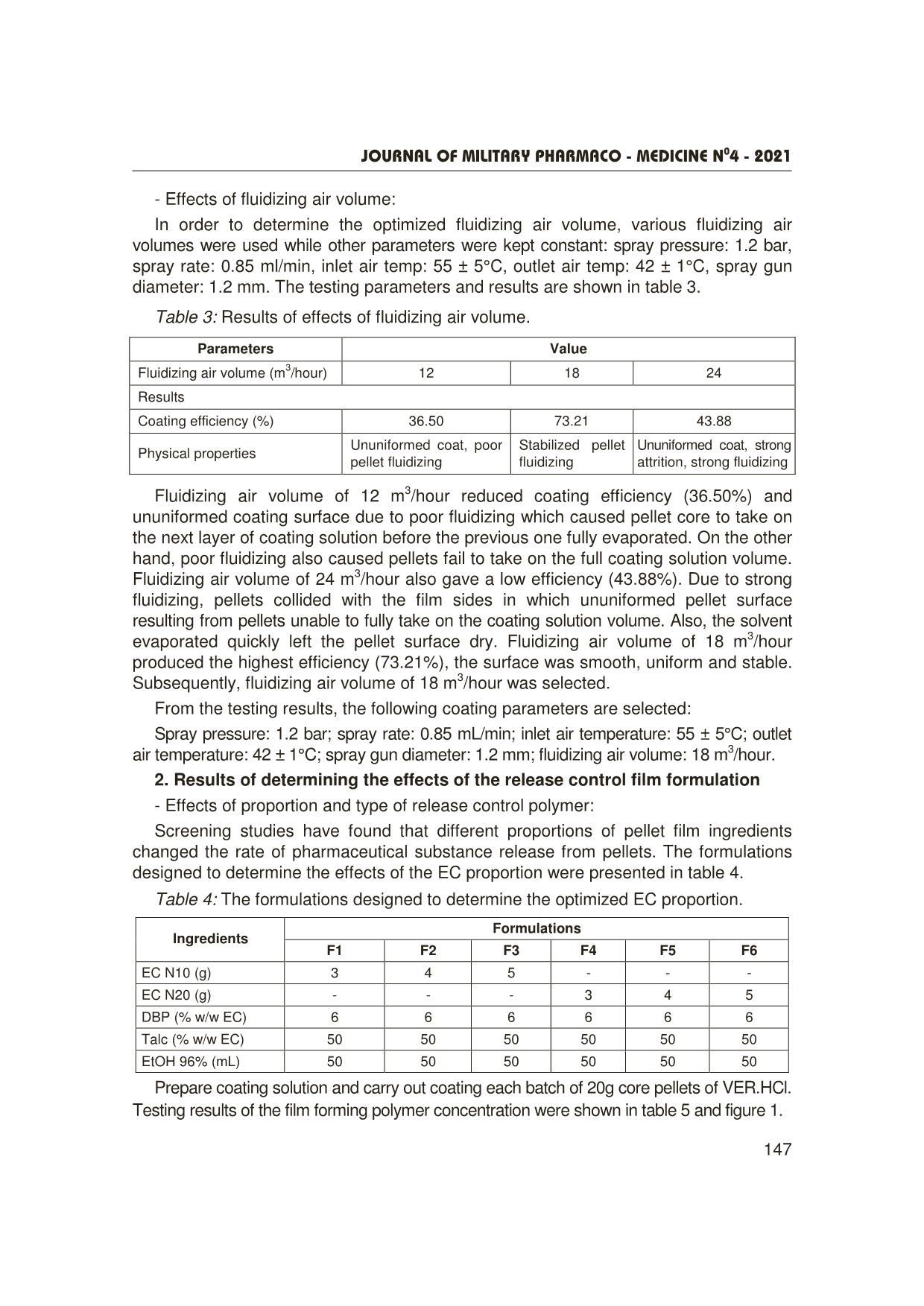
Trang 5
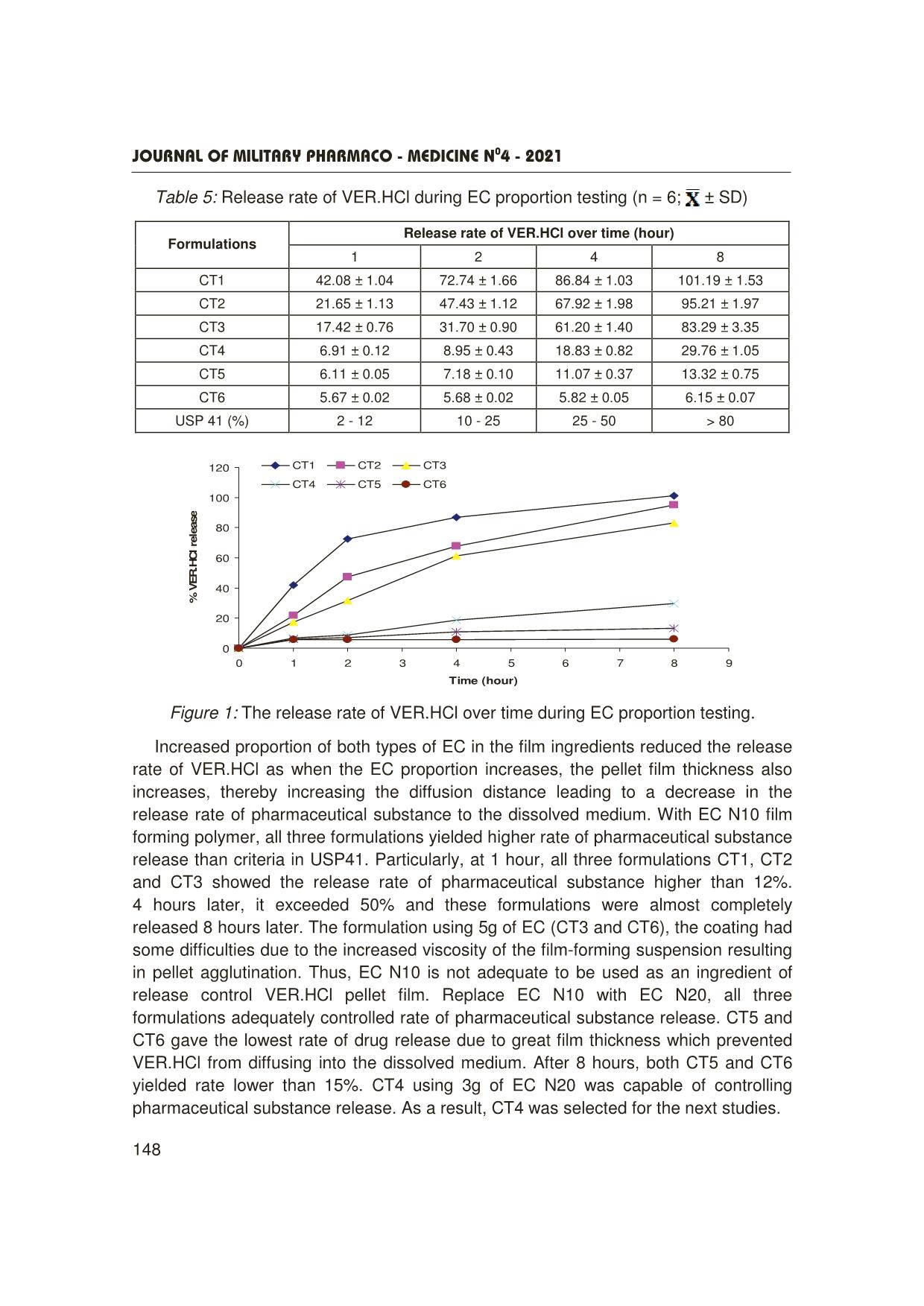
Trang 6
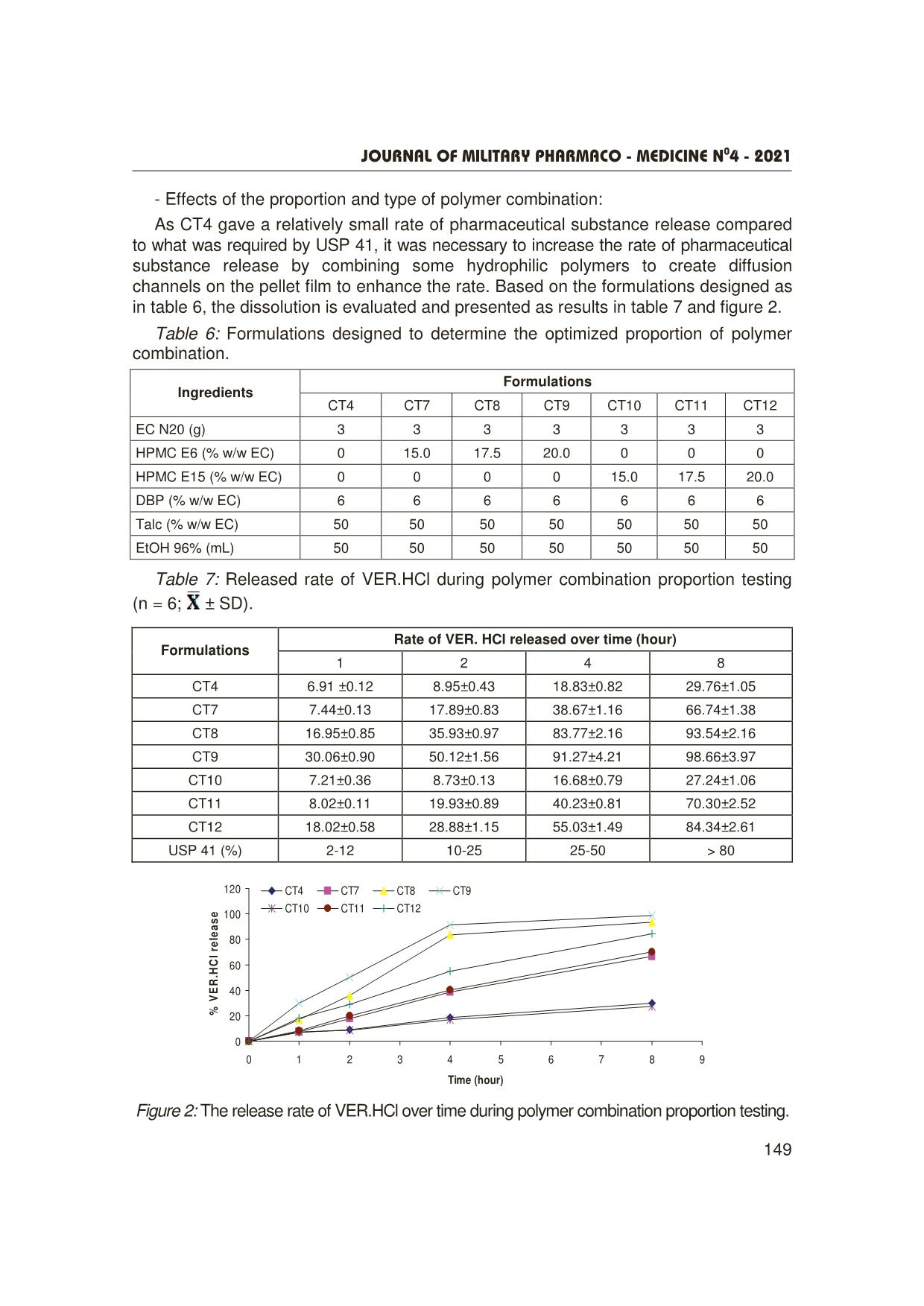
Trang 7
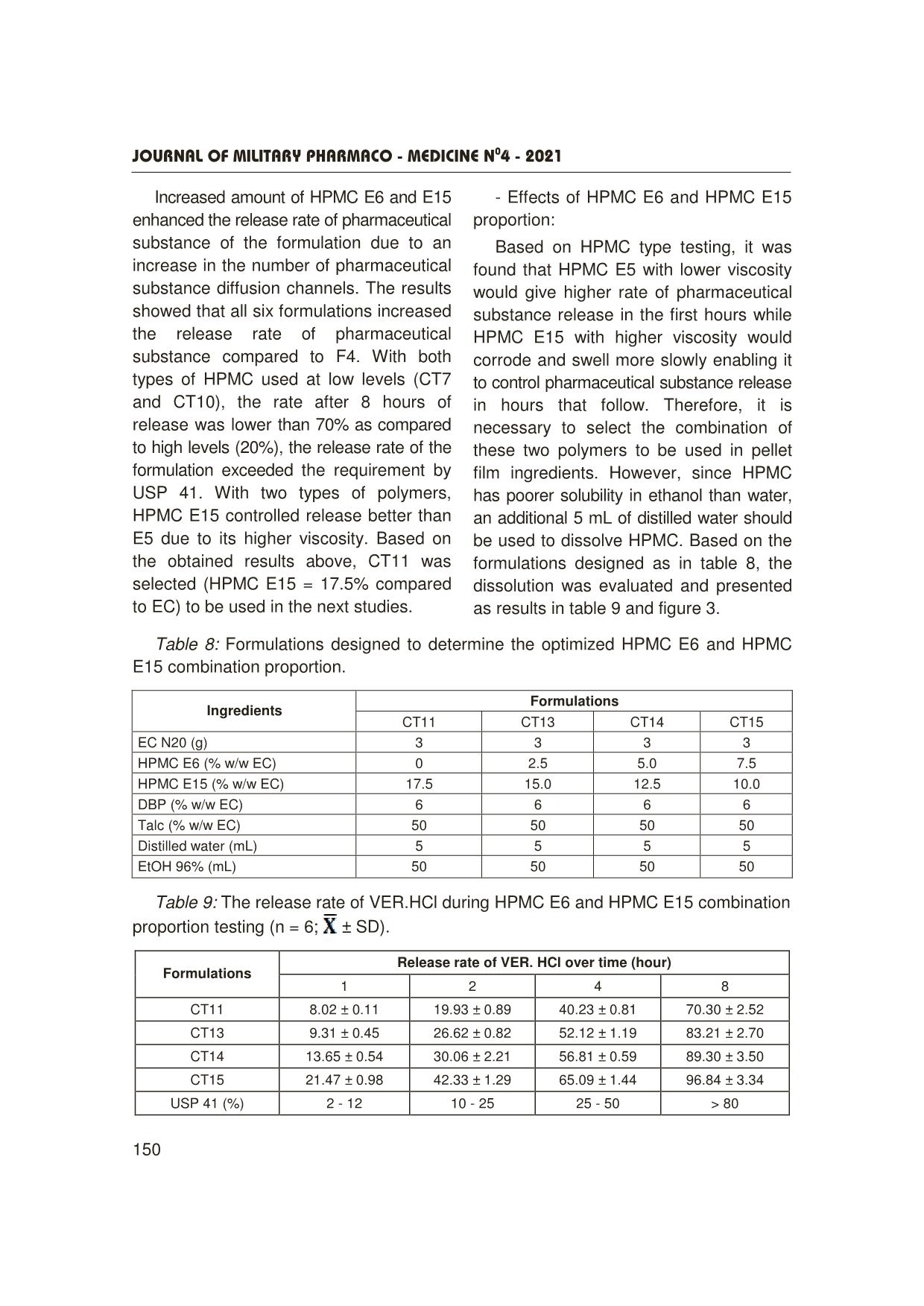
Trang 8
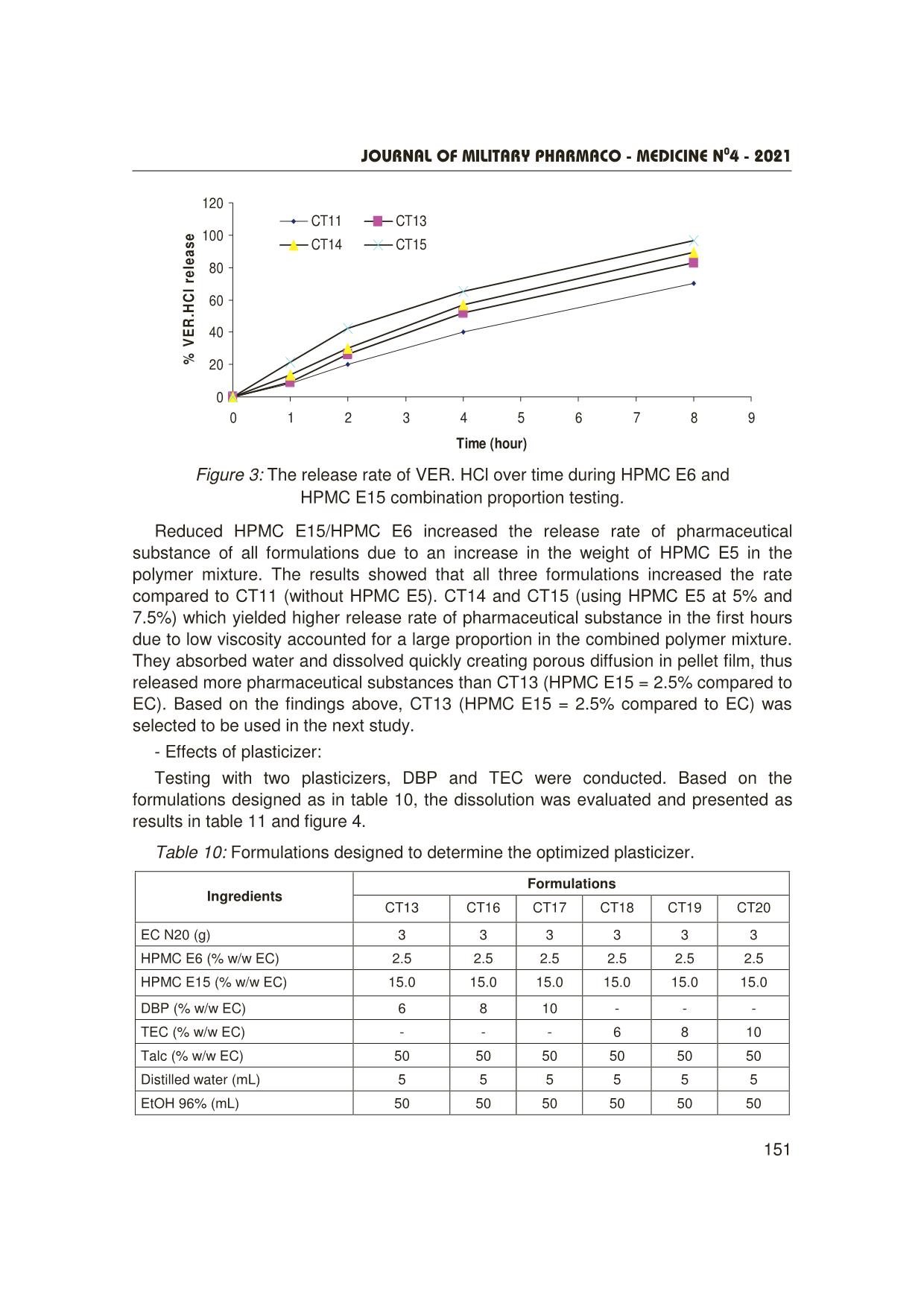
Trang 9
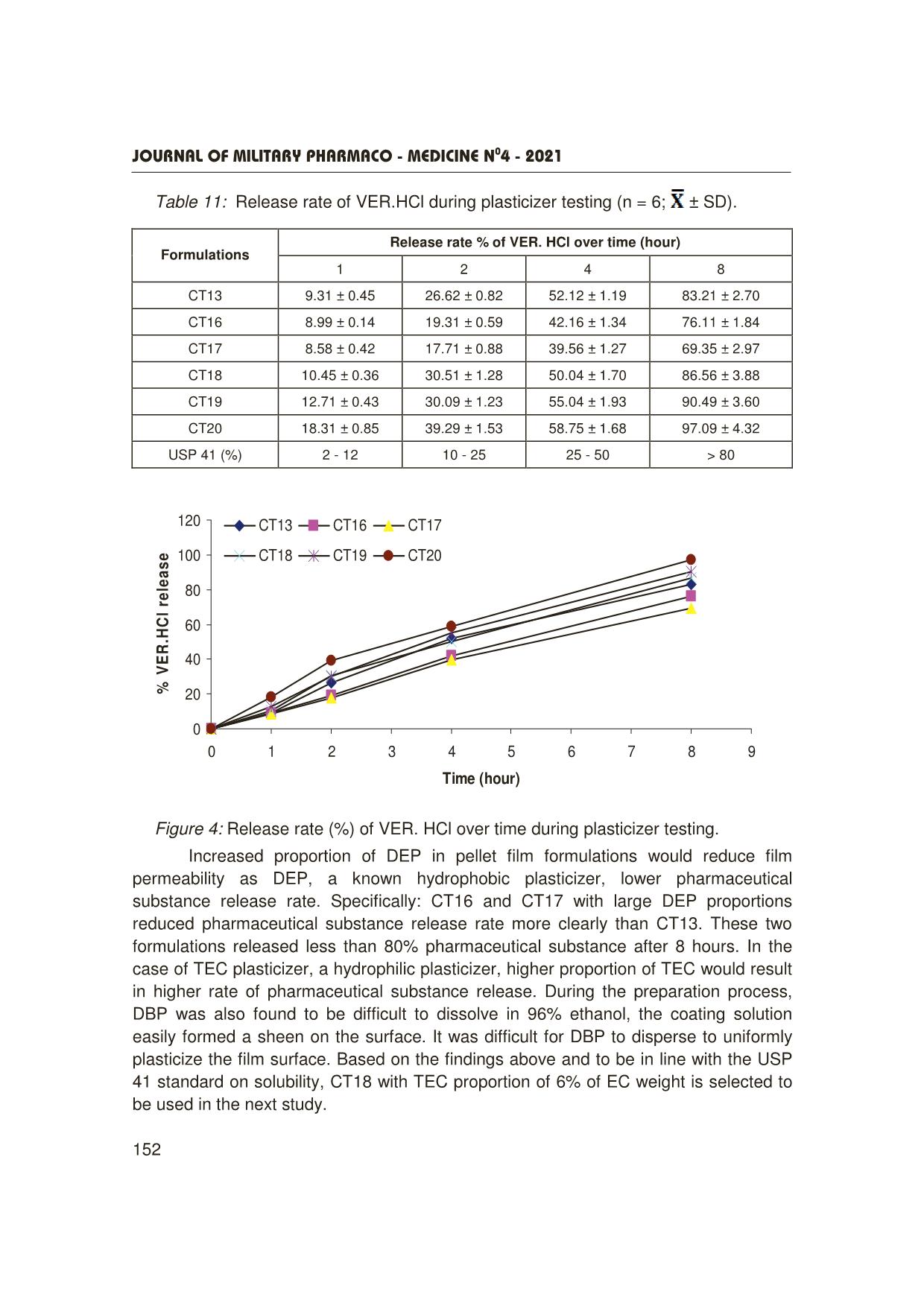
Trang 10
Tải về để xem bản đầy đủ
Tóm tắt nội dung tài liệu: Research on film coating formulation of sustained release pellets of verapamil hydrochloride
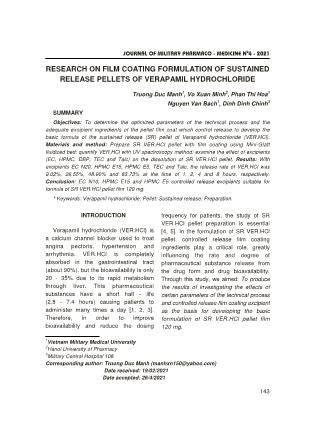
Journal OF MILITARY PHARMACO - MEDICINE N04 - 2021 143 RESEARCH ON FILM COATING FORMULATION OF SUSTAINED RELEASE PELLETS OF VERAPAMIL HYDROCHLORIDE Truong Duc Manh1, Vo Xuan Minh2, Phan Thi Hoa1 Nguyen Van Bach1, Dinh Dinh Chinh3 SUMMARY Objectives: To determine the optimized parameters of the technical process and the adequate excipient ingredients of the pellet film coat which control release to develop the basic formula of the sustained release (SR) pellet of Verapamil hydrochloride (VER.HCl). Materials and method: Prepare SR VER.HCl pellet with film coating using Mini-Glatt fluidized bed; quantify VER.HCl with UV spectroscopy method; examine the effect of excipients (EC, HPMC, DBP, TEC and Talc) on the dissolution of SR VER.HCl pellet. Results: With excipients EC N20, HPMC E15, HPMC E5, TEC and Talc, the release rate of VER.HCl was 9.02%, 26.55%, 48.90% and 83.73% at the time of 1, 2, 4 and 8 hours, respectively. Conclusion: EC N10, HPMC E15 and HPMC E5 controlled release excipients suitable for formula of SR VER.HCl pellet film 120 mg. * Keywords: Verapamil hydrochloride; Pellet; Sustained release; Preparation. INTRODUCTION Verapamil hydrochloride (VER.HCl) is a calcium channel blocker used to treat angina pectoris, hypertension and arrhythmia. VER.HCl is completely absorbed in the gastrointestinal tract (about 90%), but the bioavailability is only 20 - 35% due to its rapid metabolism through liver. This pharmaceutical substances have a short half - life (2.8 - 7.4 hours) causing patients to administer many times a day [1, 2, 3]. Therefore, in order to improve bioavailability and reduce the dosing frequency for patients, the study of SR VER.HCl pellet preparation is essential [4, 5]. In the formulation of SR VER.HCl pellet, controlled release film coating ingredients play a critical role, greatly influencing the rate and degree of pharmaceutical substance release from the drug form and drug bioavailability. Through this study, we aimed: To produce the results of investigating the effects of certain parameters of the technical process and controlled release film coating excipient as the basis for developing the basic formulation of SR VER.HCl pellet film 120 mg. 1Vietnam Military Medical University 2Hanoi University of Pharmacy 3Military Central Hospital 108 Corresponding author: Truong Duc Manh (manhxn150@yahoo.com) Date received: 19/02/2021 Date accepted: 26/4/2021 Journal OF MILITARY PHARMACO - MEDICINE N04 - 2021 144 MATERIALS AND METHODS 1. Materials and equipment *Materials and chemicals: VER.HCl Standard: Provided by Ho Chi Minh City Drug Quality Control Institute (QT242010914, concentration 100.52%), Pharmaceutical VER.HCl: USP 38 (China), HPMC E6, E15: USP 38 (China), Talc: USP 38 (China), EC N10, N20: USP 38 (China), DBP: USP 38 (India), TEC: USP 38 (China), Ethanol 96%: Vietnamese Pharmacopoeia IV. *Equipment and tools: Mini-Glatt film coating fluidized bed (Germany), Copley DIS 8000 dissolution tester (UK), Labomed UV-VIS spectrophotometer UVD-2960 (USA), analytical balance Mettler Toledo with readability down to 0.1 mg (Switzerland), PHARMATEST PTF E abrasion tester (Germany), ERWEKA SVM powder and granule tapped volume tester (Germany), ERWEKA GWF granular tester (Germany), sieve analysis (China) and other tools meeting laboratory and analytical testing standards. 2. Methods *Preparation of VER.HCl controlled release pellets by pan coating technique: SR VER.HCl pellet was prepared by coating a release control film onto the core pellet which is a composition including: EC (release control polymer), HPMC (creating diffusion channel), DBP, TEC (plasticizer), Talc (anti-sticking agent), 96% ethanol (solvent). The process of coating release control film was carried out in steps as follows: - Prepare coating solution: Soak and dissolve completely EC in approximately 2/3 of 96% ethanol, add HPMC to dissolve. Add plasticizer to the solution above, stir to homogenize. Crush talcum powder, sift through a 125 µm sieve. Add 96% ethanol and grind thoroughly, and pull gradually into the beaker containing coating solution. Stir the solution on a magnetic stirrer for about 30 minutes. Filter through a 125 µm sieve to obtain a homogeneous coating solution. Make up to the needed volume with 96% ethanol. The solution was stirred continuously on a magnetic stirrer throughout the coating process. - Put pellets in the coating equipment: Dry pellets for about 15 minutes to heat up before spraying on the coating. Spray the coating solution. Keep spraying until coating solution runs out, leave the equipment on for another 15 minutes. Table 1: Parameters of the coating process. Spray pressure to be determined Spray rate to be determined Fluidizing air volume to be determined Inlet air temperature 55 ± 5°C Outlet air temperature 42 ± 1°C Spray gun diameter 1.2 mm - The obtained pellets were dried at 60°C for 6 hours and left overnight for the coating film to stabilize, then sifted to retain diameter of 0.8 - 1.5 mm. - Film coating performance: calculated by the formula: Film-coating efficiency (%) = 3 21 m mm − x 100% Of which: m1: Total weight of pellet after coating (g); m2: Weight of core pellet before coating (g); m3: Weight of solids in the formula of film coat (g). Journal OF MILITARY PHARMACO - MEDICINE N04 - 2021 145 * Drug content: - Test sample: Weigh approximately 2g of pellet, grind into fine powder. Precisely weigh the corresponding amount of fine powder to roughly 50 mg of VER.HCl. Transfer to a 50 mL beaker. Add approximately 30 mL of pH 7.5 phosphate buffer solution. Shake in ultrasonic shaker for 60 mins. Transfer to a 50 mL volumetric flask, add phosphate buffer of pH 7.5 to the mar ... ry out coating each batch of 20g core pellets of VER.HCl. Testing results of the film forming polymer concentration were shown in table 5 and figure 1. Journal OF MILITARY PHARMACO - MEDICINE N04 - 2021 148 Table 5: Release rate of VER.HCl during EC proportion testing (n = 6; ± SD) Release rate of VER.HCl over time (hour) Formulations 1 2 4 8 CT1 42.08 ± 1.04 72.74 ± 1.66 86.84 ± 1.03 101.19 ± 1.53 CT2 21.65 ± 1.13 47.43 ± 1.12 67.92 ± 1.98 95.21 ± 1.97 CT3 17.42 ± 0.76 31.70 ± 0.90 61.20 ± 1.40 83.29 ± 3.35 CT4 6.91 ± 0.12 8.95 ± 0.43 18.83 ± 0.82 29.76 ± 1.05 CT5 6.11 ± 0.05 7.18 ± 0.10 11.07 ± 0.37 13.32 ± 0.75 CT6 5.67 ± 0.02 5.68 ± 0.02 5.82 ± 0.05 6.15 ± 0.07 USP 41 (%) 2 - 12 10 - 25 25 - 50 > 80 0 20 40 60 80 100 120 0 1 2 3 4 5 6 7 8 9 Time (hour) % VE R. HC l r e le a se CT1 CT2 CT3 CT4 CT5 CT6 Figure 1: The release rate of VER.HCl over time during EC proportion testing. Increased proportion of both types of EC in the film ingredients reduced the release rate of VER.HCl as when the EC proportion increases, the pellet film thickness also increases, thereby increasing the diffusion distance leading to a decrease in the release rate of pharmaceutical substance to the dissolved medium. With EC N10 film forming polymer, all three formulations yielded higher rate of pharmaceutical substance release than criteria in USP41. Particularly, at 1 hour, all three formulations CT1, CT2 and CT3 showed the release rate of pharmaceutical substance higher than 12%. 4 hours later, it exceeded 50% and these formulations were almost completely released 8 hours later. The formulation using 5g of EC (CT3 and CT6), the coating had some difficulties due to the increased viscosity of the film-forming suspension resulting in pellet agglutination. Thus, EC N10 is not adequate to be used as an ingredient of release control VER.HCl pellet film. Replace EC N10 with EC N20, all three formulations adequately controlled rate of pharmaceutical substance release. CT5 and CT6 gave the lowest rate of drug release due to great film thickness which prevented VER.HCl from diffusing into the dissolved medium. After 8 hours, both CT5 and CT6 yielded rate lower than 15%. CT4 using 3g of EC N20 was capable of controlling pharmaceutical substance release. As a result, CT4 was selected for the next studies. Journal OF MILITARY PHARMACO - MEDICINE N04 - 2021 149 - Effects of the proportion and type of polymer combination: As CT4 gave a relatively small rate of pharmaceutical substance release compared to what was required by USP 41, it was necessary to increase the rate of pharmaceutical substance release by combining some hydrophilic polymers to create diffusion channels on the pellet film to enhance the rate. Based on the formulations designed as in table 6, the dissolution is evaluated and presented as results in table 7 and figure 2. Table 6: Formulations designed to determine the optimized proportion of polymer combination. Formulations Ingredients CT4 CT7 CT8 CT9 CT10 CT11 CT12 EC N20 (g) 3 3 3 3 3 3 3 HPMC E6 (% w/w EC) 0 15.0 17.5 20.0 0 0 0 HPMC E15 (% w/w EC) 0 0 0 0 15.0 17.5 20.0 DBP (% w/w EC) 6 6 6 6 6 6 6 Talc (% w/w EC) 50 50 50 50 50 50 50 EtOH 96% (mL) 50 50 50 50 50 50 50 Table 7: Released rate of VER.HCl during polymer combination proportion testing (n = 6; ± SD). Rate of VER. HCl released over time (hour) Formulations 1 2 4 8 CT4 6.91 ±0.12 8.95±0.43 18.83±0.82 29.76±1.05 CT7 7.44±0.13 17.89±0.83 38.67±1.16 66.74±1.38 CT8 16.95±0.85 35.93±0.97 83.77±2.16 93.54±2.16 CT9 30.06±0.90 50.12±1.56 91.27±4.21 98.66±3.97 CT10 7.21±0.36 8.73±0.13 16.68±0.79 27.24±1.06 CT11 8.02±0.11 19.93±0.89 40.23±0.81 70.30±2.52 CT12 18.02±0.58 28.88±1.15 55.03±1.49 84.34±2.61 USP 41 (%) 2-12 10-25 25-50 > 80 0 20 40 60 80 100 120 0 1 2 3 4 5 6 7 8 9 Time (hour) % VE R. HC l r e le a s e CT4 CT7 CT8 CT9 CT10 CT11 CT12 Figure 2: The release rate of VER.HCl over time during polymer combination proportion testing. Journal OF MILITARY PHARMACO - MEDICINE N04 - 2021 150 Increased amount of HPMC E6 and E15 enhanced the release rate of pharmaceutical substance of the formulation due to an increase in the number of pharmaceutical substance diffusion channels. The results showed that all six formulations increased the release rate of pharmaceutical substance compared to F4. With both types of HPMC used at low levels (CT7 and CT10), the rate after 8 hours of release was lower than 70% as compared to high levels (20%), the release rate of the formulation exceeded the requirement by USP 41. With two types of polymers, HPMC E15 controlled release better than E5 due to its higher viscosity. Based on the obtained results above, CT11 was selected (HPMC E15 = 17.5% compared to EC) to be used in the next studies. - Effects of HPMC E6 and HPMC E15 proportion: Based on HPMC type testing, it was found that HPMC E5 with lower viscosity would give higher rate of pharmaceutical substance release in the first hours while HPMC E15 with higher viscosity would corrode and swell more slowly enabling it to control pharmaceutical substance release in hours that follow. Therefore, it is necessary to select the combination of these two polymers to be used in pellet film ingredients. However, since HPMC has poorer solubility in ethanol than water, an additional 5 mL of distilled water should be used to dissolve HPMC. Based on the formulations designed as in table 8, the dissolution was evaluated and presented as results in table 9 and figure 3. Table 8: Formulations designed to determine the optimized HPMC E6 and HPMC E15 combination proportion. Formulations Ingredients CT11 CT13 CT14 CT15 EC N20 (g) 3 3 3 3 HPMC E6 (% w/w EC) 0 2.5 5.0 7.5 HPMC E15 (% w/w EC) 17.5 15.0 12.5 10.0 DBP (% w/w EC) 6 6 6 6 Talc (% w/w EC) 50 50 50 50 Distilled water (mL) 5 5 5 5 EtOH 96% (mL) 50 50 50 50 Table 9: The release rate of VER.HCl during HPMC E6 and HPMC E15 combination proportion testing (n = 6; ± SD). Release rate of VER. HCl over time (hour) Formulations 1 2 4 8 CT11 8.02 ± 0.11 19.93 ± 0.89 40.23 ± 0.81 70.30 ± 2.52 CT13 9.31 ± 0.45 26.62 ± 0.82 52.12 ± 1.19 83.21 ± 2.70 CT14 13.65 ± 0.54 30.06 ± 2.21 56.81 ± 0.59 89.30 ± 3.50 CT15 21.47 ± 0.98 42.33 ± 1.29 65.09 ± 1.44 96.84 ± 3.34 USP 41 (%) 2 - 12 10 - 25 25 - 50 > 80 Journal OF MILITARY PHARMACO - MEDICINE N04 - 2021 151 0 20 40 60 80 100 120 0 1 2 3 4 5 6 7 8 9 Time (hour) % VE R. HC l r el ea se CT11 CT13 CT14 CT15 Figure 3: The release rate of VER. HCl over time during HPMC E6 and HPMC E15 combination proportion testing. Reduced HPMC E15/HPMC E6 increased the release rate of pharmaceutical substance of all formulations due to an increase in the weight of HPMC E5 in the polymer mixture. The results showed that all three formulations increased the rate compared to CT11 (without HPMC E5). CT14 and CT15 (using HPMC E5 at 5% and 7.5%) which yielded higher release rate of pharmaceutical substance in the first hours due to low viscosity accounted for a large proportion in the combined polymer mixture. They absorbed water and dissolved quickly creating porous diffusion in pellet film, thus released more pharmaceutical substances than CT13 (HPMC E15 = 2.5% compared to EC). Based on the findings above, CT13 (HPMC E15 = 2.5% compared to EC) was selected to be used in the next study. - Effects of plasticizer: Testing with two plasticizers, DBP and TEC were conducted. Based on the formulations designed as in table 10, the dissolution was evaluated and presented as results in table 11 and figure 4. Table 10: Formulations designed to determine the optimized plasticizer. Formulations Ingredients CT13 CT16 CT17 CT18 CT19 CT20 EC N20 (g) 3 3 3 3 3 3 HPMC E6 (% w/w EC) 2.5 2.5 2.5 2.5 2.5 2.5 HPMC E15 (% w/w EC) 15.0 15.0 15.0 15.0 15.0 15.0 DBP (% w/w EC) 6 8 10 - - - TEC (% w/w EC) - - - 6 8 10 Talc (% w/w EC) 50 50 50 50 50 50 Distilled water (mL) 5 5 5 5 5 5 EtOH 96% (mL) 50 50 50 50 50 50 Journal OF MILITARY PHARMACO - MEDICINE N04 - 2021 152 Table 11: Release rate of VER.HCl during plasticizer testing (n = 6; ± SD). Release rate % of VER. HCl over time (hour) Formulations 1 2 4 8 CT13 9.31 ± 0.45 26.62 ± 0.82 52.12 ± 1.19 83.21 ± 2.70 CT16 8.99 ± 0.14 19.31 ± 0.59 42.16 ± 1.34 76.11 ± 1.84 CT17 8.58 ± 0.42 17.71 ± 0.88 39.56 ± 1.27 69.35 ± 2.97 CT18 10.45 ± 0.36 30.51 ± 1.28 50.04 ± 1.70 86.56 ± 3.88 CT19 12.71 ± 0.43 30.09 ± 1.23 55.04 ± 1.93 90.49 ± 3.60 CT20 18.31 ± 0.85 39.29 ± 1.53 58.75 ± 1.68 97.09 ± 4.32 USP 41 (%) 2 - 12 10 - 25 25 - 50 > 80 0 20 40 60 80 100 120 0 1 2 3 4 5 6 7 8 9 Time (hour) % VE R. HC l r el ea se CT13 CT16 CT17 CT18 CT19 CT20 Figure 4: Release rate (%) of VER. HCl over time during plasticizer testing. Increased proportion of DEP in pellet film formulations would reduce film permeability as DEP, a known hydrophobic plasticizer, lower pharmaceutical substance release rate. Specifically: CT16 and CT17 with large DEP proportions reduced pharmaceutical substance release rate more clearly than CT13. These two formulations released less than 80% pharmaceutical substance after 8 hours. In the case of TEC plasticizer, a hydrophilic plasticizer, higher proportion of TEC would result in higher rate of pharmaceutical substance release. During the preparation process, DBP was also found to be difficult to dissolve in 96% ethanol, the coating solution easily formed a sheen on the surface. It was difficult for DBP to disperse to uniformly plasticize the film surface. Based on the findings above and to be in line with the USP 41 standard on solubility, CT18 with TEC proportion of 6% of EC weight is selected to be used in the next study. Journal OF MILITARY PHARMACO - MEDICINE N04 - 2021 153 - Effect of anti-sticking agent: Testing out formulations with different talc proportions as shown in table 12 and coating on 20g pellets with 50 mL of coating solution containing approximately 10% solids with similar coating performance. Dissolution evaluation results are shown in table 13 and figure 5. Table 12: Formulations designed to determine the optimized anti-sticking agent. Formulations Ingredients CT18 CT21 CT22 CT23 EC N20 (g) 3 3 3 3 HPMC E6 (% w/w EC) 2.5 2.5 2.5 2.5 HPMC E15 (% w/w EC) 15.0 15.0 15.0 15.0 Talc (% w/w EC) 50 60 40 30 TEC (% w/w EC) 6 6 6 6 Distilled water (mL) 5 5 5 5 96% EtOH (mL) 50 50 50 50 Table 13: Release rate of VER.HCl during anti-sticking agent testing (n = 6; ± SD). Release rate % of VER. HCl over time (hour) Formulations 1 2 4 8 CT18 10.45 ± 0.36 30.51 ± 1.28 50.04 ± 1.70 86.56 ± 3.88 CT21 22.90 ± 1.02 46.90 ± 2.03 79.54 ± 3.09 97.33 ± 3.69 CT22 9.02 ± 0.14 26.55 ± 1.20 48.90 ± 1.42 83.73 ± 2.70 CT23 32.65 ± 1.24 60.11 ± 1.65 90.59 ± 3.37 98.18 ± 4.09 USP 41 (%) 2 - 12 10 - 25 25 - 50 > 80 0 20 40 60 80 100 120 0 1 2 3 4 5 6 7 8 9 Time (hour) % VE R. HC l r el ea se CT18 CT21 CT22 CT23 Figure 5: The rate of VER. HCl released over time during anti-sticking agent testing. Journal OF MILITARY PHARMACO - MEDICINE N04 - 2021 154 With a small talc proportion (30%), the release rate of pharmaceutical substance obtained was more than 30%. The cause may be due to the insufficient amount of talc which failed to prevent agglutination during the coating process, ultimately causing agglutination and puncture in pellet films. As for the large talc proportion (60%), high rate of pharmaceutical substance release was also obtained (22.9% after 1 hour) for which the reason was that an excessive amount of talc powder led to unstable and cracked films when measuring solubility. CT18 and CT22 have similar solubility curves, the less the amount of talc, the slower pharmaceutical substance is to release. It was observed that CT22 released more slowly and gave the release rate of pharmaceutical substance at all hours closer to what is stipulated by USP 41. CONCLUSIONS - Having determined the effects of certain parameters of the technical film coating process to control the release of core pellet of VER.HCl. With parameters such as: Spray pressure: 1.2 bar, spray rate: 0.85 mL/min, fluidizing air volume: 18 m3/hour, inlet air temperature: 55 ± 5°C, outlet air temperature: 42 ± 1°C, spray gun diameter: 1.2 mm, the coating process gave a high efficiency (73.21%) in which pellet fluidizing was stable, uniform and smooth surface finish was achieved. - Having selected release control excipients EC N20 as well as two hydrophilic polymers, HPMC E15/E6, to create diffusion channels, from which the pellet film formulation is formulated consisting of: EC N20, HPMC E6, HPMC E15, Talc, TEC, distilled water and EtOH 96%. REFERENCES 1. Ministry of Health. Vietnamese National Drug Formulary. Medical Publishing House 2015. 2. Anthony CM, et al. Clarke’ s analysis of drugs and poisons. Pharmaceutical Press. London 2011: 2223-2224. 3. Sweetman SC, et al. Martindale 36th, RPS Publishing 2009:1522-1526. 4. Nitin DJ, Dipak DG, Ashish AH, et al. Formulation development and evaluation of sustained release pellets of verapamil HCl. International Journal of Pharma Research and Development 2010; 1(11):1-7. 5. Vidyadhara S, Prasad MB, Sasidhar RLC, et al. Development and evaluation of controlled release verapamil hydrochloride pellets by pan coating process. Current Trends in Biotechnology and Pharmacy 2013; 7(1):535-543. 6. USP 41-NF 36. Monographs: Verapamil hydrochlorid extended-release tablets 2018; 4307-4311.
File đính kèm:
research_on_film_coating_formulation_of_sustained_release_pe.pdf