Hydrodynamic studies on liquid-Liquid two phase flow separation in microchannel by computational fluid dynamic modelling
Microfluidic systems undergo rapid expansion of its application in different industries over the
few decades as its surface tension-dominated property provides better mixing and improves mass
transfer between two immiscible liquids. Synthesis of biodiesel via transesterification of vegetable
oil and methanol in microfluidic systems by droplet flow requires separation of the products after
the reaction occurred. The separation technique for multiphase fluid flow in the microfluidic system
is different from the macro-system, as the gravitational force is overtaken by surface force. To understand these phenomena completely, a study on the hydrodynamic characteristics of two-phase
oil-methanol system in microchannel was carried out. A multiphase Volume of Fluid model was
developed to predict the fluid flow in the microchannel. An inline separator design was proposed
along with its variable to obtain effective separation for the oil-methanol system. The separation
performance was evaluated based on the amount of oil recovered and its purity. The capability
of the developed model has been validated through a comparison of simulation results with published experiment. It was predicted that the purity of recovered oil was increased by more than
46% when the design with side openings arranged at both sides of the microchannel. The highest percentage recovery of oil from the mixture was simulated at 91.3% by adding the number of
side openings to ensure the maximum recovery. The oil that was separated by the inline separator
was predicted to be at 100% purity, which indicates that no methanol contamination throughout
the separation process. The purity of the separated product can be increased by manipulating the
pressure drop across the side openings. Hence, it can be concluded that the separation in a large
diameter microchannel system is possible and methodology can be tuned to achieve the separation goal. Finally, the simulation results showed that the present volume of fluid model had a good
agreement with the published experiment.
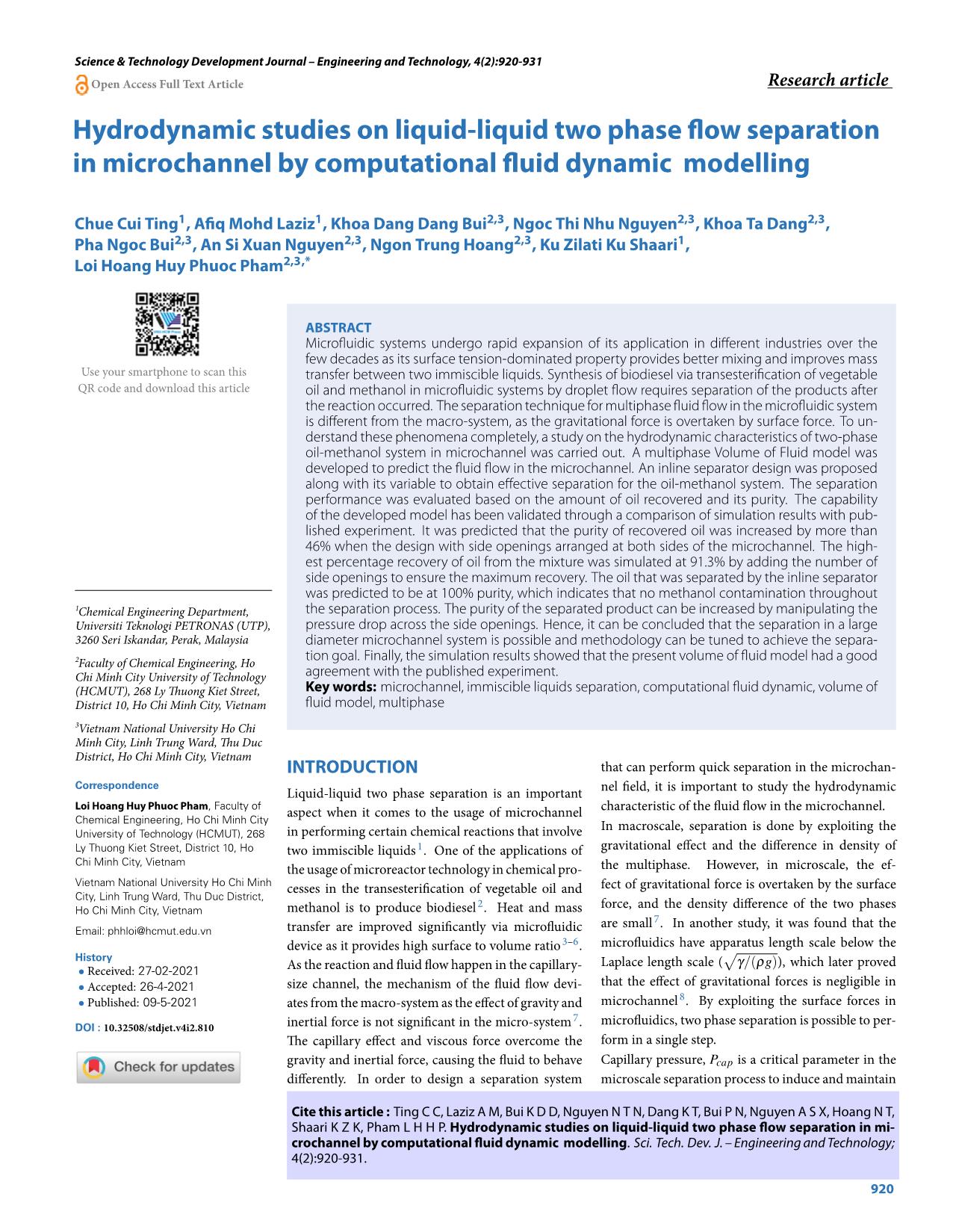
Trang 1
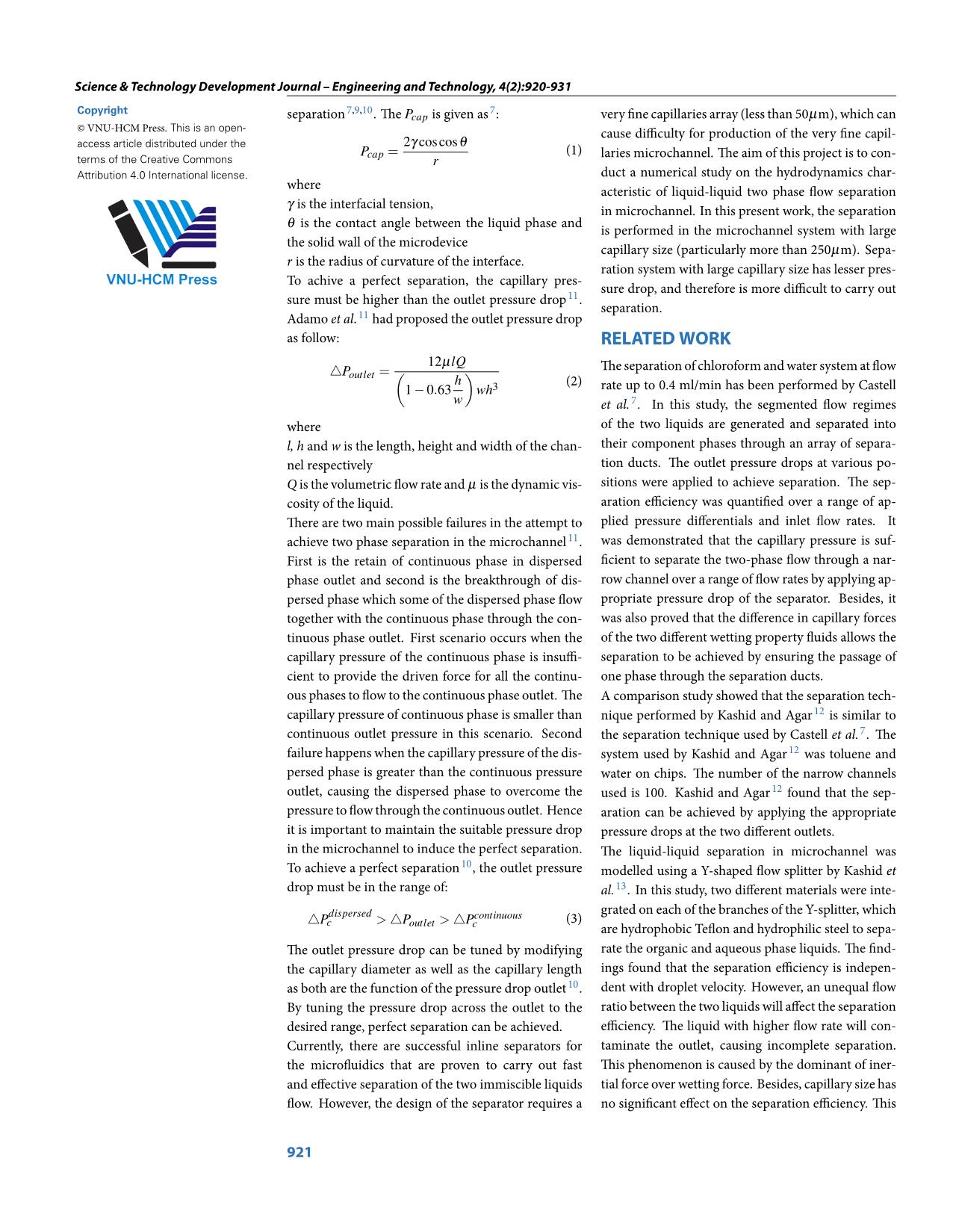
Trang 2
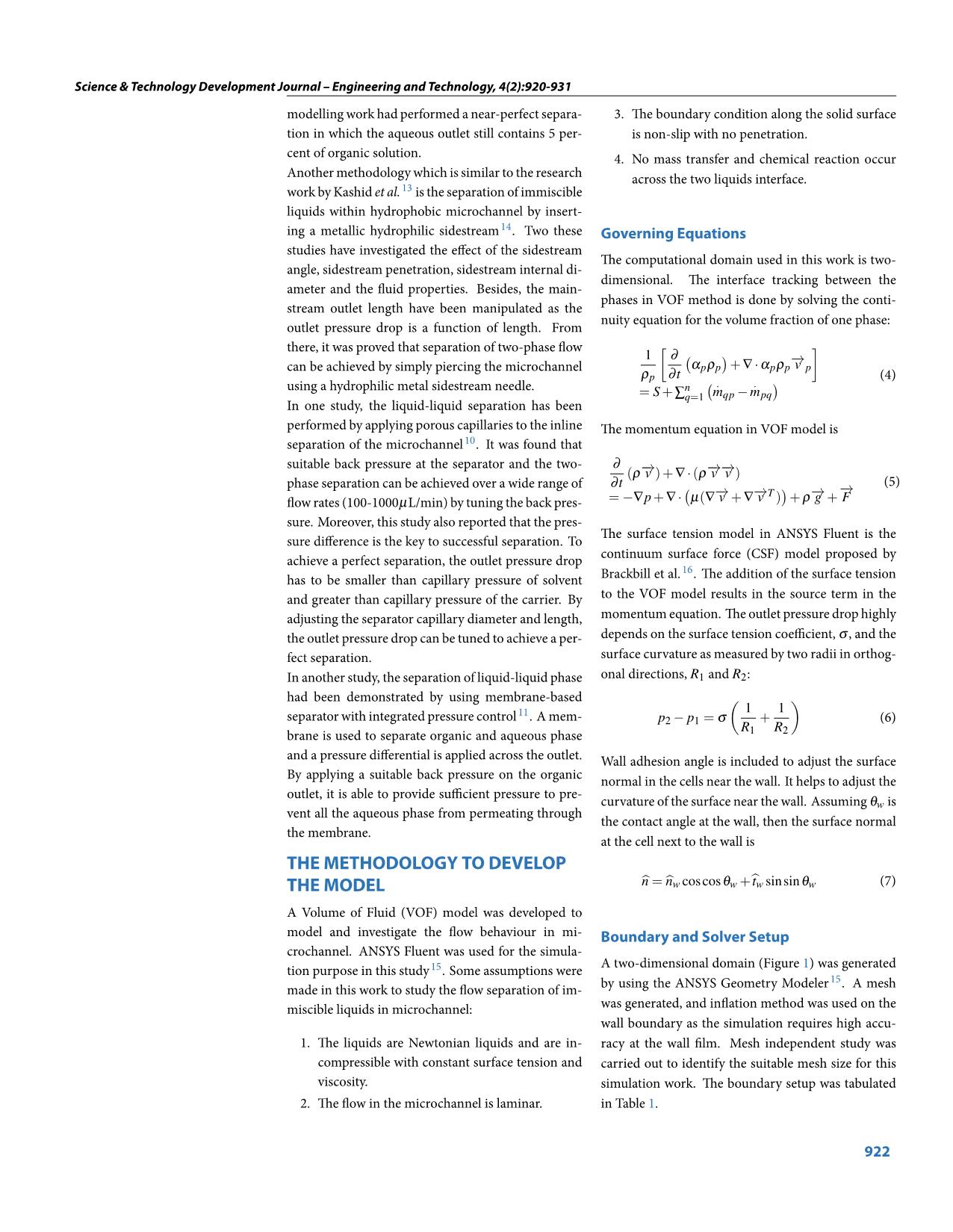
Trang 3
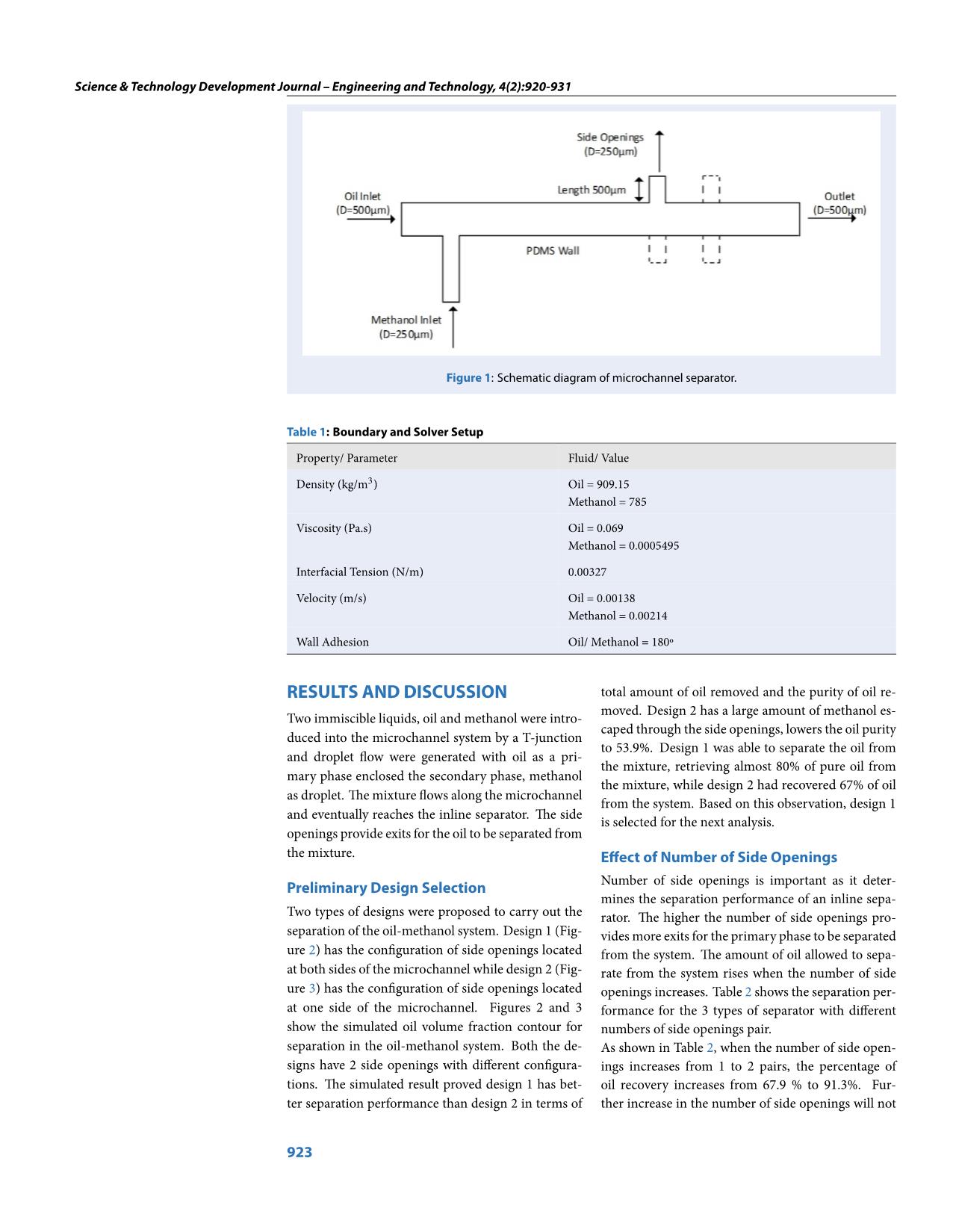
Trang 4
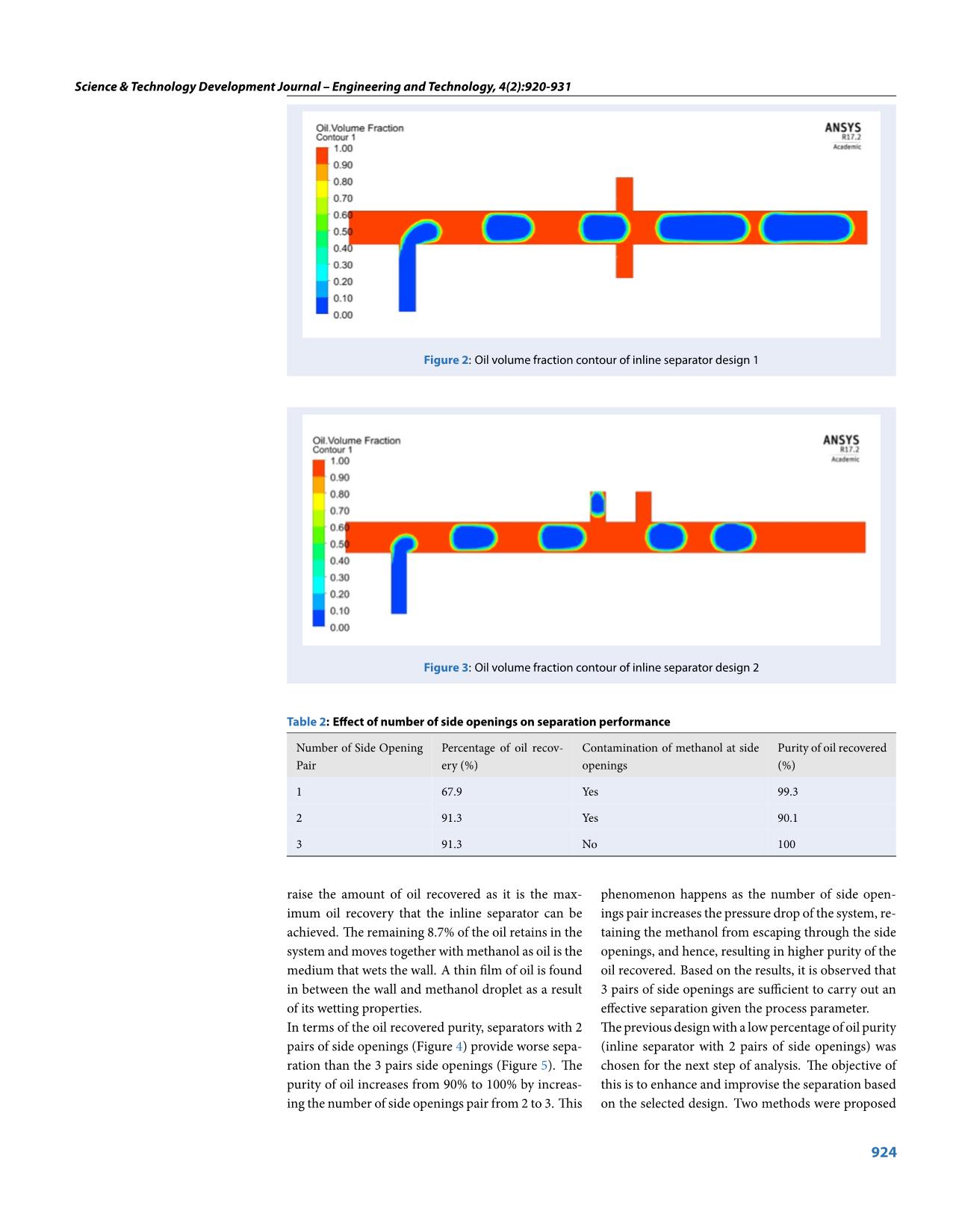
Trang 5
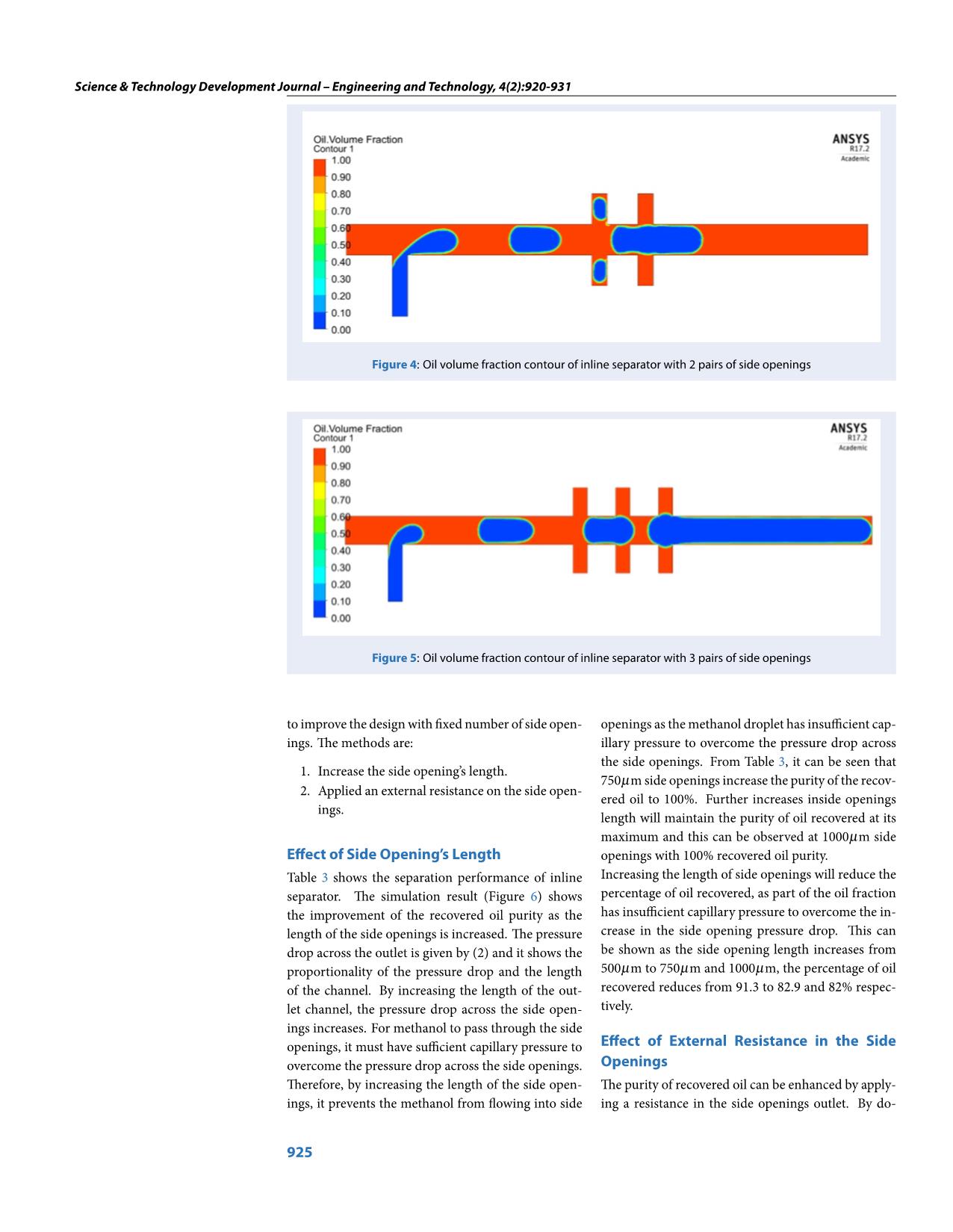
Trang 6
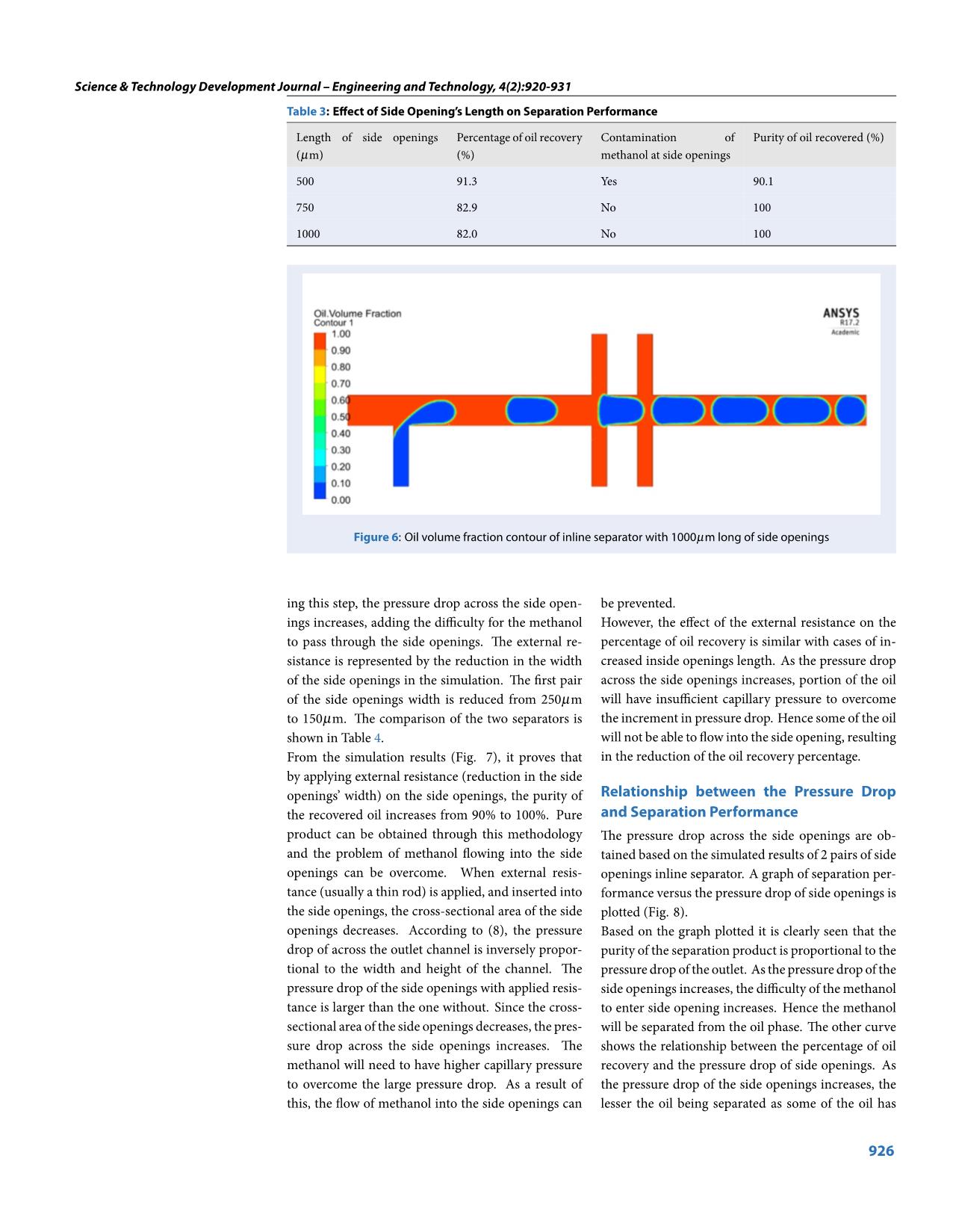
Trang 7
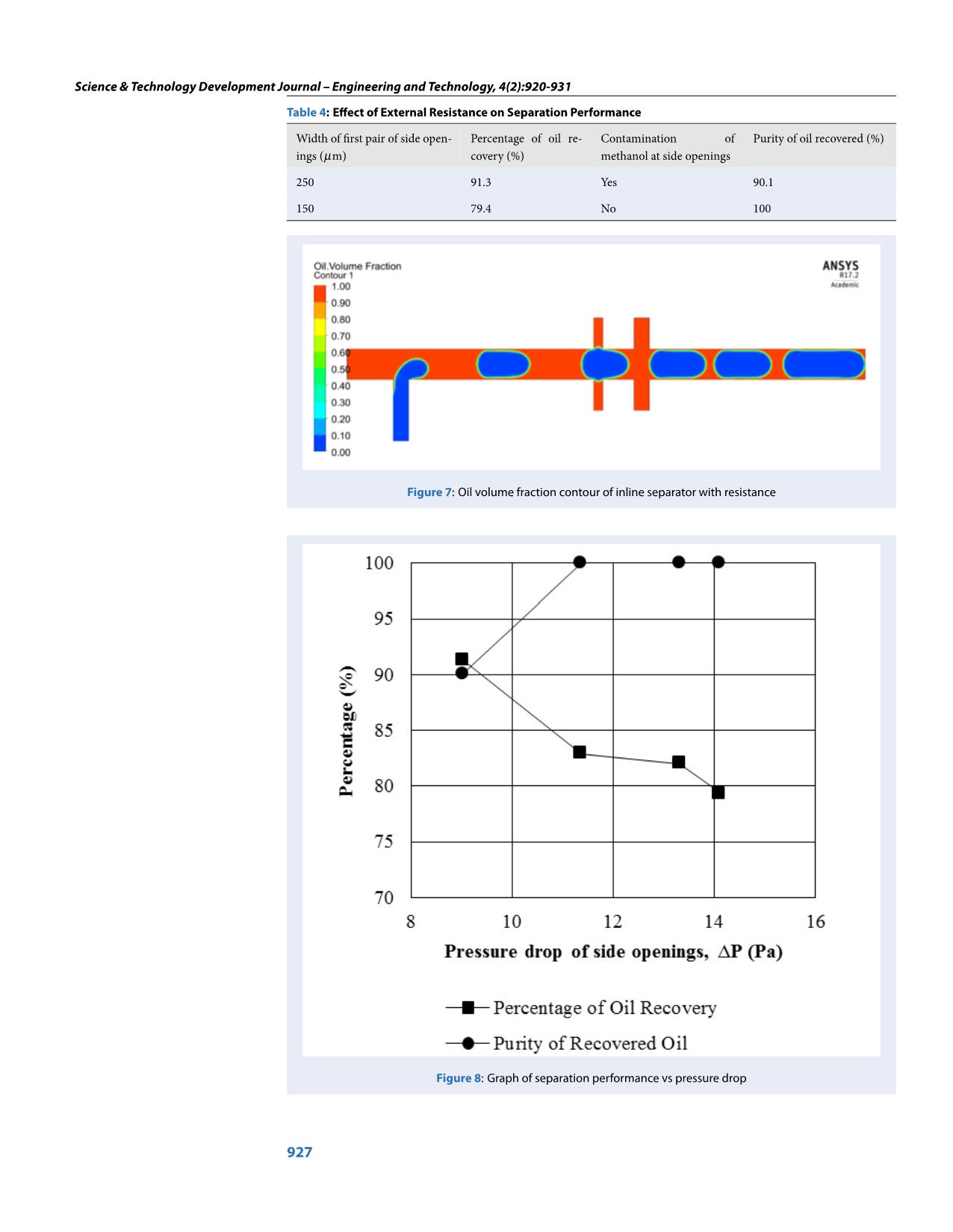
Trang 8

Trang 9
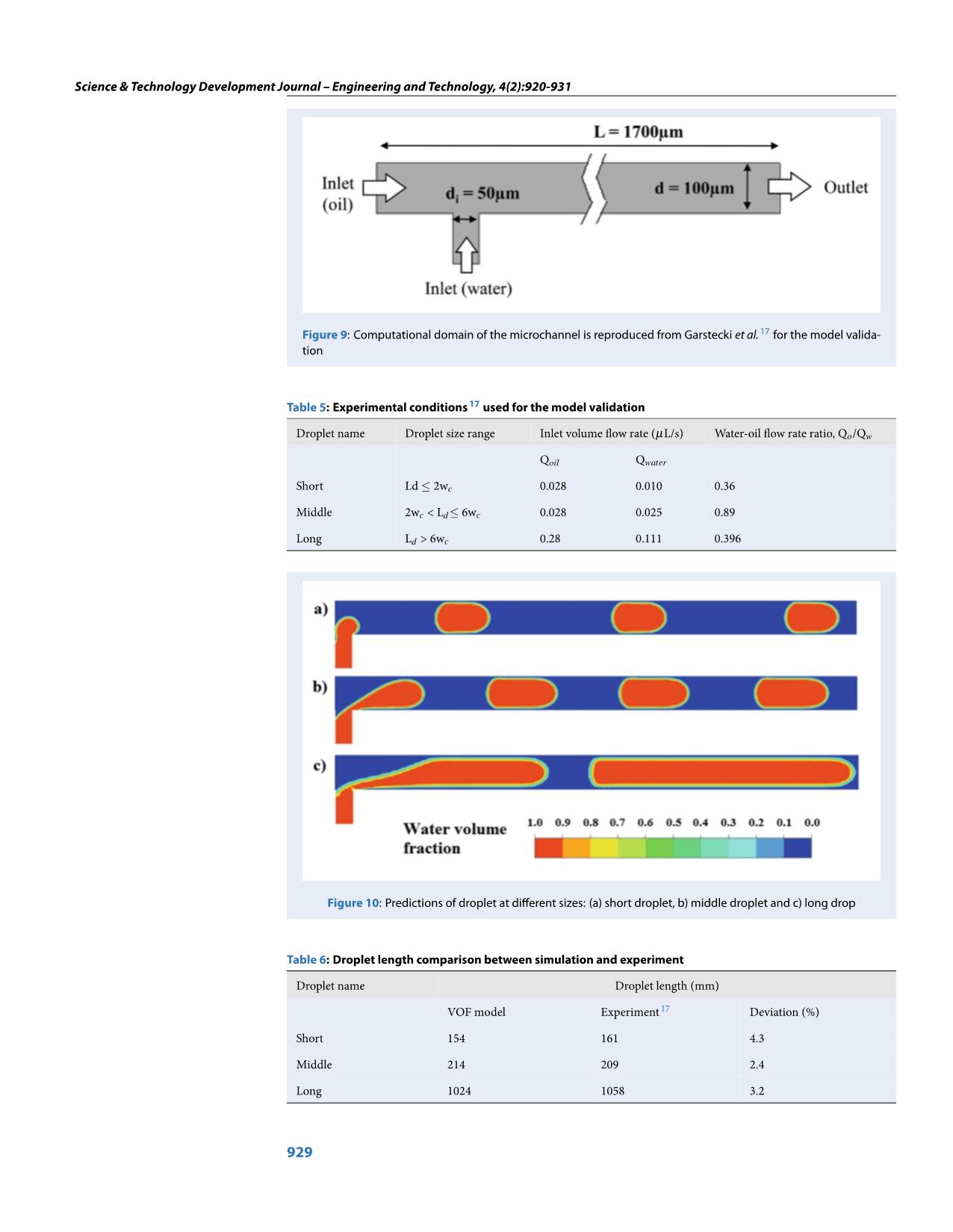
Trang 10
Tải về để xem bản đầy đủ
Tóm tắt nội dung tài liệu: Hydrodynamic studies on liquid-Liquid two phase flow separation in microchannel by computational fluid dynamic modelling
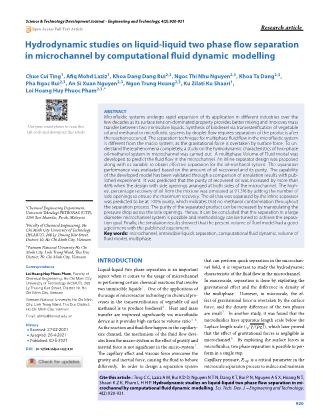
Science & Technology Development Journal – Engineering and Technology, 4(2):920-931 Open Access Full Text Article Research article 1Chemical Engineering Department, Universiti Teknologi PETRONAS (UTP), 3260 Seri Iskandar, Perak, Malaysia 2Faculty of Chemical Engineering, Ho Chi Minh City University of Technology (HCMUT), 268 Ly Thuong Kiet Street, District 10, Ho Chi Minh City, Vietnam 3Vietnam National University Ho Chi Minh City, Linh Trung Ward, Thu Duc District, Ho Chi Minh City, Vietnam Correspondence Loi Hoang Huy Phuoc Pham, Faculty of Chemical Engineering, Ho Chi Minh City University of Technology (HCMUT), 268 Ly Thuong Kiet Street, District 10, Ho Chi Minh City, Vietnam Vietnam National University Ho Chi Minh City, Linh Trung Ward, Thu Duc District, Ho Chi Minh City, Vietnam Email: phhloi@hcmut.edu.vn History Received: 27-02-2021 Accepted: 26-4-2021 Published: 09-5-2021 DOI : 10.32508/stdjet.v4i2.810 Hydrodynamic studies on liquid-liquid two phase flow separation inmicrochannel by computational fluid dynamic modelling Chue Cui Ting1, AfiqMohd Laziz1, Khoa Dang Dang Bui2,3, Ngoc Thi Nhu Nguyen2,3, Khoa Ta Dang2,3, Pha Ngoc Bui2,3, An Si Xuan Nguyen2,3, Ngon Trung Hoang2,3, Ku Zilati Ku Shaari1, Loi Hoang Huy Phuoc Pham2,3,* Use your smartphone to scan this QR code and download this article ABSTRACT Microfluidic systems undergo rapid expansion of its application in different industries over the few decades as its surface tension-dominated property provides better mixing and improves mass transfer between two immiscible liquids. Synthesis of biodiesel via transesterification of vegetable oil and methanol in microfluidic systems by droplet flow requires separation of the products after the reaction occurred. The separation technique formultiphase fluid flow in themicrofluidic system is different from the macro-system, as the gravitational force is overtaken by surface force. To un- derstand these phenomena completely, a study on the hydrodynamic characteristics of two-phase oil-methanol system in microchannel was carried out. A multiphase Volume of Fluid model was developed to predict the fluid flow in the microchannel. An inline separator design was proposed along with its variable to obtain effective separation for the oil-methanol system. The separation performance was evaluated based on the amount of oil recovered and its purity. The capability of the developed model has been validated through a comparison of simulation results with pub- lished experiment. It was predicted that the purity of recovered oil was increased by more than 46% when the design with side openings arranged at both sides of the microchannel. The high- est percentage recovery of oil from the mixture was simulated at 91.3% by adding the number of side openings to ensure the maximum recovery. The oil that was separated by the inline separator was predicted to be at 100% purity, which indicates that no methanol contamination throughout the separation process. The purity of the separated product can be increased by manipulating the pressure drop across the side openings. Hence, it can be concluded that the separation in a large diameter microchannel system is possible and methodology can be tuned to achieve the separa- tion goal. Finally, the simulation results showed that the present volume of fluid model had a good agreement with the published experiment. Keywords: microchannel, immiscible liquids separation, computational fluid dynamic, volume of fluid model, multiphase INTRODUCTION Liquid-liquid two phase separation is an important aspect when it comes to the usage of microchannel in performing certain chemical reactions that involve two immiscible liquids1. One of the applications of the usage ofmicroreactor technology in chemical pro- cesses in the transesterification of vegetable oil and methanol is to produce biodiesel2. Heat and mass transfer are improved significantly via microfluidic device as it provides high surface to volume ratio 3–6. As the reaction and fluid flow happen in the capillary- size channel, the mechanism of the fluid flow devi- ates from themacro-system as the effect of gravity and inertial force is not significant in the micro-system7. The capillary effect and viscous force overcome the gravity and inertial force, causing the fluid to behave differently. In order to design a separation system that can perform quick separation in the microchan- nel field, it is important to study the hydrodynamic characteristic of the fluid flow in the microchannel. In macroscale, separation is done by exploiting the gravitational effect and the difference in density of the multiphase. However, in microscale, the ef- fect of gravitational force is overtaken by the surface force, and the density difference of the two phases are small7. In another study, it was found that the microfluidics have apparatus length scale below the Laplace length scale ( p g=(rg)), which later proved that the effect of gravitational forces is negligible in microchannel8. By exploiting the surface forces in microfluidics, two phase separation is possible to per- form in a single step. Capillary pressure, Pcap is a critical parameter in the microscale separation process to induce andmaintain Cite this article : Ting C C, Laziz AM, Bui K D D, Nguyen N T N, Dang K T, Bui P N, Nguyen A S X, Hoang N T, Shaari K Z K, Pham L H H P. Hydrodynamic studies on liquid-liquid two phase flow separation in mi- crochannel by computational fluid dynamic modelling. Sci. Tech. Dev. J. – Engineering and Technology; 4(2):920-931. 920 Copyright © VNU-HCM Press. This is an open- access article distributed under the terms of the Creative Commons Attribution 4.0 International license. Science & Technology Development Journal – Engineering and Technology, 4(2):920-931 separation7,9,10. The Pcap is given as7: Pcap = 2g coscosq r (1) where ... gy Development Journal – Engineering and Technology, 4(2):920-931 not sufficient pressure to enter the side openings. Less oil is being recovered from the system as it retains in the main outlet and to be discharged together with methanol. The finding shows the significance of the pressure drop across the side openings in achieving microchannel inline separation. Model Validation Study In this study, the experimental result from Garstecki et al.17 is used to validate the accuracy of the above VOF model. The geometry of the microchannel used in Garstecki et al.’s experiment is a T-junction as shown in Fig. 9. The diameter of microchannel is 100 mm and the inlet has a width of 50 mm. Oil is used as the continuous phase and water as dispersed phase. The main purpose of Garstecki et al.’s experiment17 is to produce different droplet sizes by injecting var- ious volumetric flow rate ratio between oil and water into T-junctionmicrochannel. Three different droplet sizes have been observed in range of the ratio between the droplet length, Ld , to the channel width, wc. Ta- ble 5 shows the details of experimental conditions for all droplet size scenarios. Fig. 10 shows the simulation results of the droplet predicted from the VOF model at different volumet- ric flow conditions (see Table 5). It can be found in the Fig. 10 that increasing the oil-to-water ratio leads to the increase of the droplet size. This finding is in corresponding with the study of Garstecki et al.17. The droplet lengths predicted from the VOF model and observed from the experiment17 are presented in Table 6. As can be seen from Table 6, the length de- viations between the simulation and experimental re- sults are around 5%. This finding revealed that good agreement was observed between the simulation re- sults and the published experimental data. CONCLUSION The flow behaviour of two immiscible liquids in mi- crochannel is studied using the VOF model that is available in ANSYS Fluent software. Separation of two immiscible liquids in the microchannel by us- ing a large diameter inline separator system is pro- posed at the earlier stage of the project. By conducting this study, this project proves that inline separation by large diameter separator is possible. The project is done by using the squeezing regime at the inlet flow, with the velocity of oil phase at 0.00138 m/s and velocity of methanol phase at 0.00214 m/s, which bring difficulties for the separation as the two fluids are flowing at a very slow velocity. Themain in- terest of this project is to recover the oil from themix- ture, as the oil phase is the main product of the trans- esterification. Therefore, the separation performance will be evaluated based on the recovered oil product. Preliminary study is conducted to identify the suit- able design for the inline separator. It is proven that the design with side openings arranged at both sides of the microchannel gives better separation perfor- mance than the design with side openings arranged at one side of the microchannel. The purity of recov- ered oil is increased by more than 46%. Based on this observation, the project is continuedwith selected de- sign. Further analysis is carried out on the selected geom- etry to investigate the effect of number of side open- ings, effect of side openings’ length and effect of exter- nal resistance on the separation performance of the inline separator. It is observed that the highest per- centage recovery of oil from the mixture that can be achieved is 91.3%. This method can be achieved by adding the number of side openings to ensure the maximum recovery. The oil that is separated by the inline separator is found to be at 100% purity, which indicates that no methanol contamination through- out the separation process. For the cases where the contamination of methanol occurred, whereby the methanol is escaping into the side openings together with the oil phase, this prob- lem can be overcome by applying larger pressure drop across the side openings. This methodology can be achieved by increasing the length of the side openings, or by applying external resistance in the side open- ings. The purity of the recovered oil is proved to be increased up to 100%, whereby all the methanol will flow through the main outlet. The project has demonstrated that the separation of oil-methanol system inmicrochannel can be achieved using a higher number of side openings, which is 3 pairs of side openings for the selected oil and methanol flow rate. The purity of the separated prod- uct can be increased by manipulating the pressure drop across the side openings. Hence, it can be con- cluded that the separation in a large diameter mi- crochannel system is possible and methodology can be tuned to achieve the separation goal. Finally, the developed VOF model was validated against a recently published experimental data. The validation study shows that the present VOF model had a good agreement with the published experiment. ACKNOWLEDGEMENTS We acknowledge the support of time and facili- ties from Ho Chi Minh City University of Technol- ogy (HCMUT), VNU-HCMandUniversiti Teknologi PETRONAS (UTP) for this study. 928 Science & Technology Development Journal – Engineering and Technology, 4(2):920-931 Figure 9: Computational domain of the microchannel is reproduced from Garstecki et al. 17 for the model valida- tion Table 5: Experimental conditions 17 used for themodel validation Droplet name Droplet size range Inlet volume flow rate (mL/s) Water-oil flow rate ratio, Qo/Qw Qoil Qwater Short Ld 2wc 0.028 0.010 0.36 Middle 2wc < Ld 6wc 0.028 0.025 0.89 Long Ld > 6wc 0.28 0.111 0.396 Figure 10: Predictions of droplet at different sizes: (a) short droplet, b) middle droplet and c) long drop Table 6: Droplet length comparison between simulation and experiment Droplet name Droplet length (mm) VOF model Experiment 17 Deviation (%) Short 154 161 4.3 Middle 214 209 2.4 Long 1024 1058 3.2 929 Science & Technology Development Journal – Engineering and Technology, 4(2):920-931 LIST OF ABBREVIATION CSF Continuum surface force PTFE Polytetrafluoroethylene VOF Volume of Fluid COMPETING INTERESTS The authors declare that they have no conflicts of in- terests. AUTHORS’ CONTRIBUTIONS The research methodology was conceptually pro- posed by Chue Cui Ting and Afiq Mohd Laziz. Orig- inal draft was prepared by Chue Cui Ting. The re- search was supervised by Khoa Dang Dang Bui, Ngoc Thi Nhu Nguyen, Khoa Ta Dang Pha, Ngoc Bui, An Si Xuan Nguyen, Ngon Trung Hoang, Ku Zilati Ku Shaari and Loi Hoang Huy Phuoc Pham. All authors have read and agreed to the published version of the manuscript. REFERENCES 1. Okubo Y, et al. Microchannel devices for the coalescence of dispersed droplets produced for use in rapid extraction pro- cesses. Chemical Engineering Journal. 2004;101(1-3):39–48. Available from: https://doi.org/10.1016/j.cej.2003.10.025. 2. Canter N. Making biodiesel in a microreactor. Tribol. Lubr. Technol. 2006;62:15–17. 3. EhrfeldW, Hessel V, Loewe H. Microreactors: New Technology for Modern Chemistry. Wiley-VCH, Weinheim. 2000;Available from: https://doi.org/10.1002/3527601953. 4. Kobayashi J, Mori Y, Kobayashi S. Multiphase organic syn- thesis in microchannel reactors. Chem. Asian J. 2006;1:22–35. PMID: 17441035. Available from: https://doi.org/10.1002/asia. 200600058. 5. Jovanovic J, Rebrov EV. Phase transfer catalysis in segmented flow in a microchannel: fluidic control of selectivity and pro- ductivity. Ind. Eng. Chem. Res. 2010;49:2681–2687. Available from: https://doi.org/10.1021/ie9017918. 6. Kashid MN, Renken A, Kiwi-Minsker L. CFD modelling of liquid-liquid multiphase microstructured reactor: Slug flow generation. Chemical Engineering Research and Design. 2010;88(3):362–368. Available from: https://doi.org/10.1016/j. cherd.2009.11.017. 7. Castell OK. Liquid-liquid phase separation: Characterisation of a novel device capable of separating particle carrying mul- tiphase flows. Lab Chip. 2009;9:388–396. PMID: 19156287. Available from: https://doi.org/10.1039/B806946H. 8. Gunther A, Jensen KF. Multiphase microuidics: from ow char- acteristics to chemical and materials synthesis. Lab on a Chip. 2006;6:1487–1503. PMID: 17203152. Available from: https: //doi.org/10.1039/B609851G. 9. Kralj J, Sahoo H, Jensen K. Integrated continuous microfluidic liquid-liquid extraction. Lab Chip. 2007;7(2):256–263. PMID: 17268629. Available from: https://doi.org/10.1039/B610888A. 10. Phillips TW, et al. Microscale extraction and phase sepa- ration using a porous capillary. Lab Chip. 2015;15(14):2960– 2967. PMID: 26054926. Available from: https://doi.org/10. 1039/C5LC00430F. 11. Adamo A, Heider PL, et al. Membrane-Based, Liquid- Liquid Separatorwith IntegratedPressureControl. Industrial & Engineering Chemistry Research. 2013;52(31):10802–10808. Available from: https://doi.org/10.1021/ie401180t. 12. Kashid MN, Agar DW. Hydrodynamics of liquid-liquid slug flow capillary microreactor: flow regimes, slug size and pres- sure drop. Chemical Engineering Journal. 2007;131(1):1–13. Available from: https://doi.org/10.1016/j.cej.2006.11.020. 13. Kashid MN, et al. Liquid Liquid Slug Flow In A Capillary: An Alternative To Suspended Drop Or Film Contactors. Industrial & Engineering Chemistry Research. 2007;46(25):8420–8430. Available from: https://doi.org/10.1021/ie070077x. 14. Scheiff F, et al. The separationof immiscible liquid slugswithin plasticmicrochannels using ametallic hydrophilic sidestream. Lab on a Chip. 2011;11(6):1022–1029. PMID: 21279200. Avail- able from: https://doi.org/10.1039/c0lc00442a. 15. Fluent. FLUENT 6.3 User’s Guide. Fluent Inc. 2006;. 16. Brackbill JU, et al. A ContinuumMethod for Modeling Surface Tension. J. Comput. Phys. 1992;100:335–354. Available from: https://doi.org/10.1016/0021-9991(92)90240-Y. 17. Garstecki P. Formation of droplets and bubbles in a microflu- idic T-junction-scaling and mechanism of break-up. Lab Chip. 2006;6:437–446. PMID: 16511628. Available from: https: //doi.org/10.1039/b510841a. 930 Tạp chí Phát triển Khoa học và Công nghệ – Kĩ thuật và Công nghệ, 4(2): 920-931 Open Access Full Text Article Bài nghiên cứu 1Khoa Kỹ thuật Hóa học, Trường Đại học Kỹ thuật Petronas, 3260 Seri Iskandar, Perak, Malaixia 2Khoa Kỹ thuật Hóa học, Trường Đại học Bách Khoa TP. Hồ Chí Minh, 268 Lý Thường Kiệt, Quận 10, Thành phố Hồ Chí Minh, Việt Nam 3Đại học Quốc gia Thành phố Hồ Chi Minh, Phường Linh Trung, QuậnThủ Đức, Thành phố Hồ Chi Minh, Việt Nam Liên hệ PhạmHoàng Huy Phước Lợi, Khoa Kỹ thuật Hóa học, Trường Đại học Bách Khoa TP. Hồ Chí Minh, 268 Lý Thường Kiệt, Quận 10, Thành phố Hồ Chí Minh, Việt Nam Đại học Quốc gia Thành phố Hồ Chi Minh, Phường Linh Trung, Quận Thủ Đức, Thành phố Hồ Chi Minh, Việt Nam Email: phhloi@hcmut.edu.vn Lịch sử Ngày nhận: 27-02-2021 Ngày chấp nhận: 26-4-2021 Ngày đăng: 09-5-2021 DOI : 10.32508/stdjet.v4i2.810 Nghiên cứu về thủy động lực học của sự phân tách dòng chảy giữa hai pha lỏng-lỏng trong vi kênh bằngmô hình tính toán động lực học chất lưu Chue Cui Ting1, AfiqMohd Laziz1, Bùi Đặng Đăng Khoa2,3, Nguyễn Thị Như Ngọc2,3, Tạ Đăng Khoa2,3, Bùi Ngọc Pha2,3, Nguyễn Sĩ Xuân Ân2,3, Hoàng Trung Ngôn2,3, Ku Zilati Ku Shaari1, PhạmHoàng Huy Phước Lợi2,3,* Use your smartphone to scan this QR code and download this article TÓM TẮT Trong những thập niên gần đây, hệ thống vi lưu được dùng nhiều trong các ngành công nghiệp khác nhau, vì nhờ đặc tính sức căng bề mặt của nó đã giúp cho sự hòa trộn tốt hơn và tăng sự truyền khối giữa hai chất lỏng không hòa tan. Quá trình tổng hợp diesel sinh học thông qua phản ứng tổng hợp este của dầu thực vật và methanol trong hệ thống vi lưu nhỏ giọt yêu cầu tách các sản phẩm sau khi phản ứng xảy ra. Kỹ thuật tách dòng chất lỏng nhiều pha trong hệ thống vi lưu khác với hệ vĩ mô, do lực hấp dẫn bị lực bề mặt chi phối. Để hiểu rõ hiện tượng này, nghiên cứu về đặc điểm thủy động lực học của hệ thống dầu-methanol trong vi kênh đã được thực hiện. Mô hình thể tích chất lỏng nhiều pha đã được phát triển để dự đoán dòng chất lỏng trong vi kênh. Một bộ tách nội tuyến đã được thiết kế cùng với biến số của nó để có được sự phân tách hiệu quả cho hệ thống dầu-methanol. Hiệu suất của quá trình phân tách đã được đánh giá dựa trên lượng dầu thu hồi và độ tinh khiết của nó. Độ chính xác của mô hình đã phát triển đã được xác nhận thông qua việc so sánh kết quả mô phỏng với số liệu thực nghiệm đã công bố. Độ tinh khiết của dầu thu hồi đã được dự đoán tăng hơn 46% khi thiết kế với các lỗ ra được bố trí ở cả hai bên của vi kênh. Tỷ lệ phần trăm thu hồi cao nhất của dầu từ hỗn hợp được mô phỏng ở mức 91,3% bằng cách tăng số lượng lỗ ra ở hai bên để đảm bảo thu hồi tối đa. Dầu được tách bằng thiết bị tách nội tuyến được dự đoán là có độ tinh khiết 100%, điều này cho thấy rằng không có nhiễm methanol trong suốt quá trình tách. Độ tinh khiết của sản phẩm tách có thể được tăng lên bằng cách điều chỉnh độ giảm áp suất trên các lỗ ra. Do đó, có thể kết luận rằng việc phân tách trong một hệ thống vi kênh có đường kính lớn là có thể thực hiện được và phương pháp này có thể được điều chỉnh để đạt được mục tiêu phân tách. Cuối cùng, kết quả mô phỏng cho thấy mô hình thể tích chất lỏng này phù hợp với thí nghiệm đã công bố. Từ khoá: vi kênh, tách chất lỏng không hòa tan nhau, tính toán động lực học chất lưu, mô hình thể tích chất lỏng, nhiều pha Trích dẫn bài báo này: Ting C C, Laziz A M, Khoa B D D, Ngọc N T N, Khoa T D, Pha B N, Ân N S X, Ngôn H T, Shaari K Z K, Lợi P H H P. Nghiên cứu về thủy động lực học của sự phân tách dòng chảy giữa hai pha lỏng-lỏng trong vi kênh bằng mô hình tính toán động lực học chất lưu. Sci. Tech. Dev. J. - Eng. Tech.; 4(2): 920-931. 931
File đính kèm:
hydrodynamic_studies_on_liquid_liquid_two_phase_flow_separat.pdf