Fabrication of Sub-Micro Thin Layer Structures using Cyclopentanone Mix Solution as a Modified SU-8 3050
The SU-8 3000 series have been formulated for improved adhesion to the substrate and reduced coating
stress than SU-8 2000 series. It is being used to fabricate microstructures in the range of thickness from
some up to several hundred micrometers. However, it is hard to fabricate the layer of the SU-8 3000 series
at sub-micrometer thinness. In this paper, we propose a procedure to reduce the thickness of the SU-8 3050
thin film. By mixing the SU-8 3050 with Cyclopentanone (CP) with different volume ratios, we can control
viscosity of the mixture. Therefore, the thickness of the fabricated photoresist layer at 2000 rpm spincoating
can be from 540 nm to 5330 nm. The mixing procedures of SU-8 fabrication have been optimized in order to
enhance the unity of the thin layer photoresist. Some other fabrication factors are also investigated.
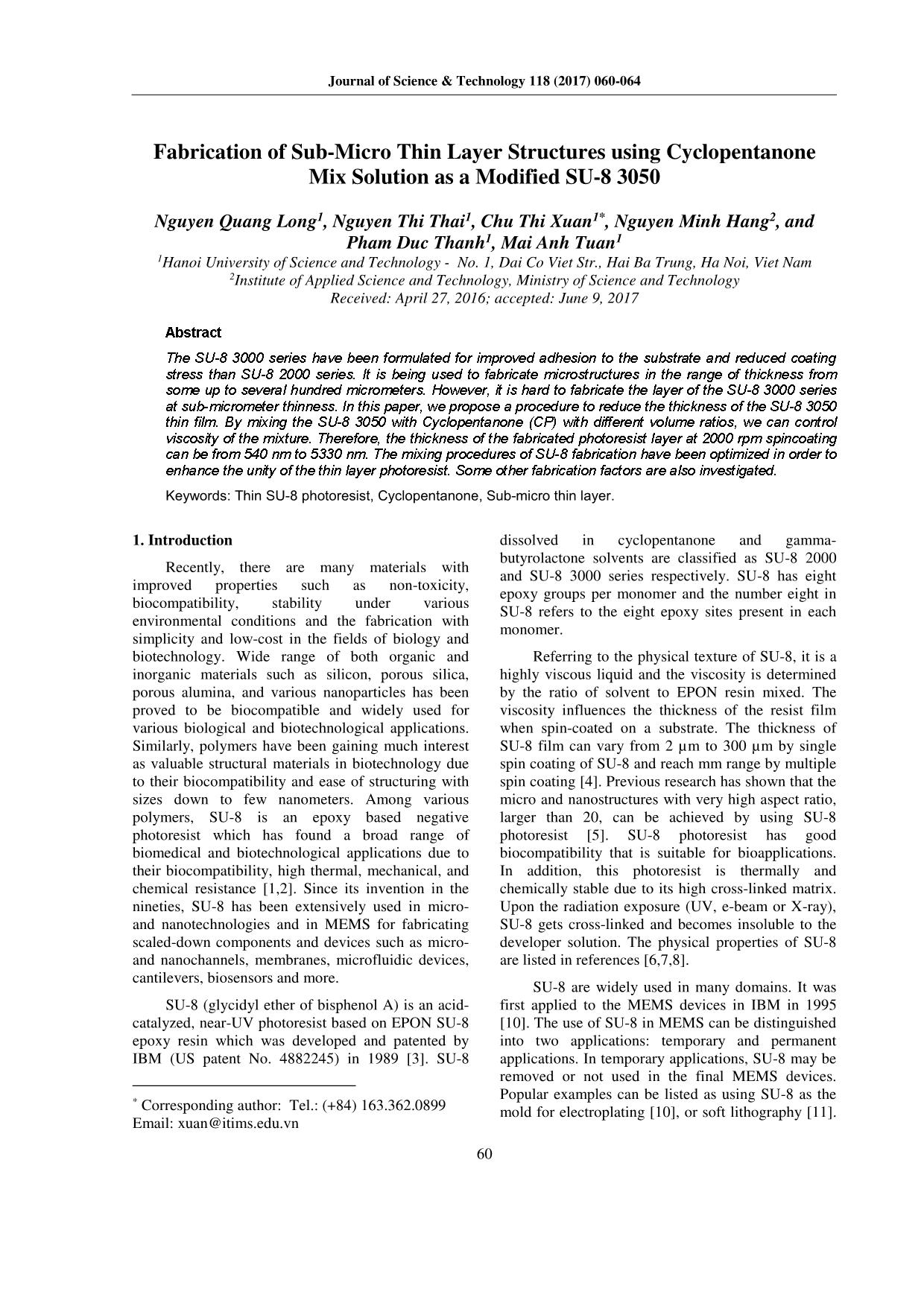
Trang 1
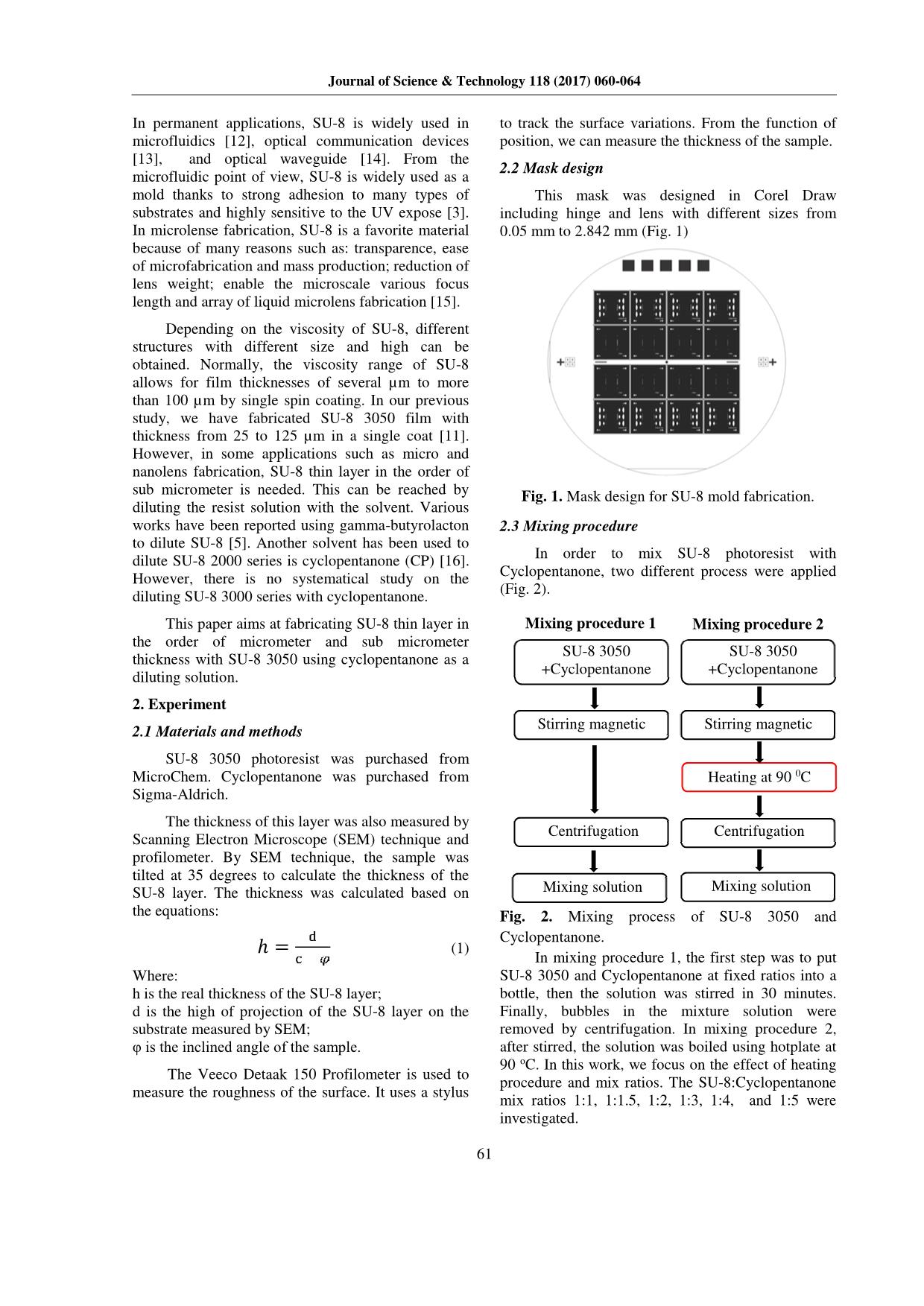
Trang 2
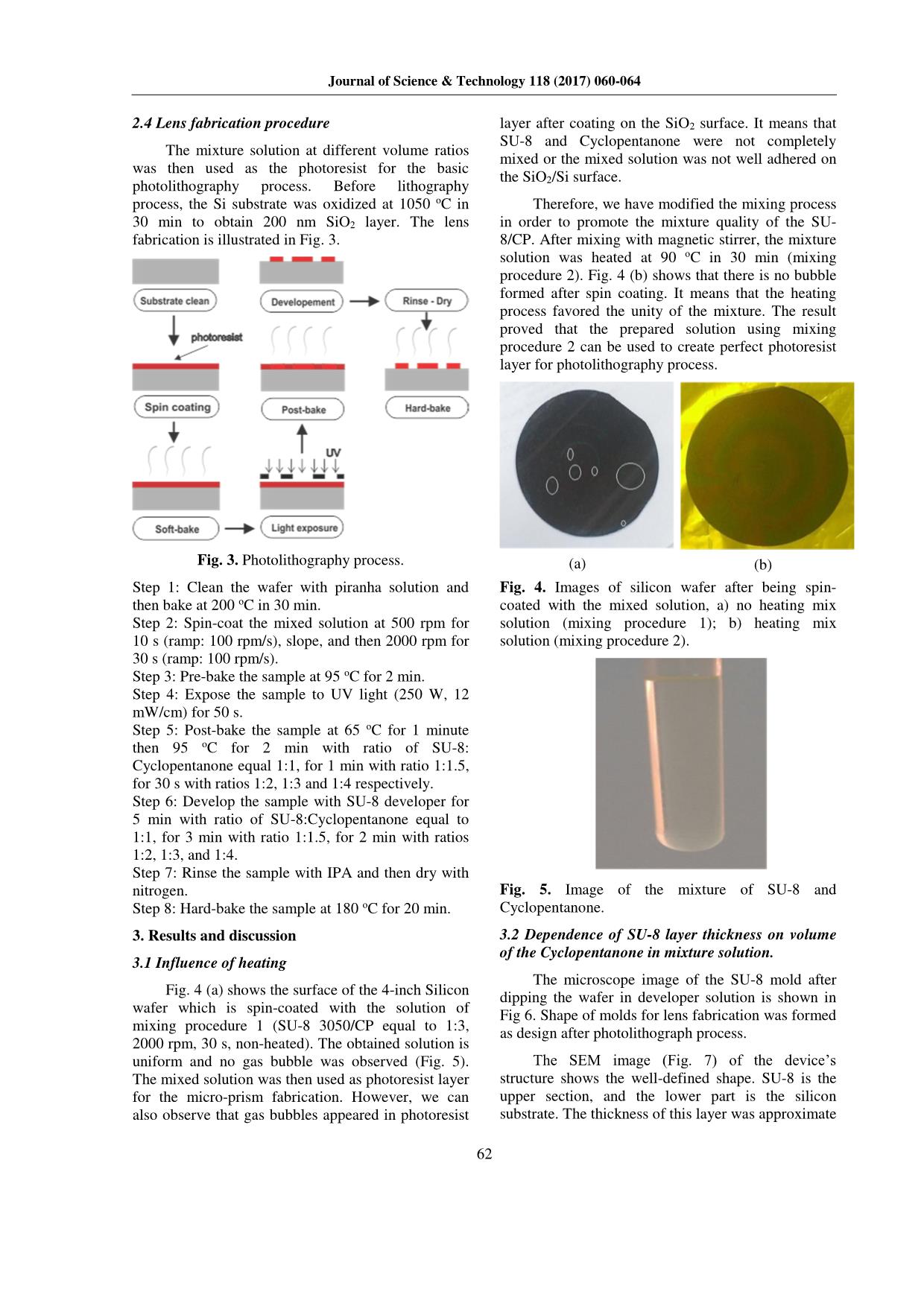
Trang 3
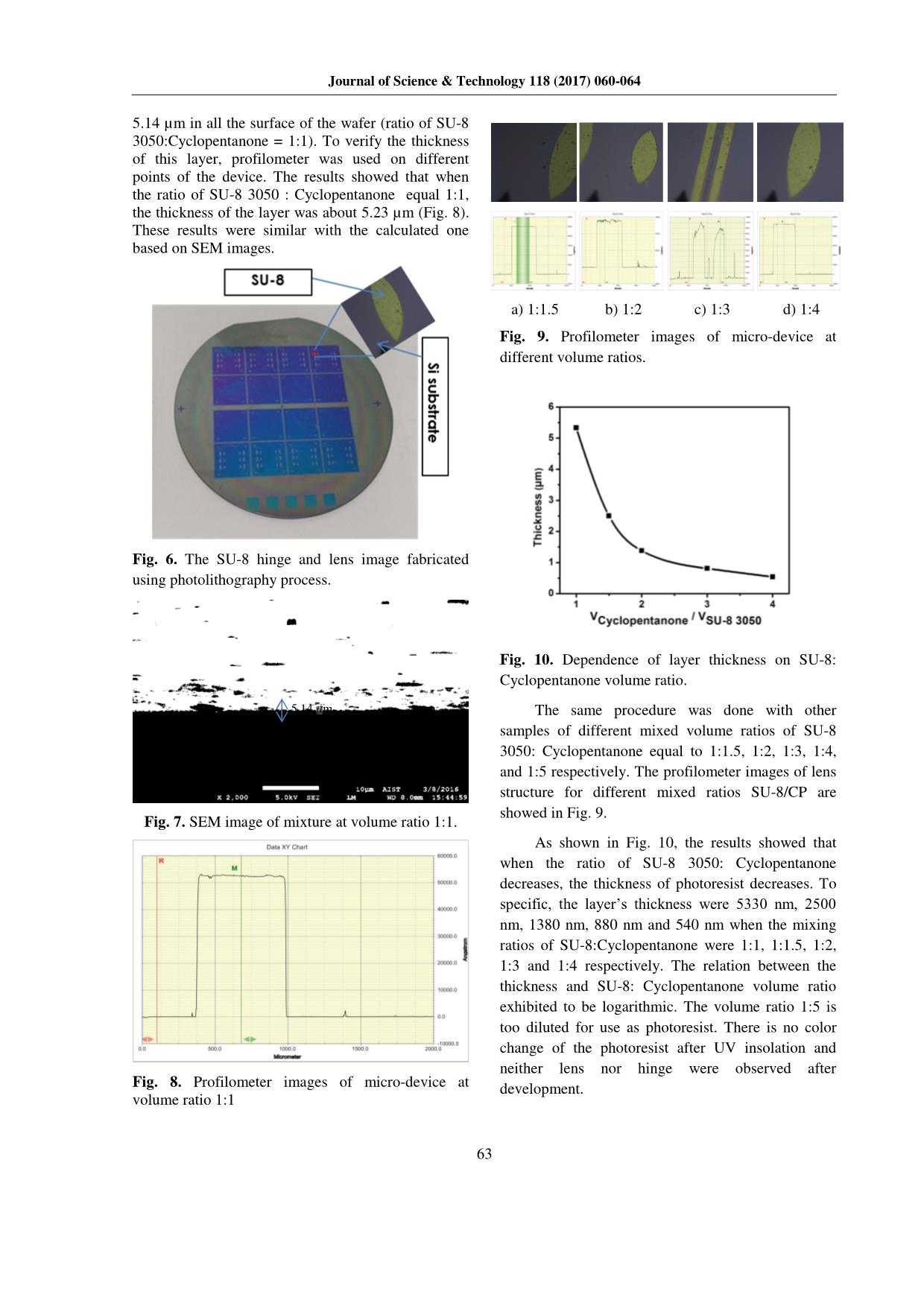
Trang 4
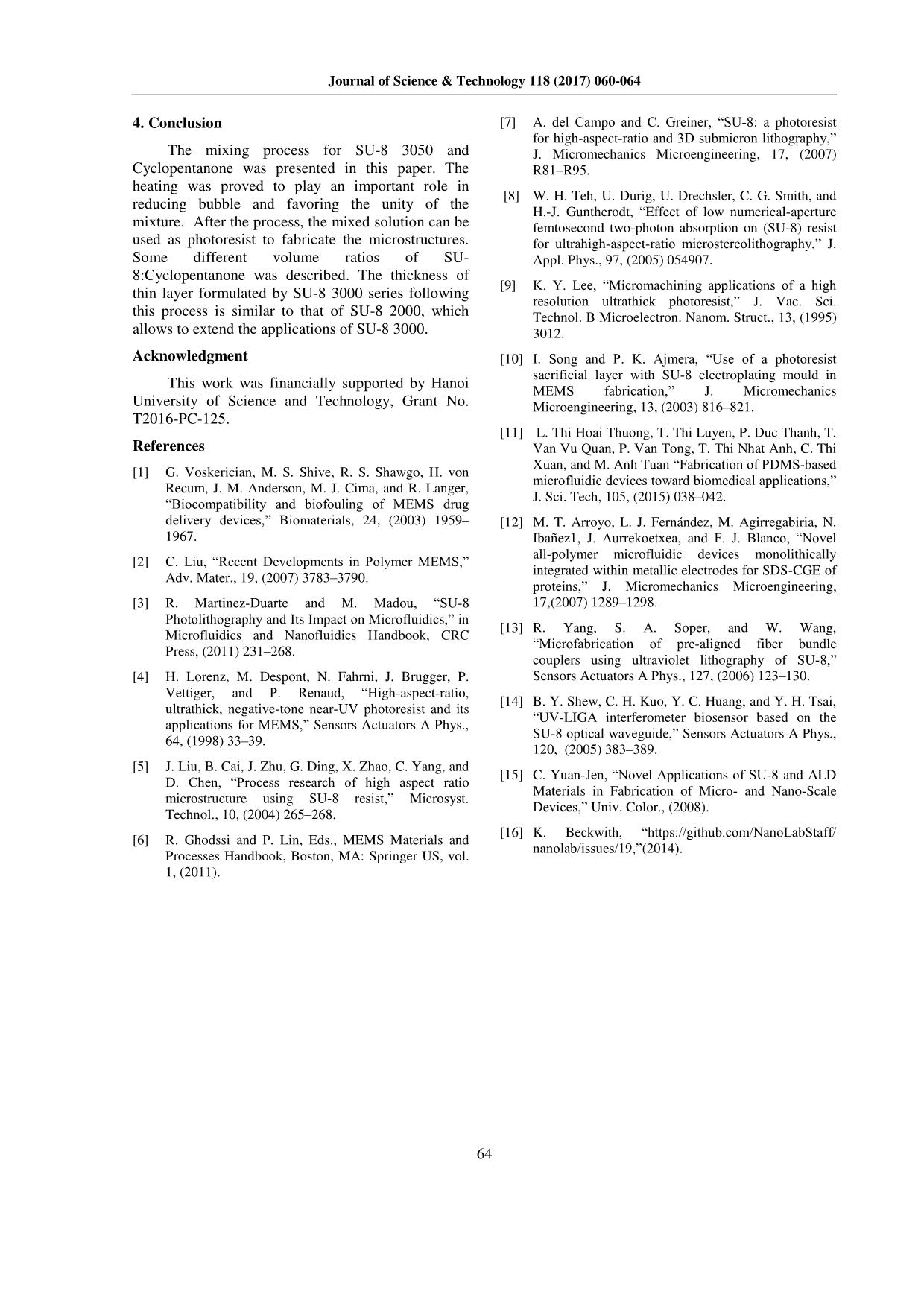
Trang 5
Tóm tắt nội dung tài liệu: Fabrication of Sub-Micro Thin Layer Structures using Cyclopentanone Mix Solution as a Modified SU-8 3050
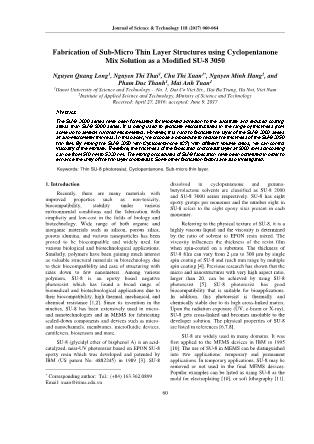
Journal of Science & Technology 118 (2017) 060-064 60 Fabrication of Sub-Micro Thin Layer Structures using Cyclopentanone Mix Solution as a Modified SU-8 3050 Nguyen Quang Long1, Nguyen Thi Thai1, Chu Thi Xuan1*, Nguyen Minh Hang2, and Pham Duc Thanh1, Mai Anh Tuan1 1Hanoi University of Science and Technology - No. 1, Dai Co Viet Str., Hai Ba Trung, Ha Noi, Viet Nam 2Institute of Applied Science and Technology, Ministry of Science and Technology Received: April 27, 2016; accepted: June 9, 2017 Abstract The SU-8 3000 series have been formulated for improved adhesion to the substrate and reduced coating stress than SU-8 2000 series. It is being used to fabricate microstructures in the range of thickness from some up to several hundred micrometers. However, it is hard to fabricate the layer of the SU-8 3000 series at sub-micrometer thinness. In this paper, we propose a procedure to reduce the thickness of the SU-8 3050 thin film. By mixing the SU-8 3050 with Cyclopentanone (CP) with different volume ratios, we can control viscosity of the mixture. Therefore, the thickness of the fabricated photoresist layer at 2000 rpm spincoating can be from 540 nm to 5330 nm. The mixing procedures of SU-8 fabrication have been optimized in order to enhance the unity of the thin layer photoresist. Some other fabrication factors are also investigated. Keywords: Thin SU-8 photoresist, Cyclopentanone, Sub-micro thin layer. 1. Introduction* Recently, there are many materials with improved properties such as non-toxicity, biocompatibility, stability under various environmental conditions and the fabrication with simplicity and low-cost in the fields of biology and biotechnology. Wide range of both organic and inorganic materials such as silicon, porous silica, porous alumina, and various nanoparticles has been proved to be biocompatible and widely used for various biological and biotechnological applications. Similarly, polymers have been gaining much interest as valuable structural materials in biotechnology due to their biocompatibility and ease of structuring with sizes down to few nanometers. Among various polymers, SU-8 is an epoxy based negative photoresist which has found a broad range of biomedical and biotechnological applications due to their biocompatibility, high thermal, mechanical, and chemical resistance [1,2]. Since its invention in the nineties, SU-8 has been extensively used in micro- and nanotechnologies and in MEMS for fabricating scaled-down components and devices such as micro- and nanochannels, membranes, microfluidic devices, cantilevers, biosensors and more. SU-8 (glycidyl ether of bisphenol A) is an acid- catalyzed, near-UV photoresist based on EPON SU-8 epoxy resin which was developed and patented by IBM (US patent No. 4882245) in 1989 [3]. SU-8 * Corresponding author: Tel.: (+84) 163.362.0899 Email: xuan@itims.edu.vn dissolved in cyclopentanone and gamma- butyrolactone solvents are classified as SU-8 2000 and SU-8 3000 series respectively. SU-8 has eight epoxy groups per monomer and the number eight in SU-8 refers to the eight epoxy sites present in each monomer. Referring to the physical texture of SU-8, it is a highly viscous liquid and the viscosity is determined by the ratio of solvent to EPON resin mixed. The viscosity influences the thickness of the resist film when spin-coated on a substrate. The thickness of SU-8 film can vary from 2 µm to 300 µm by single spin coating of SU-8 and reach mm range by multiple spin coating [4]. Previous research has shown that the micro and nanostructures with very high aspect ratio, larger than 20, can be achieved by using SU-8 photoresist [5]. SU-8 photoresist has good biocompatibility that is suitable for bioapplications. In addition, this photoresist is thermally and chemically stable due to its high cross-linked matrix. Upon the radiation exposure (UV, e-beam or X-ray), SU-8 gets cross-linked and becomes insoluble to the developer solution. The physical properties of SU-8 are listed in references [6,7,8]. SU-8 are widely used in many domains. It was first applied to the MEMS devices in IBM in 1995 [10]. The use of SU-8 in MEMS can be distinguished into two applications: temporary and permanent applications. In temporary applications, SU-8 may be removed or not used in the final MEMS devices. Popular examples can be listed as using SU-8 as the mold for electroplating [10], or soft lithography [11]. Journal of Science & Technology 118 (2017) 060-064 61 In permanent applications, SU-8 is widely used in microfluidics [12], optical communication devices [13], and optical waveguide [14]. From the microfluidic point of view, SU-8 is widely used as a mold thanks to strong adhesion to many types of substrates and highly sensitive to the UV expose [3]. In microlense fabrication, SU-8 is a favorite material because of many reasons such as: transparence, ease of microfabrication and mass production; reduction of lens weight; enable the microscale various focus length and array of liquid microlens fabrication [15]. Depending on the viscosity of SU-8, different structures with different size and high can be obtained. Normally, the viscosity range of SU-8 allows for film thicknesses of several µm to more than 100 µm by single spin coating. In our previous study, we have fabricated SU-8 3050 film with thickness from 25 to 125 µm in a single coat [11]. However, in some applications such as micro and nanolens fabrication, SU-8 thin layer in the order of sub micrometer is needed. This can be reached by diluting the resist solution with the solvent. Various works have been reported using gamma-butyrolacton to dilute SU-8 [5]. Another solvent has been used to dilute SU-8 2000 series is cyclopentanone (CP) [16]. However, there is no systematical study on the diluting SU-8 3000 series with cyclopentanone. This paper aims at fabricating SU-8 thin layer in the order of micrometer and sub micrometer thickness with SU-8 3050 using cyclopentanone as a diluting solution. 2. Experiment 2.1 Materials and methods SU-8 3050 photoresist was purchased from MicroChem. Cyclopentanone was purchased from Sigma-Aldrich. The thickness of this layer was also measured by Scanning Electron Microscope (SEM) technique and profilometer. By SEM technique, the sample was tilted at 35 degrees to calculate the thickness of the SU-8 layer. The thickness was calculated based on the equations: ℎ = (1) Where: h is the real thickness of the SU-8 layer; d is the high of projection of the SU-8 layer on the substrate measured by SEM; φ is the inclined angle of the sample. The Veeco Detaak 150 Profilometer is used to measure the roughness of the surface. It uses a stylus to track the surface variations. From the function of position, we can measure the thickness of the sample. 2.2 Mask design This mask was designed in Corel Draw including hinge and lens with different sizes from 0.05 mm to 2.842 mm (Fig. 1) Fig. 1. Mask design for SU-8 mold fabrication. 2.3 Mixing procedure In order to mix SU-8 photoresist with Cyclopentanone, two different process were applied (Fig. 2). Fig. 2. Mixing process of SU-8 3050 and Cyclopentanone. In mixing procedure 1, the first step was to put SU-8 3050 and Cyclopentanone at fixed ratios into a bottle, then the solution was stirred in 30 minutes. Finally, bubbles in the mixture solution were removed by centrifugation. In mixing procedure 2, after stirred, the solution was boiled using hotplate at 90 oC. In this work, we focus on the effect of heating procedure and mix ratios. The SU-8:Cyclopentanone mix ratios 1:1, 1:1.5, 1:2, 1:3, 1:4, and 1:5 were investigated. Mixing procedure 1 Mixing procedure 2 SU-8 3050 +Cyclopentanone SU-8 3050 +Cyclopentanone Stirring magneticStirring magnetic Heating at 90 0C Centrifugation Centrifugation Mixing solution Mixing solution Journal of Science & Technology 118 (2017) 060-064 62 2.4 Lens fabrication procedure The mixture solution at different volume ratios was then used as the photoresist for the basic photolithography process. Before lithography process, the Si substrate was oxidized at 1050 oC in 30 min to obtain 200 nm SiO2 layer. The lens fabrication is illustrated in Fig. 3. Fig. 3. Photolithography process. Step 1: Clean the wafer with piranha solution and then bake at 200 oC in 30 min. Step 2: Spin-coat the mixed solution at 500 rpm for 10 s (ramp: 100 rpm/s), slope, and then 2000 rpm for 30 s (ramp: 100 rpm/s). Step 3: Pre-bake the sample at 95 oC for 2 min. Step 4: Expose the sample to UV light (250 W, 12 mW/cm) for 50 s. Step 5: Post-bake the sample at 65 oC for 1 minute then 95 oC for 2 min with ratio of SU-8: Cyclopentanone equal 1:1, for 1 min with ratio 1:1.5, for 30 s with ratios 1:2, 1:3 and 1:4 respectively. Step 6: Develop the sample with SU-8 developer for 5 min with ratio of SU-8:Cyclopentanone equal to 1:1, for 3 min with ratio 1:1.5, for 2 min with ratios 1:2, 1:3, and 1:4. Step 7: Rinse the sample with IPA and then dry with nitrogen. Step 8: Hard-bake the sample at 180 oC for 20 min. 3. Results and discussion 3.1 Influence of heating Fig. 4 (a) shows the surface of the 4-inch Silicon wafer which is spin-coated with the solution of mixing procedure 1 (SU-8 3050/CP equal to 1:3, 2000 rpm, 30 s, non-heated). The obtained solution is uniform and no gas bubble was observed (Fig. 5). The mixed solution was then used as photoresist layer for the micro-prism fabrication. However, we can also observe that gas bubbles appeared in photoresist layer after coating on the SiO2 surface. It means that SU-8 and Cyclopentanone were not completely mixed or the mixed solution was not well adhered on the SiO2/Si surface. Therefore, we have modified the mixing process in order to promote the mixture quality of the SU- 8/CP. After mixing with magnetic stirrer, the mixture solution was heated at 90 oC in 30 min (mixing procedure 2). Fig. 4 (b) shows that there is no bubble formed after spin coating. It means that the heating process favored the unity of the mixture. The result proved that the prepared solution using mixing procedure 2 can be used to create perfect photoresist layer for photolithography process. Fig. 4. Images of silicon wafer after being spin- coated with the mixed solution, a) no heating mix solution (mixing procedure 1); b) heating mix solution (mixing procedure 2). Fig. 5. Image of the mixture of SU-8 and Cyclopentanone. 3.2 Dependence of SU-8 layer thickness on volume of the Cyclopentanone in mixture solution. The microscope image of the SU-8 mold after dipping the wafer in developer solution is shown in Fig 6. Shape of molds for lens fabrication was formed as design after photolithograph process. The SEM image (Fig. 7) of the device’s structure shows the well-defined shape. SU-8 is the upper section, and the lower part is the silicon substrate. The thickness of this layer was approximate (a) (b) Journal of Science & Technology 118 (2017) 060-064 63 5.14 µm in all the surface of the wafer (ratio of SU-8 3050:Cyclopentanone = 1:1). To verify the thickness of this layer, profilometer was used on different points of the device. The results showed that when the ratio of SU-8 3050 : Cyclopentanone equal 1:1, the thickness of the layer was about 5.23 µm (Fig. 8). These results were similar with the calculated one based on SEM images. Fig. 6. The SU-8 hinge and lens image fabricated using photolithography process. Fig. 7. SEM image of mixture at volume ratio 1:1. Fig. 8. Profilometer images of micro-device at volume ratio 1:1 a) 1:1.5 b) 1:2 c) 1:3 d) 1:4 Fig. 9. Profilometer images of micro-device at different volume ratios. Fig. 10. Dependence of layer thickness on SU-8: Cyclopentanone volume ratio. The same procedure was done with other samples of different mixed volume ratios of SU-8 3050: Cyclopentanone equal to 1:1.5, 1:2, 1:3, 1:4, and 1:5 respectively. The profilometer images of lens structure for different mixed ratios SU-8/CP are showed in Fig. 9. As shown in Fig. 10, the results showed that when the ratio of SU-8 3050: Cyclopentanone decreases, the thickness of photoresist decreases. To specific, the layer’s thickness were 5330 nm, 2500 nm, 1380 nm, 880 nm and 540 nm when the mixing ratios of SU-8:Cyclopentanone were 1:1, 1:1.5, 1:2, 1:3 and 1:4 respectively. The relation between the thickness and SU-8: Cyclopentanone volume ratio exhibited to be logarithmic. The volume ratio 1:5 is too diluted for use as photoresist. There is no color change of the photoresist after UV insolation and neither lens nor hinge were observed after development. 5.14 m Journal of Science & Technology 118 (2017) 060-064 64 4. Conclusion The mixing process for SU-8 3050 and Cyclopentanone was presented in this paper. The heating was proved to play an important role in reducing bubble and favoring the unity of the mixture. After the process, the mixed solution can be used as photoresist to fabricate the microstructures. Some different volume ratios of SU- 8:Cyclopentanone was described. The thickness of thin layer formulated by SU-8 3000 series following this process is similar to that of SU-8 2000, which allows to extend the applications of SU-8 3000. Acknowledgment This work was financially supported by Hanoi University of Science and Technology, Grant No. T2016-PC-125. References [1] G. Voskerician, M. S. Shive, R. S. Shawgo, H. von Recum, J. M. Anderson, M. J. Cima, and R. Langer, “Biocompatibility and biofouling of MEMS drug delivery devices,” Biomaterials, 24, (2003) 1959– 1967. [2] C. Liu, “Recent Developments in Polymer MEMS,” Adv. Mater., 19, (2007) 3783–3790. [3] R. Martinez-Duarte and M. Madou, “SU-8 Photolithography and Its Impact on Microfluidics,” in Microfluidics and Nanofluidics Handbook, CRC Press, (2011) 231–268. [4] H. Lorenz, M. Despont, N. Fahrni, J. Brugger, P. Vettiger, and P. Renaud, “High-aspect-ratio, ultrathick, negative-tone near-UV photoresist and its applications for MEMS,” Sensors Actuators A Phys., 64, (1998) 33–39. [5] J. Liu, B. Cai, J. Zhu, G. Ding, X. Zhao, C. Yang, and D. Chen, “Process research of high aspect ratio microstructure using SU-8 resist,” Microsyst. Technol., 10, (2004) 265–268. [6] R. Ghodssi and P. Lin, Eds., MEMS Materials and Processes Handbook, Boston, MA: Springer US, vol. 1, (2011). [7] A. del Campo and C. Greiner, “SU-8: a photoresist for high-aspect-ratio and 3D submicron lithography,” J. Micromechanics Microengineering, 17, (2007) R81–R95. [8] W. H. Teh, U. Dürig, U. Drechsler, C. G. Smith, and H.-J. Güntherodt, “Effect of low numerical-aperture femtosecond two-photon absorption on (SU-8) resist for ultrahigh-aspect-ratio microstereolithography,” J. Appl. Phys., 97, (2005) 054907. [9] K. Y. Lee, “Micromachining applications of a high resolution ultrathick photoresist,” J. Vac. Sci. Technol. B Microelectron. Nanom. Struct., 13, (1995) 3012. [10] I. Song and P. K. Ajmera, “Use of a photoresist sacrificial layer with SU-8 electroplating mould in MEMS fabrication,” J. Micromechanics Microengineering, 13, (2003) 816–821. [11] L. Thi Hoai Thuong, T. Thi Luyen, P. Duc Thanh, T. Van Vu Quan, P. Van Tong, T. Thi Nhat Anh, C. Thi Xuan, and M. Anh Tuan “Fabrication of PDMS-based microfluidic devices toward biomedical applications,” J. Sci. Tech, 105, (2015) 038–042. [12] M. T. Arroyo, L. J. Fernández, M. Agirregabiria, N. Ibañez1, J. Aurrekoetxea, and F. J. Blanco, “Novel all-polymer microfluidic devices monolithically integrated within metallic electrodes for SDS-CGE of proteins,” J. Micromechanics Microengineering, 17,(2007) 1289–1298. [13] R. Yang, S. A. Soper, and W. Wang, “Microfabrication of pre-aligned fiber bundle couplers using ultraviolet lithography of SU-8,” Sensors Actuators A Phys., 127, (2006) 123–130. [14] B. Y. Shew, C. H. Kuo, Y. C. Huang, and Y. H. Tsai, “UV-LIGA interferometer biosensor based on the SU-8 optical waveguide,” Sensors Actuators A Phys., 120, (2005) 383–389. [15] C. Yuan-Jen, “Novel Applications of SU-8 and ALD Materials in Fabrication of Micro- and Nano-Scale Devices,” Univ. Color., (2008). [16] K. Beckwith, “https://github.com/NanoLabStaff/ nanolab/issues/19,”(2014).
File đính kèm:
fabrication_of_sub_micro_thin_layer_structures_using_cyclope.pdf