Influence of Sintering Additives on the Porous Structure and Mechanical Properties of Porous Alumina
The aim of the present work is to investigate and to compare the influence of the two sintering additives
Cr2O3 and TiO2 on the porous structure and the mechanical properties of the sintered porous alumina.
Alumina based porous ceramics were fabricated by sacrificial template technique via powder metallurgy
route from alumina powder using ammonium bicarbonate (NH4)HCO3 as the pore former. The results
showed that the use of sintering additives led to a remarkble enhancement of the bonding between alumina
particles hence the strength of the alumina based porous ceramics. Between the two sintering additives,
TiO2 was more effective in aiding sintering (densification) of alumina than Cr2O3. Consequently, the sintered
porous alumina using TiO2 as sintering additive has a smaller pore size, 19030 m compared to 22040
m of that with Cr2O3, and lower porosity. The porosity of the sintered samples increased with the
concentration of the pore-forming agents and reaches the highest value of 79.3 % and 82.6% corresponding
to TiO2 and Cr2O3 used. The mechanical strength of the porous alumina varied inversely with porosity.
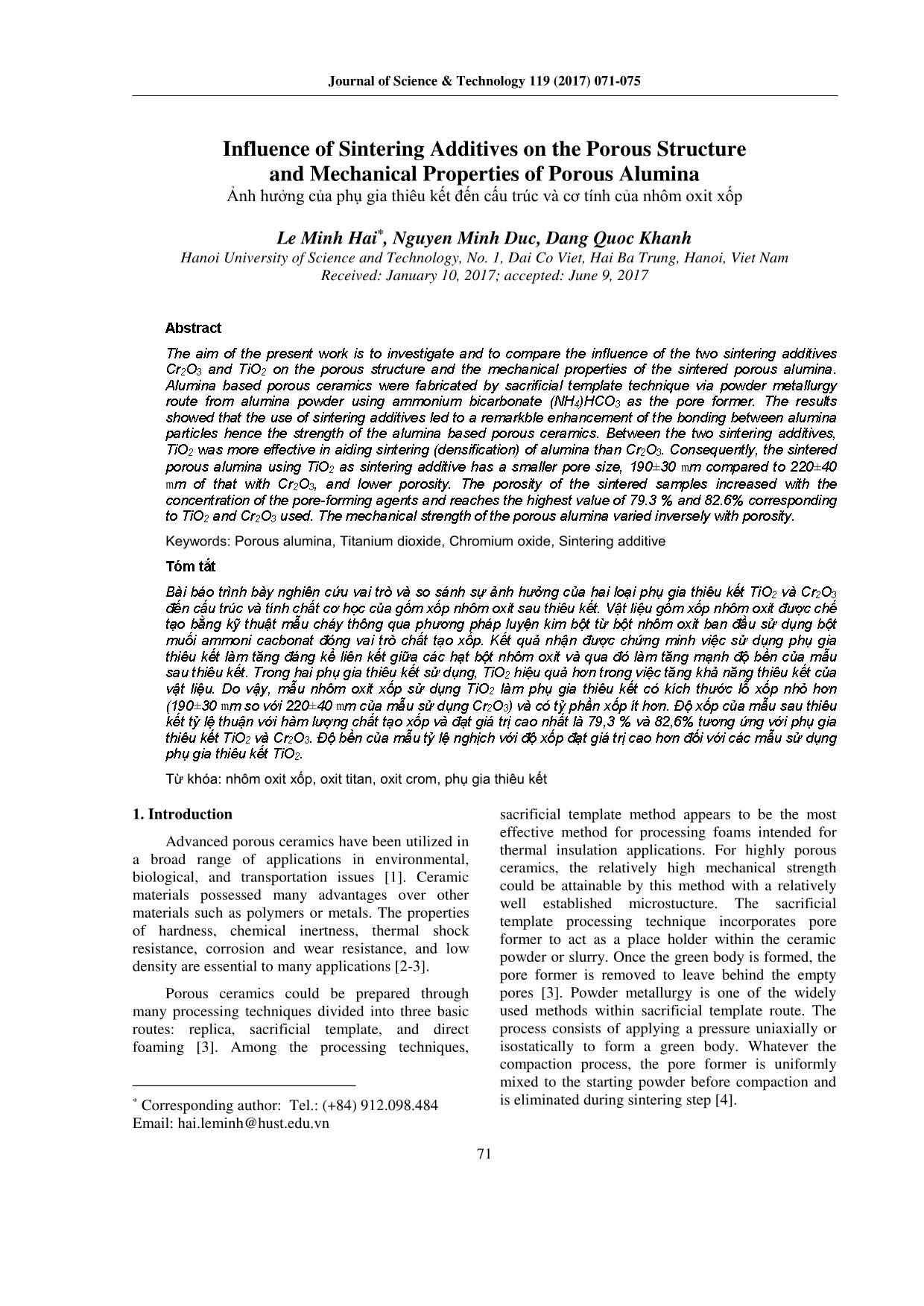
Trang 1
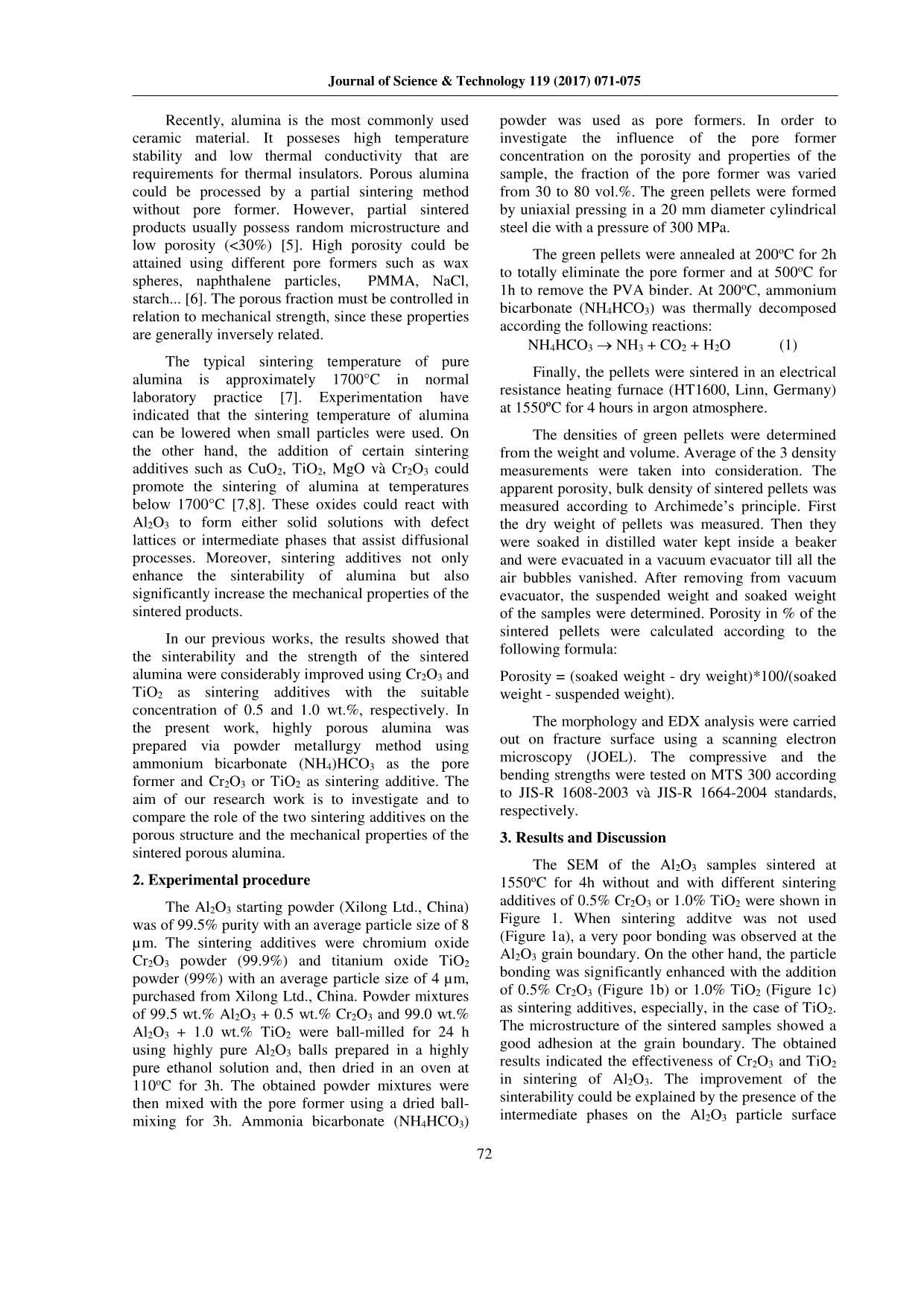
Trang 2
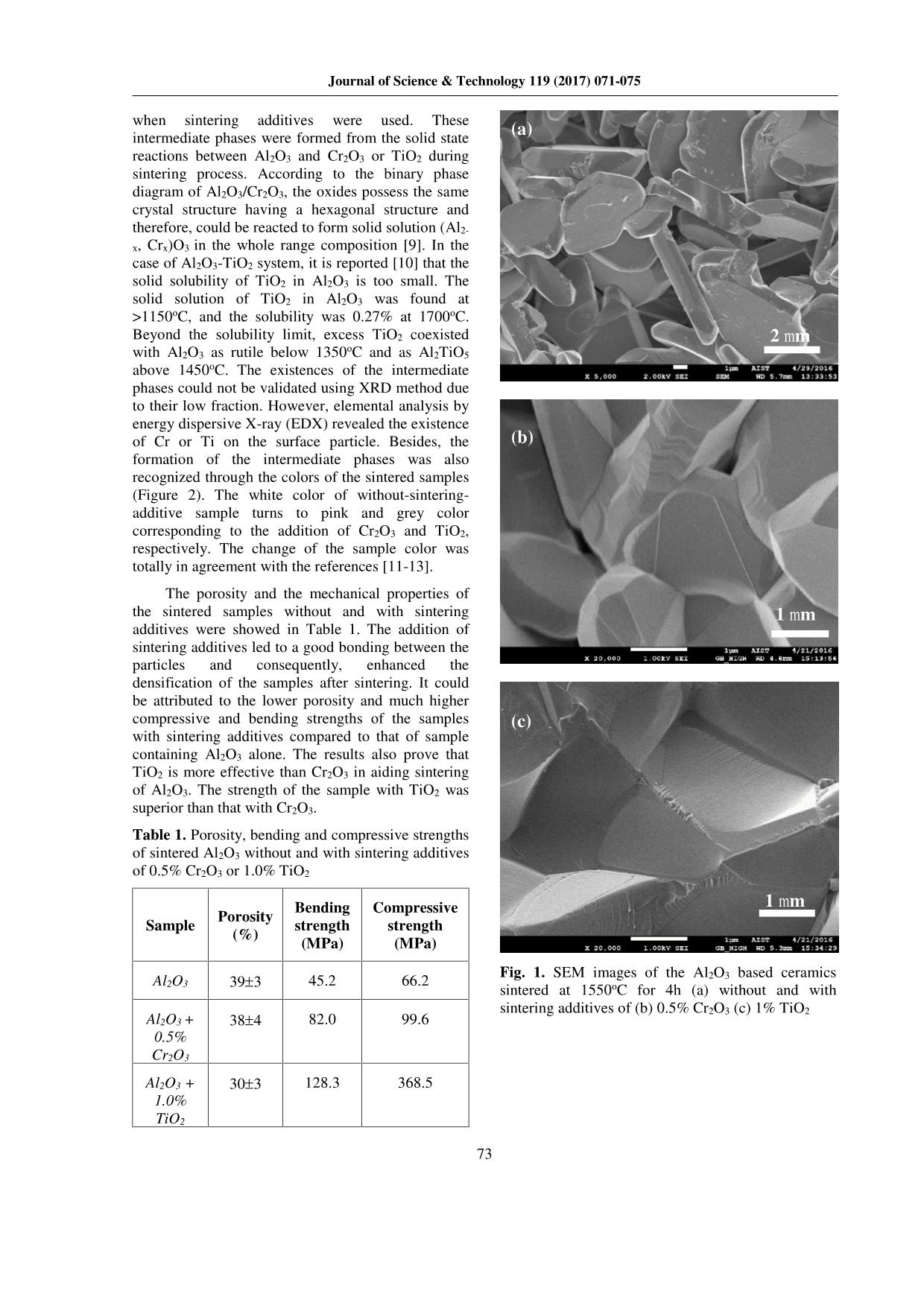
Trang 3
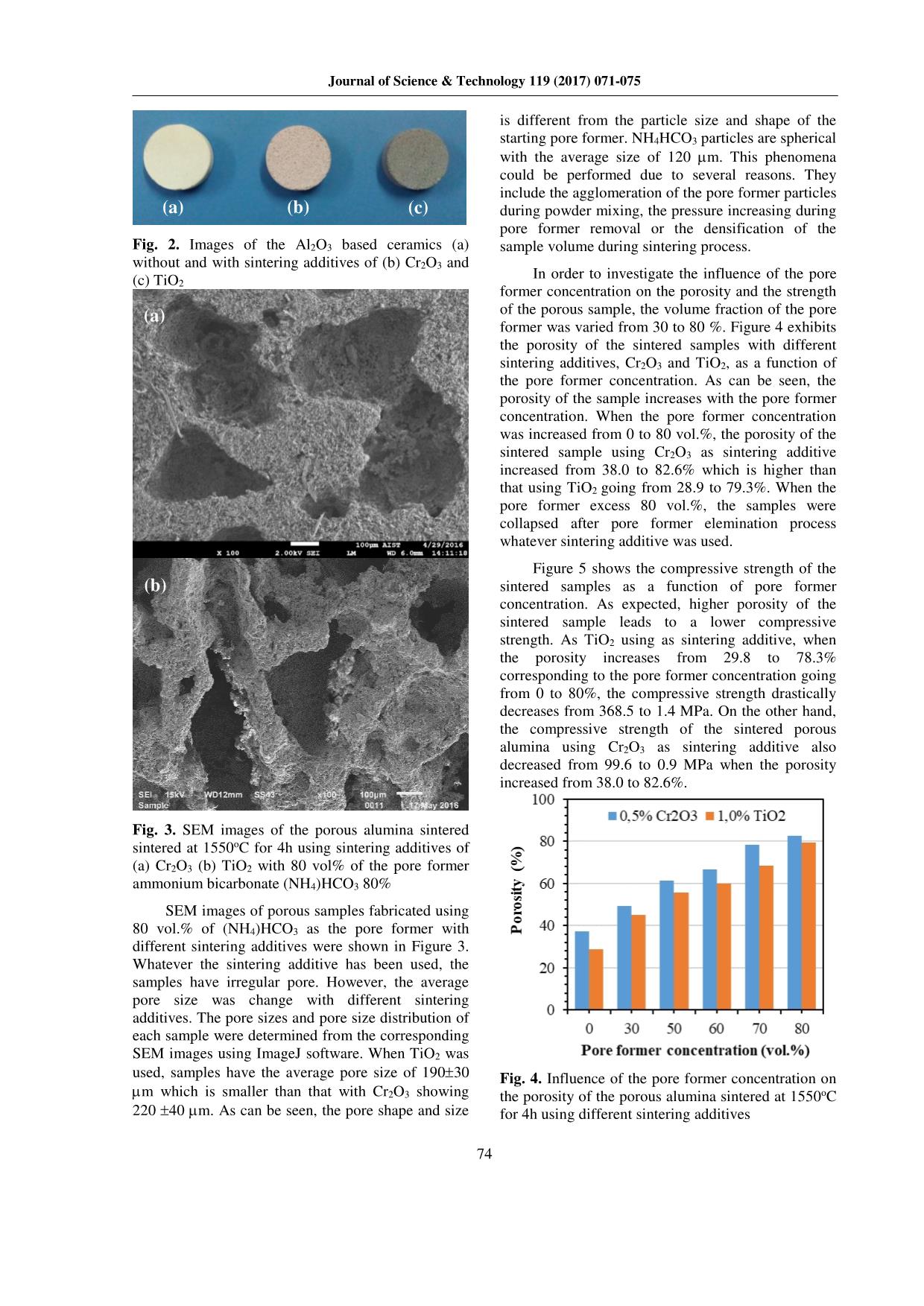
Trang 4
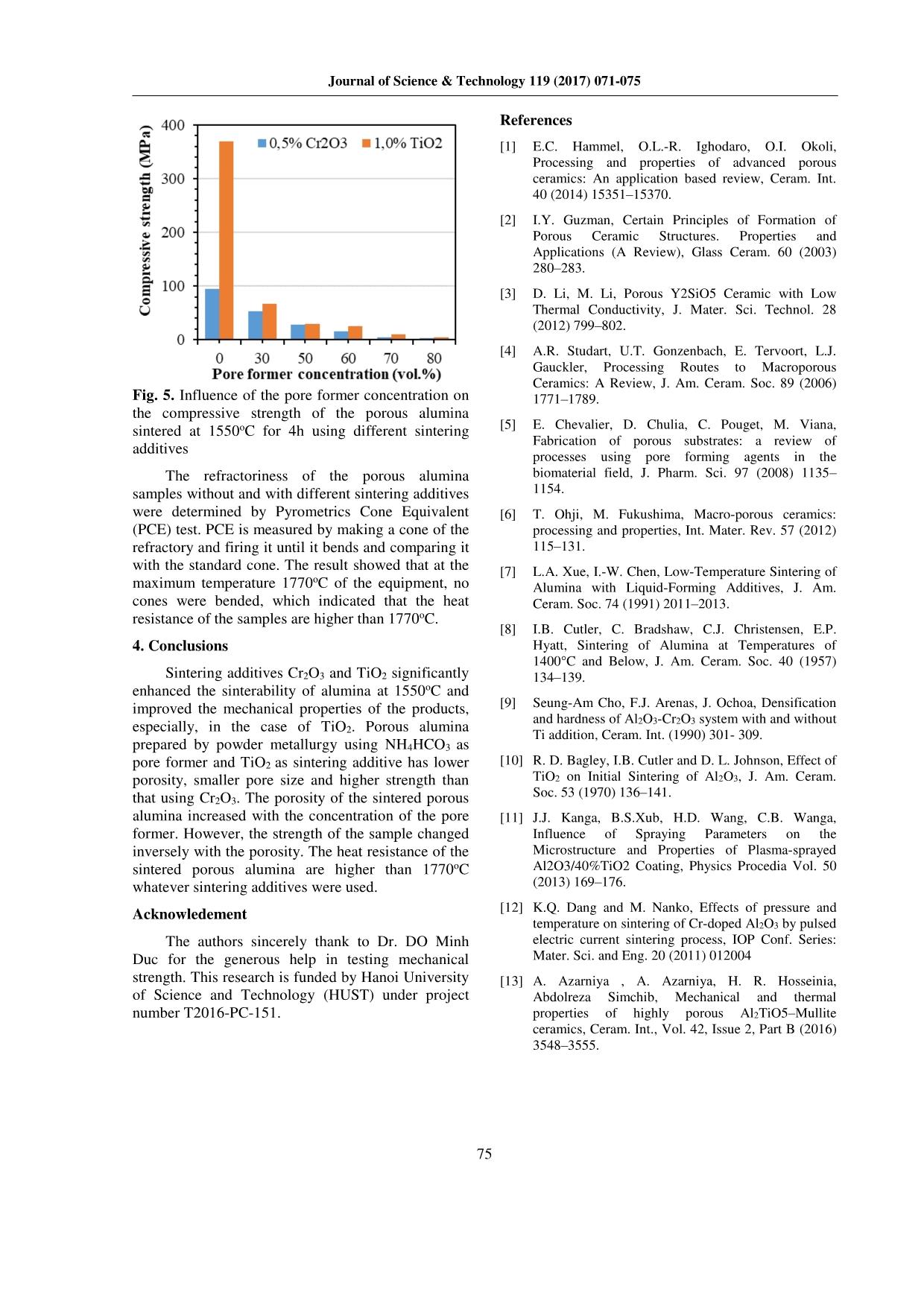
Trang 5
Tóm tắt nội dung tài liệu: Influence of Sintering Additives on the Porous Structure and Mechanical Properties of Porous Alumina
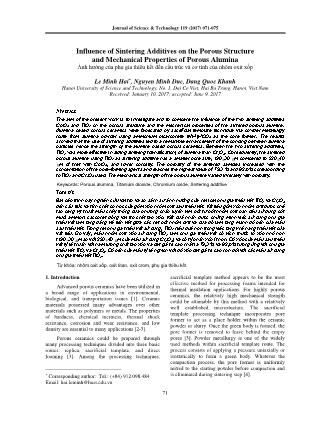
Journal of Science & Technology 119 (2017) 071-075 71 Influence of Sintering Additives on the Porous Structure and Mechanical Properties of Porous Alumina Ảnh hưởng của phụ gia thiêu kết đến cấu trúc và cơ tính của nhôm oxit xốp Le Minh Hai*, Nguyen Minh Duc, Dang Quoc Khanh Hanoi University of Science and Technology, No. 1, Dai Co Viet, Hai Ba Trung, Hanoi, Viet Nam Received: January 10, 2017; accepted: June 9, 2017 Abstract The aim of the present work is to investigate and to compare the influence of the two sintering additives Cr2O3 and TiO2 on the porous structure and the mechanical properties of the sintered porous alumina. Alumina based porous ceramics were fabricated by sacrificial template technique via powder metallurgy route from alumina powder using ammonium bicarbonate (NH4)HCO3 as the pore former. The results showed that the use of sintering additives led to a remarkble enhancement of the bonding between alumina particles hence the strength of the alumina based porous ceramics. Between the two sintering additives, TiO2 was more effective in aiding sintering (densification) of alumina than Cr2O3. Consequently, the sintered porous alumina using TiO2 as sintering additive has a smaller pore size, 190 30 m compared to 220 40 m of that with Cr2O3, and lower porosity. The porosity of the sintered samples increased with the concentration of the pore-forming agents and reaches the highest value of 79.3 % and 82.6% corresponding to TiO2 and Cr2O3 used. The mechanical strength of the porous alumina varied inversely with porosity. Keywords: Porous alumina, Titanium dioxide, Chromium oxide, Sintering additive Tóm tắt Bài báo trình bày nghiên cứu vai trò và so sánh sự ảnh hưởng của hai loại phụ gia thiêu kết TiO2 và Cr2O3 đến cấu trúc và tính chất cơ học của gốm xốp nhôm oxit sau thiêu kết. Vật liệu gốm xốp nhôm oxit được chế tạo bằng kỹ thuật mẫu cháy thông qua phương pháp luyện kim bột từ bột nhôm oxit ban đầu sử dụng bột muối ammoni cacbonat đóng vai trò chất tạo xốp. Kết quả nhận được chứng minh việc sử dụng phụ gia thiêu kết làm tăng đáng kể liên kết giữa các hạt bột nhôm oxit và qua đó làm tăng mạnh độ bền của mẫu sau thiêu kết. Trong hai phụ gia thiêu kết sử dụng, TiO2 hiệu quả hơn trong việc tăng khả năng thiêu kết của vật liệu. Do vậy, mẫu nhôm oxit xốp sử dụng TiO2 làm phụ gia thiêu kết có kích thước lỗ xốp nhỏ hơn (190 30 m so với 220 40 m của mẫu sử dụng Cr2O3) và có tỷ phần xốp ít hơn. Độ xốp của mẫu sau thiêu kết tỷ lệ thuận với hàm lượng chất tạo xốp và đạt giá trị cao nhất là 79,3 % và 82,6% tương ứng với phụ gia thiêu kết TiO2 và Cr2O3. Độ bền của mẫu tỷ lệ nghịch với độ xốp đạt giá trị cao hơn đối với các mẫu sử dụng phụ gia thiêu kết TiO2. Từ khóa: nhôm oxit xốp, oxit titan, oxit crom, phụ gia thiêu kết 1. Introduction1 Advanced porous ceramics have been utilized in a broad range of applications in environmental, biological, and transportation issues [1]. Ceramic materials possessed many advantages over other materials such as polymers or metals. The properties of hardness, chemical inertness, thermal shock resistance, corrosion and wear resistance, and low density are essential to many applications [2-3]. Porous ceramics could be prepared through many processing techniques divided into three basic routes: replica, sacrificial template, and direct foaming [3]. Among the processing techniques, * Corresponding author: Tel.: (+84) 912.098.484 Email: hai.leminh@hust.edu.vn sacrificial template method appears to be the most effective method for processing foams intended for thermal insulation applications. For highly porous ceramics, the relatively high mechanical strength could be attainable by this method with a relatively well established microstucture. The sacrificial template processing technique incorporates pore former to act as a place holder within the ceramic powder or slurry. Once the green body is formed, the pore former is removed to leave behind the empty pores [3]. Powder metallurgy is one of the widely used methods within sacrificial template route. The process consists of applying a pressure uniaxially or isostatically to form a green body. Whatever the compaction process, the pore former is uniformly mixed to the starting powder before compaction and is eliminated during sintering step [4]. Journal of Science & Technology 119 (2017) 071-075 72 Recently, alumina is the most commonly used ceramic material. It posseses high temperature stability and low thermal conductivity that are requirements for thermal insulators. Porous alumina could be processed by a partial sintering method without pore former. However, partial sintered products usually possess random microstructure and low porosity (<30%) [5]. High porosity could be attained using different pore formers such as wax spheres, naphthalene particles, PMMA, NaCl, starch... [6]. The porous fraction must be controlled in relation to mechanical strength, since these properties are generally inversely related. The typical sintering temperature of pure alumina is approximately 1700°C in normal laboratory practice [7]. Experimentation have indicated that the sintering temperature of alumina can be lowered when small particles were used. On the other hand, the addition of certain sintering additives such as CuO2, TiO2, MgO và Cr2O3 could promote the sintering of alumina at temperatures below 1700°C [7,8]. These oxides could react with Al2O3 to form either solid solutions with defect lattices or intermediate phases that assist diffusional processes. Moreover, sintering additives not only enhance the sinterability of alumina but also significantly increase the mechanical properties of the sintered products. In our previous works, the results showed that the sinterability and the strength of the sintered alumina were considerably improved using Cr2O3 and TiO2 as sintering additives with the suitable concentration of 0.5 and 1.0 wt.%, respectively. In the present work, highly porous alumina was prepared via powder metallurgy method using ammonium bicarbonate (NH4)HCO3 as the pore former and Cr2O3 or TiO2 as sintering additive. The aim of our research work is to investigate and to compare the role of the two sintering additives on the porous structure and the mechanical properties of the sintered porous alumina. 2. Experimental procedure The Al2O3 starting powder (Xilong Ltd., China) was of 99.5% purity with an average particle size of 8 µm. The sintering additives were chromium oxide Cr2O3 powder (99.9%) and titanium oxide TiO2 powder (99%) with an average particle size of 4 µm, purchased from Xilong Ltd., China. Powder mixtures of 99.5 wt.% Al2O3 + 0.5 wt.% Cr2O3 and 99.0 wt.% Al2O3 + 1.0 wt.% TiO2 were ball-milled for 24 h using highly pure Al2O3 balls prepared in a highly pure ethanol solution and, then dried in an oven at 110oC for 3h. The obtained powder mixtures were then mixed with the pore former using a dried ball- mixing for 3h. Ammonia bicarbonate (NH4HCO3) powder was used as pore formers. In order to investigate the influence of the pore former concentration on the porosity and properties of the sample, the fraction of the pore former was varied from 30 to 80 vol.%. The green pellets were formed by uniaxial pressing in a 20 mm diameter cylindrical steel die with a pressure of 300 MPa. The green pellets were annealed at 200oC for 2h to totally eliminate the pore former and at 500oC for 1h to remove the PVA binder. At 200oC, ammonium bicarbonate (NH4HCO3) was thermally decomposed according the following reactions: NH4HCO3 NH3 + CO2 + H2O (1) Finally, the pellets were sintered in an electrical resistance heating furnace (HT1600, Linn, Germany) at 1550ºC for 4 hours in argon atmosphere. The densities of green pellets were determined from the weight and volume. Average of the 3 density measurements were taken into consideration. The apparent porosity, bulk density of sintered pellets was measured according to Archimede’s principle. First the dry weight of pellets was measured. Then they were soaked in distilled water kept inside a beaker and were evacuated in a vacuum evacuator till all the air bubbles vanished. After removing from vacuum evacuator, the suspended weight and soaked weight of the samples were determined. Porosity in % of the sintered pellets were calculated according to the following formula: Porosity = (soaked weight - dry weight)*100/(soaked weight - suspended weight). The morphology and EDX analysis were carried out on fracture surface using a scanning electron microscopy (JOEL). The compressive and the bending strengths were tested on MTS 300 according to JIS-R 1608-2003 và JIS-R 1664-2004 standards, respectively. 3. Results and Discussion The SEM of the Al2O3 samples sintered at 1550oC for 4h without and with different sintering additives of 0.5% Cr2O3 or 1.0% TiO2 were shown in Figure 1. When sintering additve was not used (Figure 1a), a very poor bonding was observed at the Al2O3 grain boundary. On the other hand, the particle bonding was significantly enhanced with the addition of 0.5% Cr2O3 (Figure 1b) or 1.0% TiO2 (Figure 1c) as sintering additives, especially, in the case of TiO2. The microstructure of the sintered samples showed a good adhesion at the grain boundary. The obtained results indicated the effectiveness of Cr2O3 and TiO2 in sintering of Al2O3. The improvement of the sinterability could be explained by the presence of the intermediate phases on the Al2O3 particle surface Journal of Science & Technology 119 (2017) 071-075 73 when sintering additives were used. These intermediate phases were formed from the solid state reactions between Al2O3 and Cr2O3 or TiO2 during sintering process. According to the binary phase diagram of Al2O3/Cr2O3, the oxides possess the same crystal structure having a hexagonal structure and therefore, could be reacted to form solid solution (Al2- x, Crx)O3 in the whole range composition [9]. In the case of Al2O3-TiO2 system, it is reported [10] that the solid solubility of TiO2 in Al2O3 is too small. The solid solution of TiO2 in Al2O3 was found at >1150oC, and the solubility was 0.27% at 1700oC. Beyond the solubility limit, excess TiO2 coexisted with Al2O3 as rutile below 1350oC and as Al2TiO5 above 1450oC. The existences of the intermediate phases could not be validated using XRD method due to their low fraction. However, elemental analysis by energy dispersive X-ray (EDX) revealed the existence of Cr or Ti on the surface particle. Besides, the formation of the intermediate phases was also recognized through the colors of the sintered samples (Figure 2). The white color of without-sintering- additive sample turns to pink and grey color corresponding to the addition of Cr2O3 and TiO2, respectively. The change of the sample color was totally in agreement with the references [11-13]. The porosity and the mechanical properties of the sintered samples without and with sintering additives were showed in Table 1. The addition of sintering additives led to a good bonding between the particles and consequently, enhanced the densification of the samples after sintering. It could be attributed to the lower porosity and much higher compressive and bending strengths of the samples with sintering additives compared to that of sample containing Al2O3 alone. The results also prove that TiO2 is more effective than Cr2O3 in aiding sintering of Al2O3. The strength of the sample with TiO2 was superior than that with Cr2O3. Table 1. Porosity, bending and compressive strengths of sintered Al2O3 without and with sintering additives of 0.5% Cr2O3 or 1.0% TiO2 Sample Porosity(%) Bending strength (MPa) Compressive strength (MPa) Al2O3 39 3 45.2 66.2 Al2O3 + 0.5% Cr2O3 38 4 82.0 99.6 Al2O3 + 1.0% TiO2 30 3 128.3 368.5 Fig. 1. SEM images of the Al2O3 based ceramics sintered at 1550oC for 4h (a) without and with sintering additives of (b) 0.5% Cr2O3 (c) 1% TiO2 1 m (a) 1 m (b) (c) 2 m Journal of Science & Technology 119 (2017) 071-075 74 Fig. 2. Images of the Al2O3 based ceramics (a) without and with sintering additives of (b) Cr2O3 and (c) TiO2 Fig. 3. SEM images of the porous alumina sintered sintered at 1550oC for 4h using sintering additives of (a) Cr2O3 (b) TiO2 with 80 vol% of the pore former ammonium bicarbonate (NH4)HCO3 80% SEM images of porous samples fabricated using 80 vol.% of (NH4)HCO3 as the pore former with different sintering additives were shown in Figure 3. Whatever the sintering additive has been used, the samples have irregular pore. However, the average pore size was change with different sintering additives. The pore sizes and pore size distribution of each sample were determined from the corresponding SEM images using ImageJ software. When TiO2 was used, samples have the average pore size of 190 30 m which is smaller than that with Cr2O3 showing 220 40 m. As can be seen, the pore shape and size is different from the particle size and shape of the starting pore former. NH4HCO3 particles are spherical with the average size of 120 m. This phenomena could be performed due to several reasons. They include the agglomeration of the pore former particles during powder mixing, the pressure increasing during pore former removal or the densification of the sample volume during sintering process. In order to investigate the influence of the pore former concentration on the porosity and the strength of the porous sample, the volume fraction of the pore former was varied from 30 to 80 %. Figure 4 exhibits the porosity of the sintered samples with different sintering additives, Cr2O3 and TiO2, as a function of the pore former concentration. As can be seen, the porosity of the sample increases with the pore former concentration. When the pore former concentration was increased from 0 to 80 vol.%, the porosity of the sintered sample using Cr2O3 as sintering additive increased from 38.0 to 82.6% which is higher than that using TiO2 going from 28.9 to 79.3%. When the pore former excess 80 vol.%, the samples were collapsed after pore former elemination process whatever sintering additive was used. Figure 5 shows the compressive strength of the sintered samples as a function of pore former concentration. As expected, higher porosity of the sintered sample leads to a lower compressive strength. As TiO2 using as sintering additive, when the porosity increases from 29.8 to 78.3% corresponding to the pore former concentration going from 0 to 80%, the compressive strength drastically decreases from 368.5 to 1.4 MPa. On the other hand, the compressive strength of the sintered porous alumina using Cr2O3 as sintering additive also decreased from 99.6 to 0.9 MPa when the porosity increased from 38.0 to 82.6%. Fig. 4. Influence of the pore former concentration on the porosity of the porous alumina sintered at 1550oC for 4h using different sintering additives (a) (b) (a) (b) (c) Journal of Science & Technology 119 (2017) 071-075 75 Fig. 5. Influence of the pore former concentration on the compressive strength of the porous alumina sintered at 1550oC for 4h using different sintering additives The refractoriness of the porous alumina samples without and with different sintering additives were determined by Pyrometrics Cone Equivalent (PCE) test. PCE is measured by making a cone of the refractory and firing it until it bends and comparing it with the standard cone. The result showed that at the maximum temperature 1770oC of the equipment, no cones were bended, which indicated that the heat resistance of the samples are higher than 1770oC. 4. Conclusions Sintering additives Cr2O3 and TiO2 significantly enhanced the sinterability of alumina at 1550oC and improved the mechanical properties of the products, especially, in the case of TiO2. Porous alumina prepared by powder metallurgy using NH4HCO3 as pore former and TiO2 as sintering additive has lower porosity, smaller pore size and higher strength than that using Cr2O3. The porosity of the sintered porous alumina increased with the concentration of the pore former. However, the strength of the sample changed inversely with the porosity. The heat resistance of the sintered porous alumina are higher than 1770oC whatever sintering additives were used. Acknowledement The authors sincerely thank to Dr. DO Minh Duc for the generous help in testing mechanical strength. This research is funded by Hanoi University of Science and Technology (HUST) under project number T2016-PC-151. References [1] E.C. Hammel, O.L.-R. Ighodaro, O.I. Okoli, Processing and properties of advanced porous ceramics: An application based review, Ceram. Int. 40 (2014) 15351–15370. [2] I.Y. Guzman, Certain Principles of Formation of Porous Ceramic Structures. Properties and Applications (A Review), Glass Ceram. 60 (2003) 280–283. [3] D. Li, M. Li, Porous Y2SiO5 Ceramic with Low Thermal Conductivity, J. Mater. Sci. Technol. 28 (2012) 799–802. [4] A.R. Studart, U.T. Gonzenbach, E. Tervoort, L.J. Gauckler, Processing Routes to Macroporous Ceramics: A Review, J. Am. Ceram. Soc. 89 (2006) 1771–1789. [5] E. Chevalier, D. Chulia, C. Pouget, M. Viana, Fabrication of porous substrates: a review of processes using pore forming agents in the biomaterial field, J. Pharm. Sci. 97 (2008) 1135– 1154. [6] T. Ohji, M. Fukushima, Macro-porous ceramics: processing and properties, Int. Mater. Rev. 57 (2012) 115–131. [7] L.A. Xue, I.-W. Chen, Low-Temperature Sintering of Alumina with Liquid-Forming Additives, J. Am. Ceram. Soc. 74 (1991) 2011–2013. [8] I.B. Cutler, C. Bradshaw, C.J. Christensen, E.P. Hyatt, Sintering of Alumina at Temperatures of 1400°C and Below, J. Am. Ceram. Soc. 40 (1957) 134–139. [9] Seung-Am Cho, F.J. Arenas, J. Ochoa, Densification and hardness of Al2O3-Cr2O3 system with and without Ti addition, Ceram. Int. (1990) 301- 309. [10] R. D. Bagley, I.B. Cutler and D. L. Johnson, Effect of TiO2 on Initial Sintering of Al2O3, J. Am. Ceram. Soc. 53 (1970) 136–141. [11] J.J. Kanga, B.S.Xub, H.D. Wang, C.B. Wanga, Influence of Spraying Parameters on the Microstructure and Properties of Plasma-sprayed Al2O3/40%TiO2 Coating, Physics Procedia Vol. 50 (2013) 169–176. [12] K.Q. Dang and M. Nanko, Effects of pressure and temperature on sintering of Cr-doped Al2O3 by pulsed electric current sintering process, IOP Conf. Series: Mater. Sci. and Eng. 20 (2011) 012004 [13] A. Azarniya , A. Azarniya, H. R. Hosseinia, Abdolreza Simchib, Mechanical and thermal properties of highly porous Al2TiO5–Mullite ceramics, Ceram. Int., Vol. 42, Issue 2, Part B (2016) 3548–3555.
File đính kèm:
influence_of_sintering_additives_on_the_porous_structure_and.pdf