Bài giảng Cơ sở kĩ thuật dầu khí - Chương 7: Well completion and stimulation
Chương 7: Well completion and stimulation
CONTENTS
1. Basic Completion Methods
2. Completion Procedure
3. Perforating
4. Stimulation
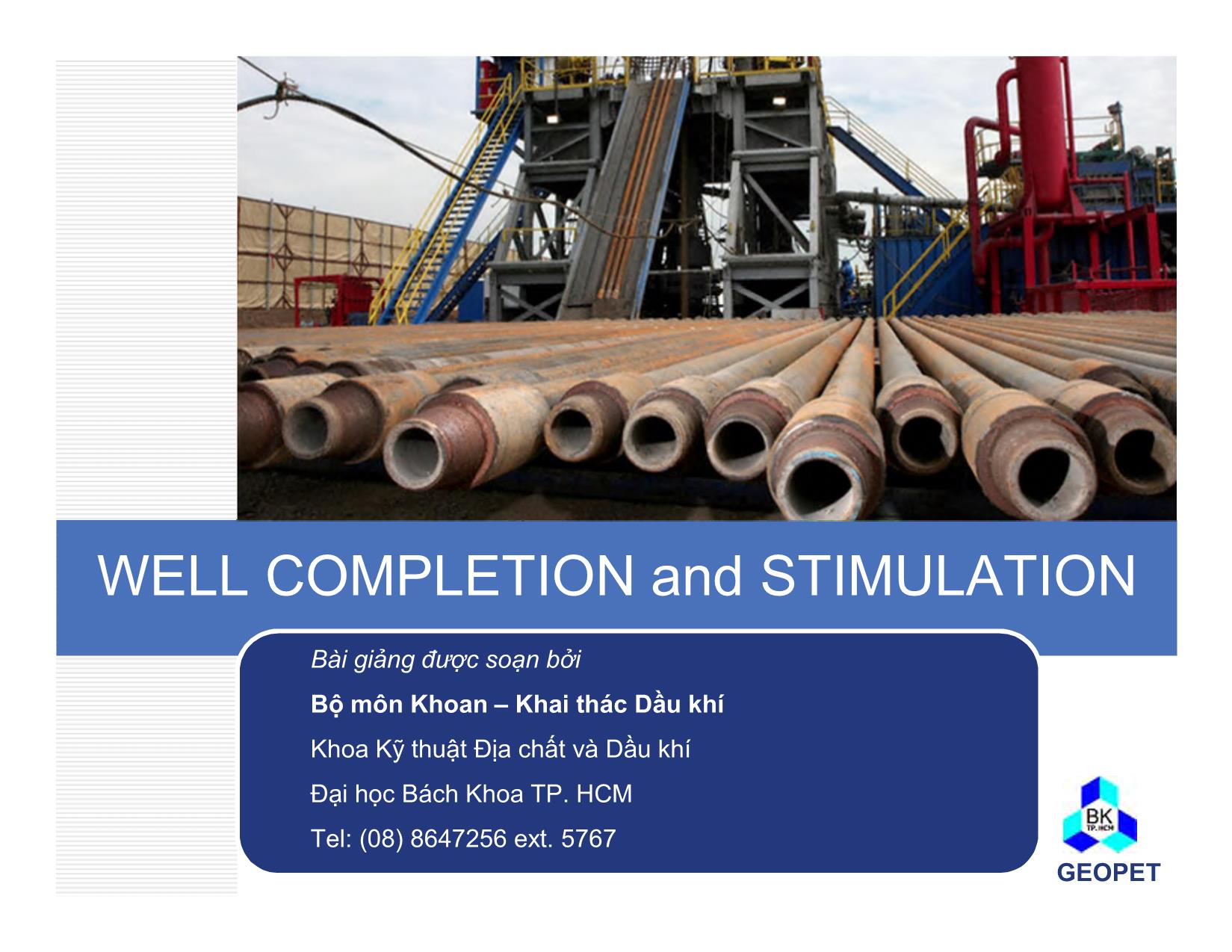
Trang 1
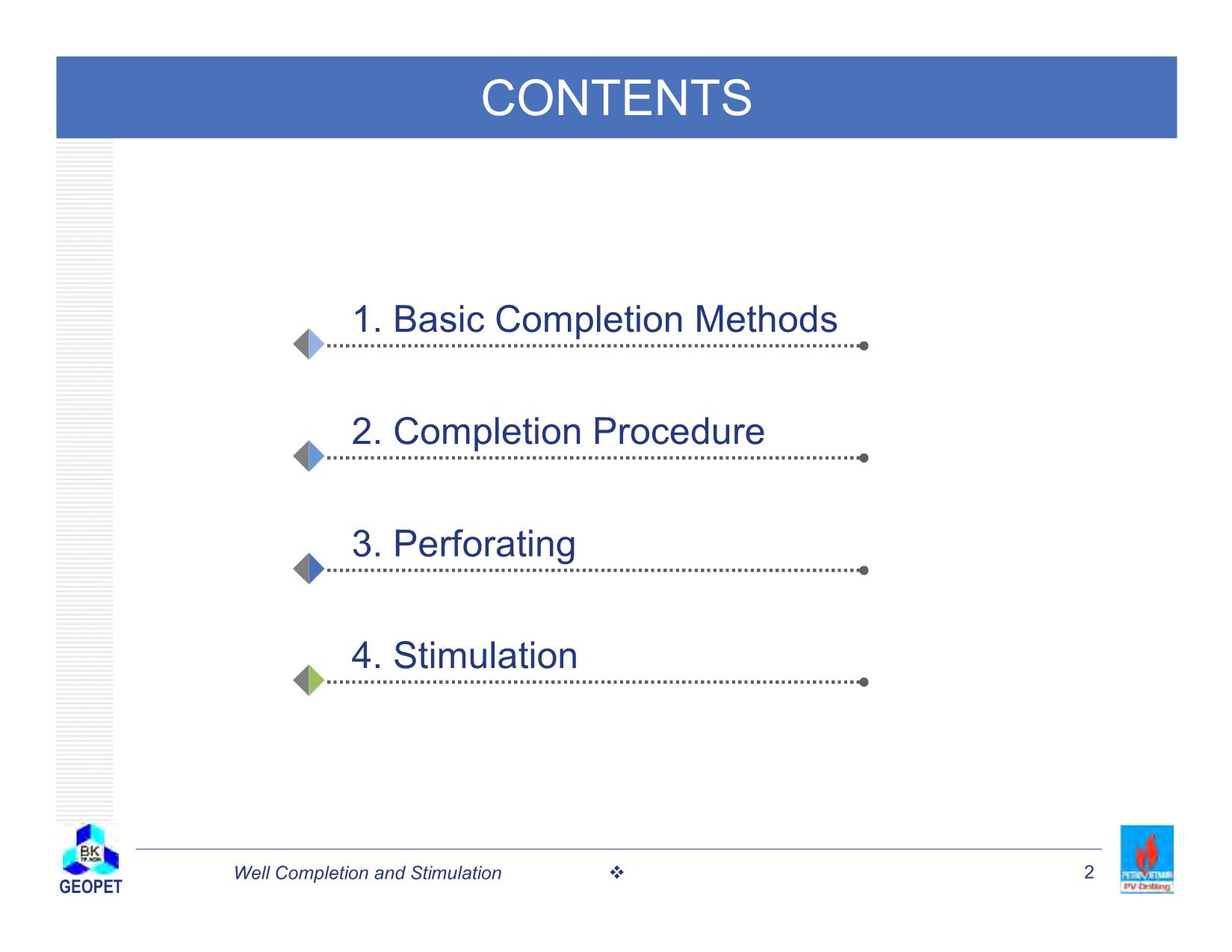
Trang 2
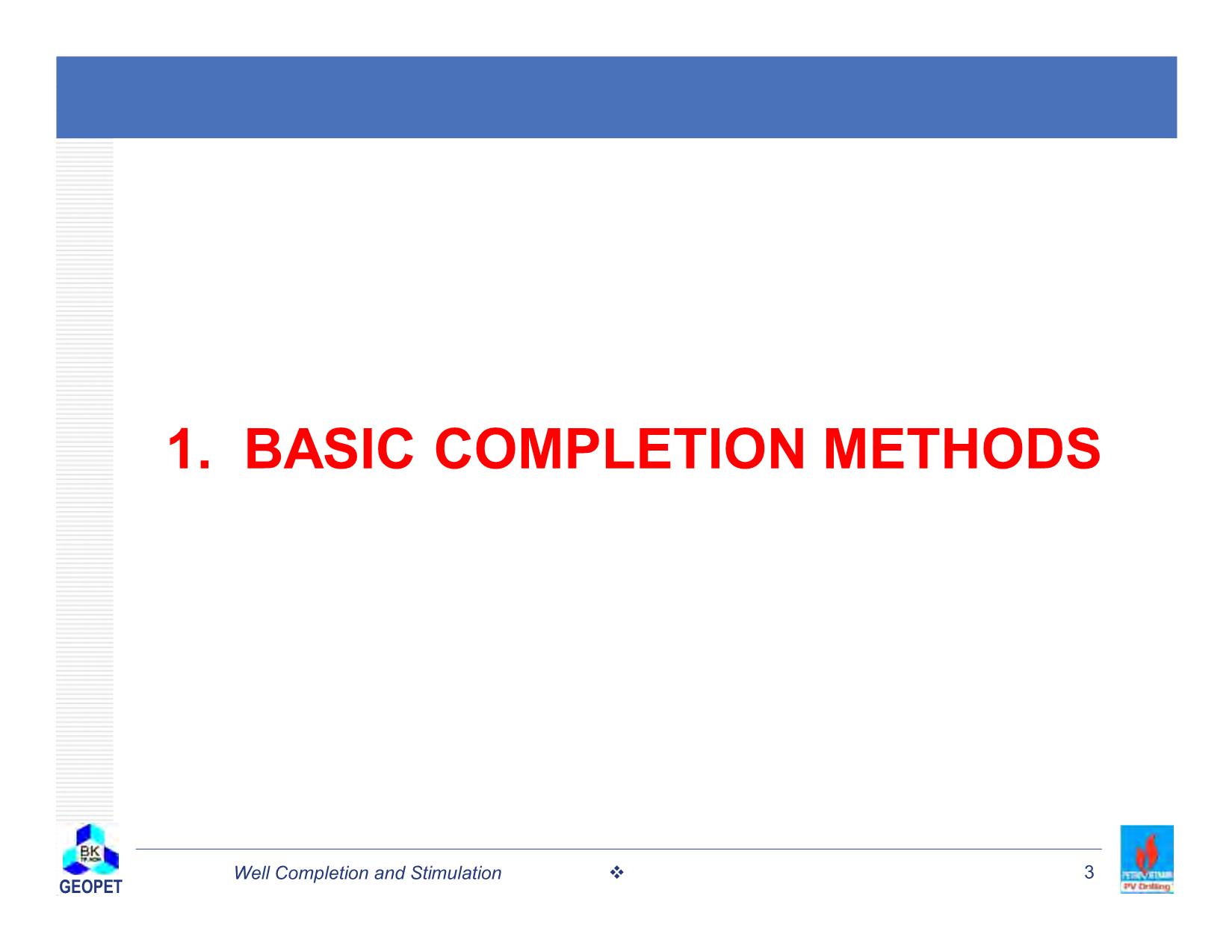
Trang 3
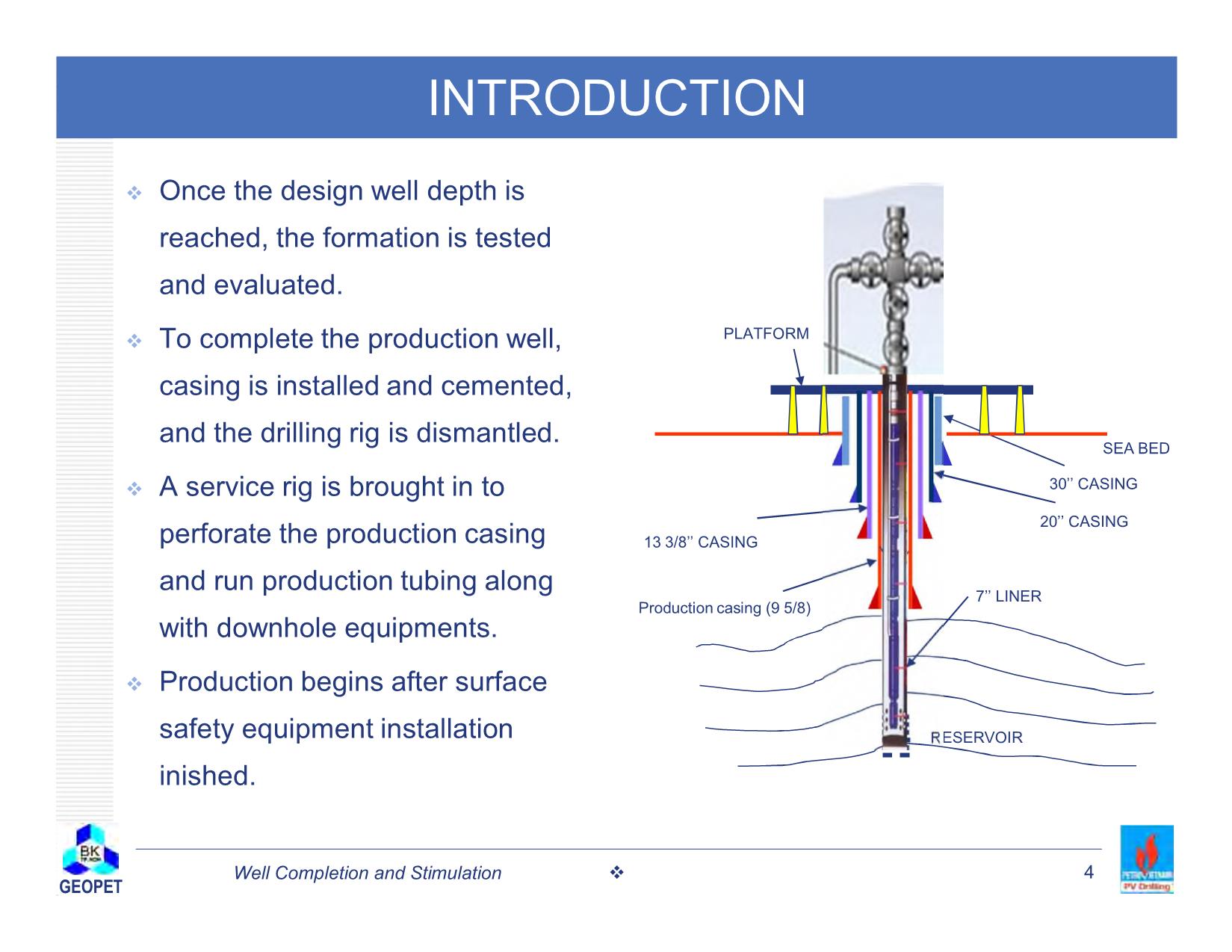
Trang 4
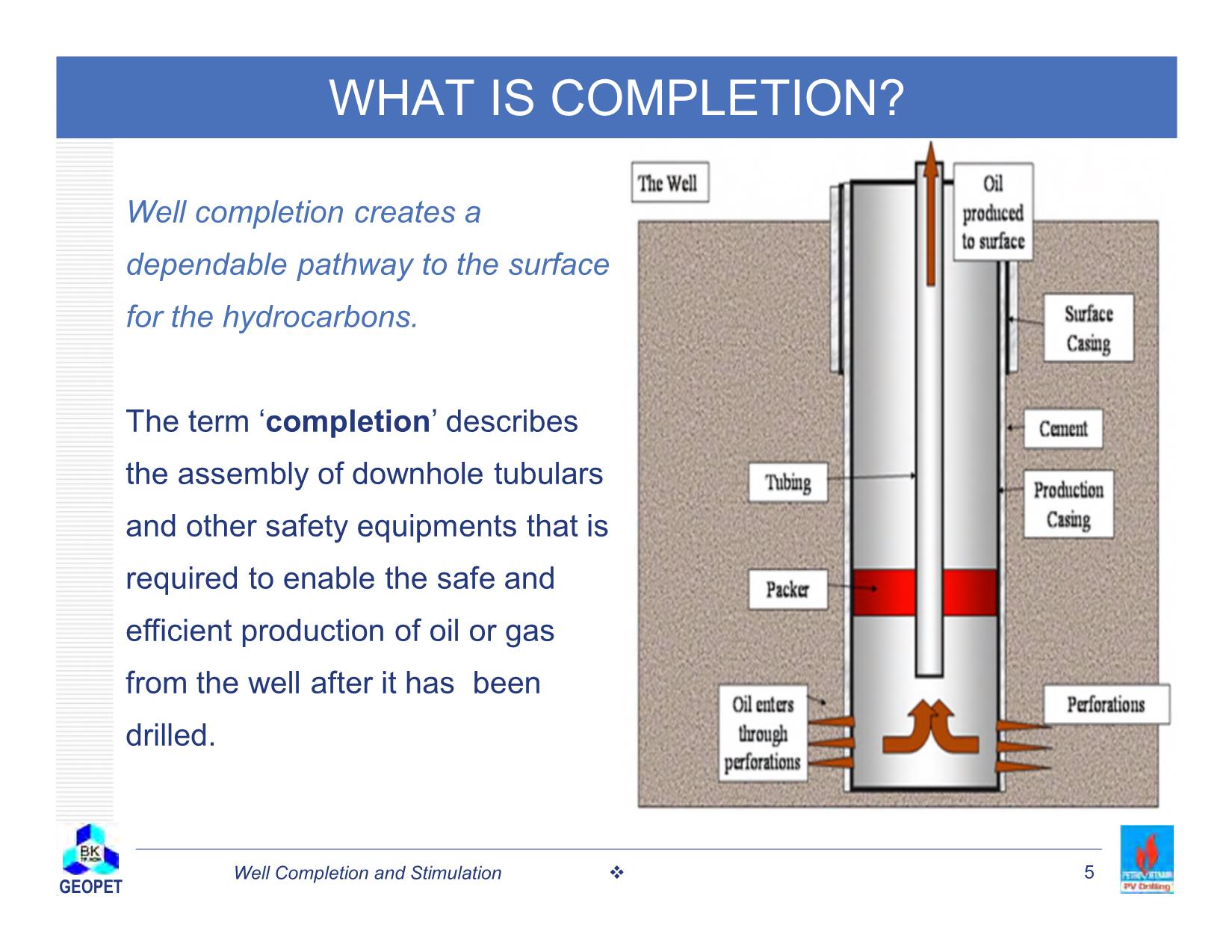
Trang 5
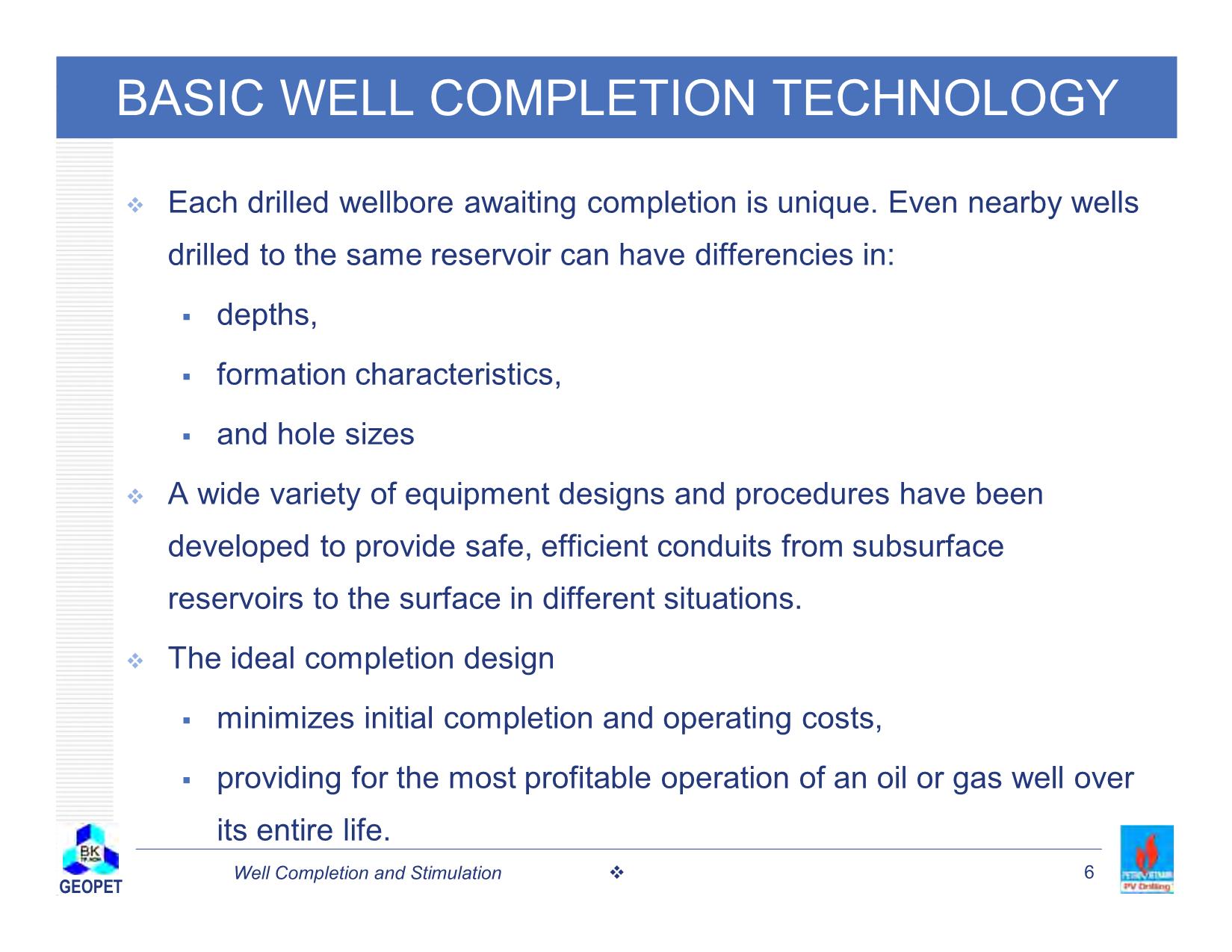
Trang 6
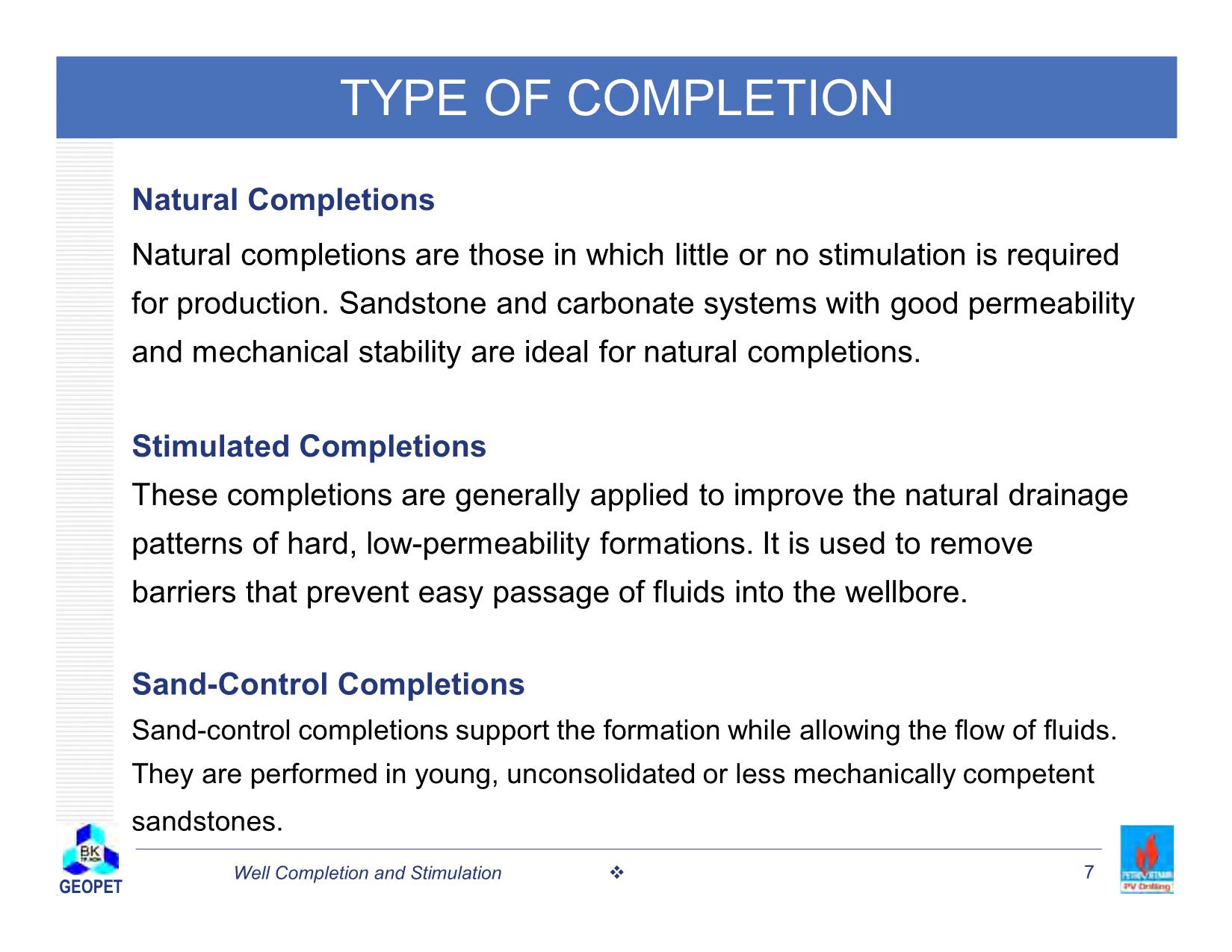
Trang 7
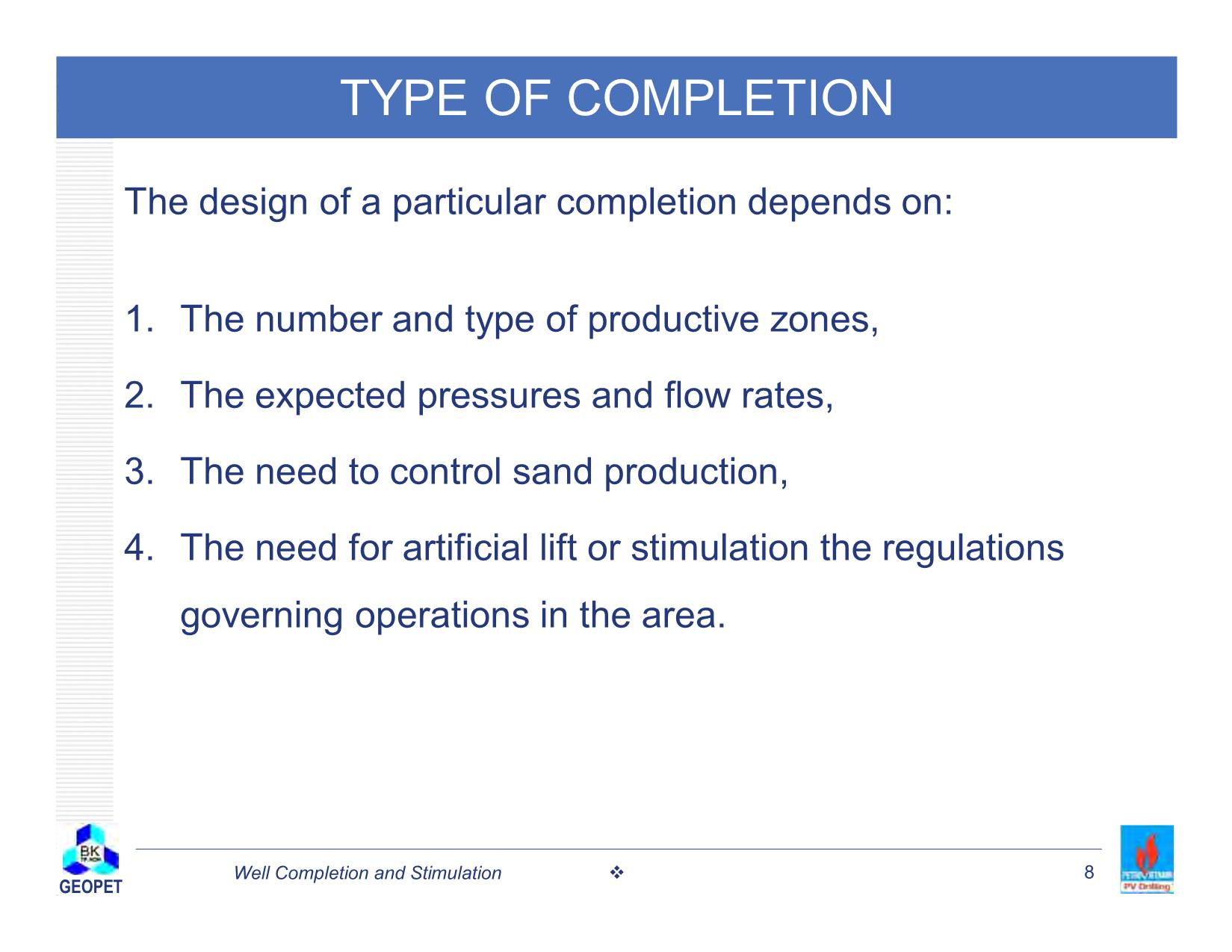
Trang 8
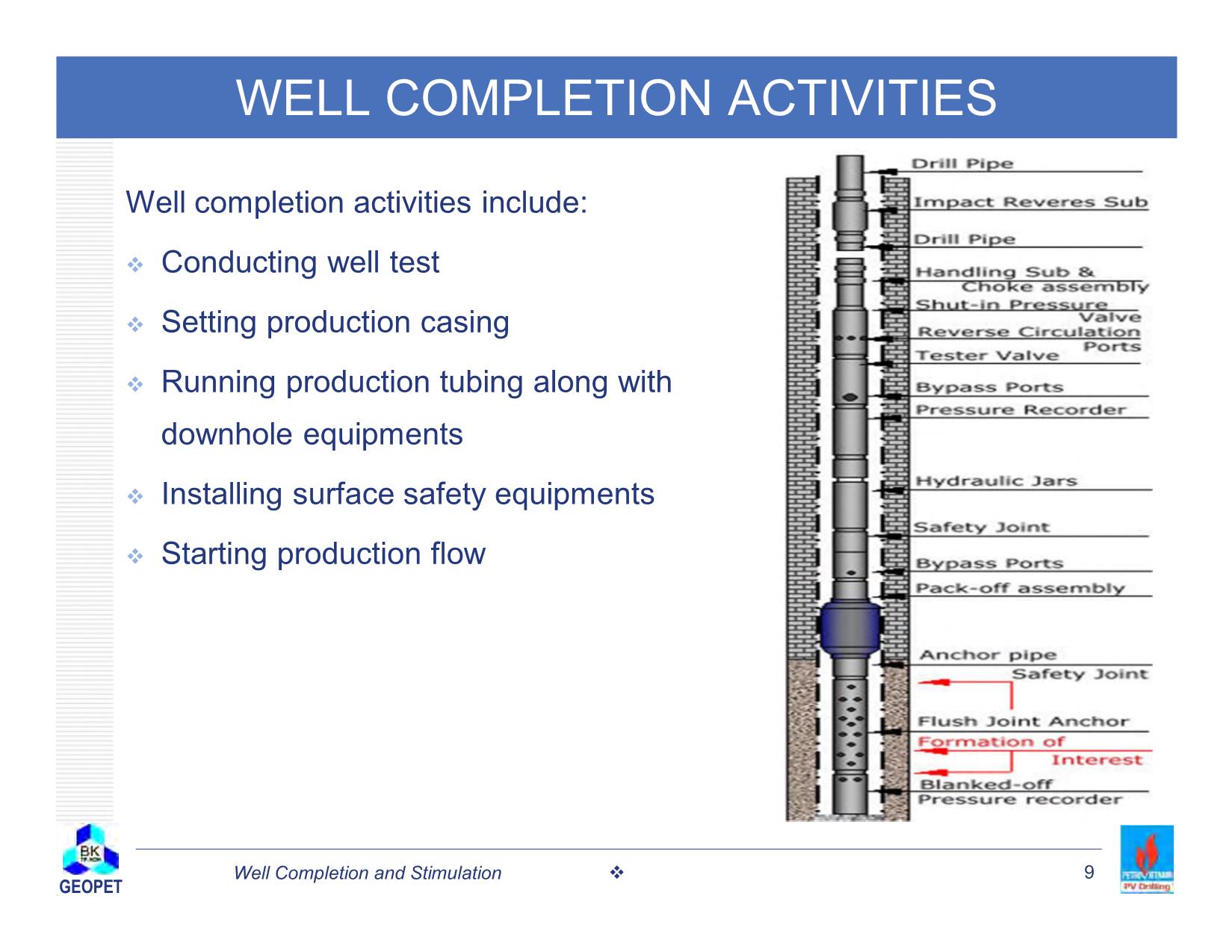
Trang 9
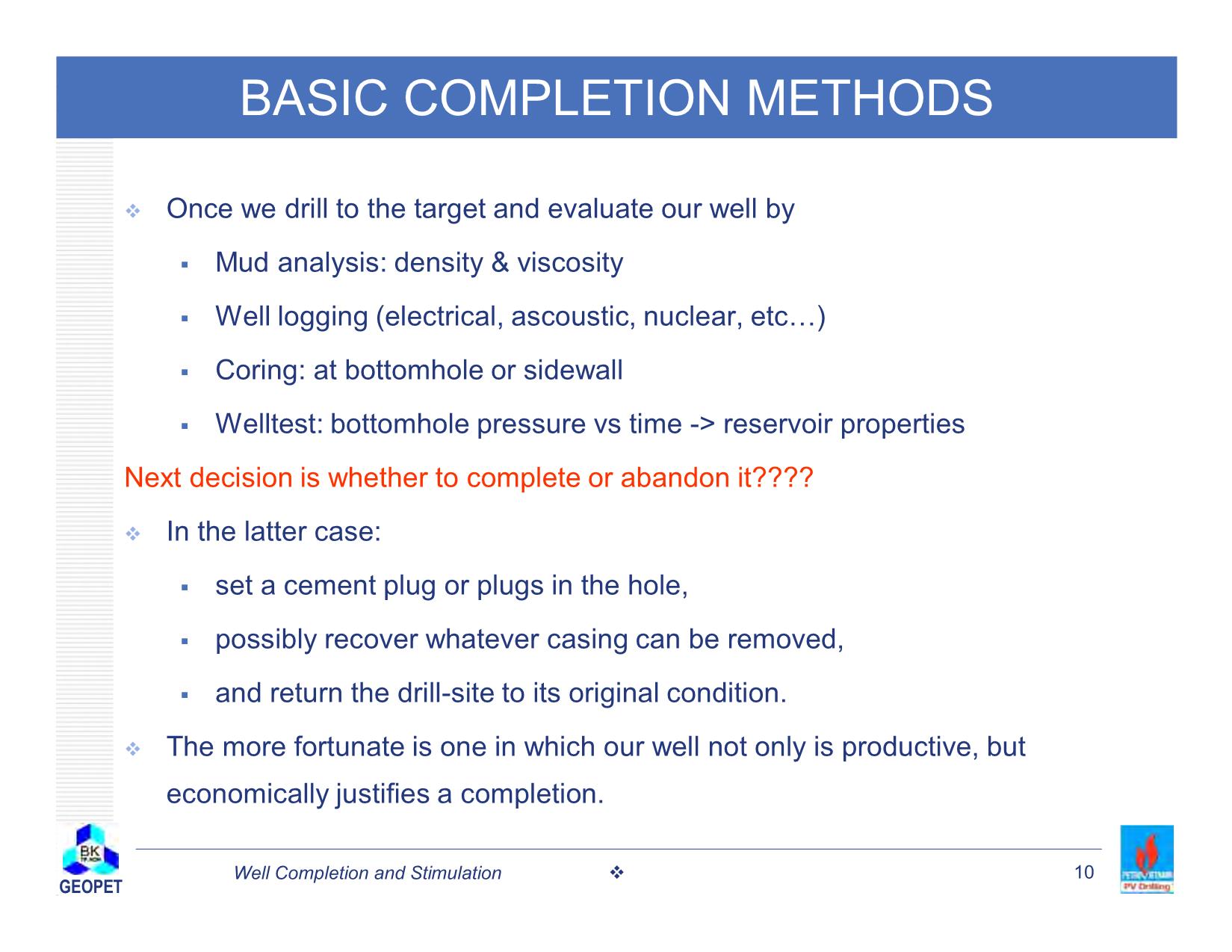
Trang 10
Tải về để xem bản đầy đủ
Bạn đang xem 10 trang mẫu của tài liệu "Bài giảng Cơ sở kĩ thuật dầu khí - Chương 7: Well completion and stimulation", để tải tài liệu gốc về máy hãy click vào nút Download ở trên
Tóm tắt nội dung tài liệu: Bài giảng Cơ sở kĩ thuật dầu khí - Chương 7: Well completion and stimulation
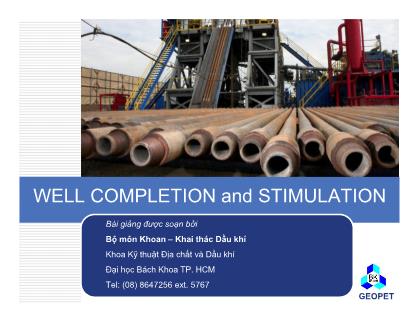
WELL COMPLETION and STIMULATION GEOPET Bài giảng được soạn bởi Bộ môn Khoan – Khai thác Dầu khí Khoa Kỹ thuật Địa chất và Dầu khí Đại học Bách Khoa TP. HCM Tel: (08) 8647256 ext. 5767 GEOPET Well Completion and Stimulation 2 CONTENTS 1. Basic Completion Methods 2. Completion Procedure 3. Perforating 4. Stimulation GEOPET Well Completion and Stimulation 3 1. BASIC COMPLETION METHODS GEOPET Well Completion and Stimulation 4 Once the design well depth is reached, the formation is tested and evaluated. To complete the production well, casing is installed and cemented, and the drilling rig is dismantled. A service rig is brought in to perforate the production casing and run production tubing along with downhole equipments. Production begins after surface safety equipment installation inished. INTRODUCTION 30’’ CASING 20’’ CASING 13 3/8’’ CASING 7’’ LINER RESERVOIR SEA BED PLATFORM Production casing (9 5/8) GEOPET Well Completion and Stimulation 5 WHAT IS COMPLETION? Well completion creates a dependable pathway to the surface for the hydrocarbons. The term ‘completion’ describes the assembly of downhole tubulars and other safety equipments that is required to enable the safe and efficient production of oil or gas from the well after it has been drilled. GEOPET Well Completion and Stimulation 6 BASIC WELL COMPLETION TECHNOLOGY Each drilled wellbore awaiting completion is unique. Even nearby wells drilled to the same reservoir can have differencies in: depths, formation characteristics, and hole sizes A wide variety of equipment designs and procedures have been developed to provide safe, efficient conduits from subsurface reservoirs to the surface in different situations. The ideal completion design minimizes initial completion and operating costs, providing for the most profitable operation of an oil or gas well over its entire life. GEOPET Well Completion and Stimulation 7 Natural Completions Natural completions are those in which little or no stimulation is required for production. Sandstone and carbonate systems with good permeability and mechanical stability are ideal for natural completions. Stimulated Completions These completions are generally applied to improve the natural drainage patterns of hard, low-permeability formations. It is used to remove barriers that prevent easy passage of fluids into the wellbore. Sand-Control Completions Sand-control completions support the formation while allowing the flow of fluids. They are performed in young, unconsolidated or less mechanically competent sandstones. TYPE OF COMPLETION GEOPET Well Completion and Stimulation 8 TYPE OF COMPLETION The design of a particular completion depends on: 1. The number and type of productive zones, 2. The expected pressures and flow rates, 3. The need to control sand production, 4. The need for artificial lift or stimulation the regulations governing operations in the area. GEOPET Well Completion and Stimulation 9 WELL COMPLETION ACTIVITIES Well completion activities include: Conducting well test Setting production casing Running production tubing along with downhole equipments Installing surface safety equipments Starting production flow GEOPET Well Completion and Stimulation 10 BASIC COMPLETION METHODS Once we drill to the target and evaluate our well by Mud analysis: density & viscosity Well logging (electrical, ascoustic, nuclear, etc) Coring: at bottomhole or sidewall Welltest: bottomhole pressure vs time -> reservoir properties Next decision is whether to complete or abandon it???? In the latter case: set a cement plug or plugs in the hole, possibly recover whatever casing can be removed, and return the drill-site to its original condition. The more fortunate is one in which our well not only is productive, but economically justifies a completion. GEOPET Well Completion and Stimulation 11 The next step usually involves the running of the final string of casing - the production string. The manner in which this is done determines the basic completion method and may follow one of several configurations: (interface between the wellbore & reservoir) the openhole completion, the liner completion, the cased and perforated completion • Without liner • With liner BASIC COMPLETION METHODS GEOPET Well Completion and Stimulation 12 The openhole completion: the producing formation is not isolated by the casing, which extends only to the top of the producing interval. The slotted liner completion: which is not cemented and not "tied back" to the surface. BASIC COMPLETION METHODS GEOPET Well Completion and Stimulation 13 The cased and perforated completion Without liner: cementing the production casing across the productive interval and then perforating the casing for production With liner: a liner is cemented and perforated as a cased and perforated completion BASIC COMPLETION METHODS GEOPET Well Completion and Stimulation 14 One of these configurations will be the basis for the completion design, which may incorporate: one or multiple strings of tubing: single, dual, or triple, etc and a variety of tubing components to facilitate production (production method): pumping, flowing, etc. from one or multiple zones: single or multiple zones For our purposes, a cased and perforated well with a single tubing string will serve to illustrate the typical completion procedure. BASIC COMPLETION METHODS GEOPET Well Completion and Stimulation 15 Subsea production systems are wells located on the sea floor, as opposed to at the surface. The safety equipments are installed underwater on the seabed. They enable early production from deepwater, remote, and marginal fields. Subsea production system offer a ... y researchers realized that the fracture would close once the hydraulic pressure was relieved, a solid material is added to the fracturing fluid to "prop" open the fracture. Initial jobs consisted of perhaps 500 to 1000 gallons of gelled kerosene (napalm) as a fracturing fluid, with perhaps 1/2 lb of sand per gallon (Neely 1977). These early fractures were assumed to be horizontal, following the bedding planes of the rock. GEOPET Well Completion and Stimulation 60 FRACTURING Since that time, an enormous amount of research and field application of fracturing techniques has been carried out. Theoretical mathematical models have been developed that permit engineers to predict the type of fracture and productivity increase that will result from a certain magnitude fracture treatment. These calculations prevent the unnecessary use of enormous amounts of costly fracture fluid, proppant material, and equipment horse power by tailoring the treatment to the particular well. GEOPET Well Completion and Stimulation 61 FRACTURING Although there is still some disagreement among theorists concerning the behavior of rock under stress, we now know that: Fracture orientation is dependent upon geologic conditions, And that most fractures are vertical rather than horizontal. GEOPET Well Completion and Stimulation 62 FRACTURING In order to significantly improve a well's productivity, a fracture must conduct fluid at a rate that is several orders of magnitude greater than the conductivity of the rock itself. Creating a high-conductivity fracture involves selecting the appropriate fluid, additives, and proppant, determining the optimum volume of material to be pumped, pumping the material at the appropriate rate and pressure. GEOPET Well Completion and Stimulation 63 FRACTURING Desirable features for a fracturing fluid include the ability to remain in the fracture and not leak off into the formation, the viscosity necessary to transport the proppant into the fracture, the ability to flow back into the well easily after depositing the proppant, and low cost. Water-based polymer solutions are popular, as are gel led hydrocarbons for water-sensitive formations. A wide variety of additives are available to reduce fluid friction in piping, prevent fluid loss from the fracture, control contamination, and insure compatibility with the formation. GEOPET Well Completion and Stimulation 64 FRACTURING The standard proppant used to hold open the fracture is silica sand. Sand can be crushed, however, in deep formations where fracture- closure stresses are high. In such cases sintered bauxite, zirconium oxide, or other high- strength materials are substituted for sand. The goal is to create at least a partial monolayer of proppant within the fracture, holding the fracture open, but not plugging it completely. GEOPET Well Completion and Stimulation 65 FRACTURING High-strength proppant forms a single layer of particle that holds open the fracture and permits flow GEOPET Well Completion and Stimulation 66 FRACTURING At the wellsite, the equipment required for a large fracturing job is somewhat more sophisticated than that required for an acid stimulation. The fracturing fluid is held in tanks, where any necessary additives are mixed. Proppant is sorted in similar containers, from which it is conveyed to high-rate blenders. Blenders combine the fracture fluid with the proppant and send the mixture to the pumping system. GEOPET Well Completion and Stimulation 67 FRACTURING GEOPET Well Completion and Stimulation 68 FRACTURING These blenders are critical to the fracturing procedure because, once the pumping process is under way, interruption of it can result in bridging of the proppant in the tubing or the fracture. The job will fail and retreatment will be required. Often, for major fracturing treatments, large volumes of fluid must be pumped at high pressure. This usually means that standard size pump trucks must be hooked up in parallel to a manifold. The fluid is pumped down the tubing, drillpipe, or casing by this system into the formation. A wellhead protector is often inserted through the Christmas tree to protect its interior from the abrasive, high-pressure fracturing fluid. GEOPET Well Completion and Stimulation 69 Sand Control GEOPET Well Completion and Stimulation 70 SAND CONTROL While a certain amount of sediment will always be produced along with formation fluids, sand control is the technology and practice of preventing sand flow from unconsolidated sandstone formations. Such a problem is often found in Tertiary sediments, at shallow depths, and in areas such as Nigeria, Indonesia, Trinidad, Venezuela, Canada, the U.S. Gulf Coast, and the Los Angeles Basin (Patton and Abbott 1982). GEOPET Well Completion and Stimulation 71 SAND CONTROL Sand production leads to any or all of the following problems: Casing collapse; Abrasion of downhole and surface equipment; Reduced productivity; Completely plugged ("sanded-up") wells. GEOPET Well Completion and Stimulation 72 SAND CONTROL Methods for controlling sand production have generally involved one of three approaches: an epoxy resin that can be injected into the formation near the wellbore and allowed to harden; this cements the sand grains together and by consolidating them prevents their movement. a metal screen and sand grain barrier that screens out the formation sand but does not inhibit fluid flow into the wellbore; or a combined treatment involving fracture stimulation and sand control, known as a “frac and pack” treatment. GEOPET Well Completion and Stimulation 73 SAND CONTROL Metal wire-wrapped screens and gravel packs work in a manner analogous to a large crowd of people trying to leave a theatre through a small door. Each could pass through the door individually, but when several try at once they form a "bridge" that prevents those at the rear of the pack from moving at all. In sand control, bridging methods employ wire-wrapped screens or slotted casing, both of which have carefully sized openings that allow the formation sand to be deposited against them. GEOPET Well Completion and Stimulation 74 SAND CONTROL In the case of gravel packs, carefully sized clean sand is placed outside the screen to retain the formation sand at its outer edge. GEOPET Well Completion and Stimulation 75 SAND CONTROL Correct sizing of both the gravel pack sand and the gravel pack screen requires knowledge of the information about formation grain size distribution that had been obtained from cores. Guidelines have been developed to select sand and screen sizes that will prevent formation sand movement but not inhibit formation fluid flow. Gravel packing may be carried out in an openhole completion in which under-reaming has enlarged the volume of the pack to enlarge the hole prior to placing the gravel pack sand outside the screen by the reverse circulation technique. GEOPET Well Completion and Stimulation 76 SAND CONTROL Typical Open Hole Gravel Pack Installation Typical Cased Hole Gravel Pack Installation GEOPET Well Completion and Stimulation 77 SAND CONTROL An inside gravel pack may also be accomplished in a cased and perforated completion. Three common types of inside gravel packing are shown in 1. Wash down, where the gravel is placed in the hole and the screen “washed” through it by circulating, 2. Reverse circulation, where the sand is pumped down the annulus and the carrying fluid returned up the tubing, 3. Crossover allows the sand slurry to be pumped down the tubing, depending on the method of sand placement. GEOPET Well Completion and Stimulation 78 SAND CONTROL Wash down Reverse circulation Cross over GEOPET Well Completion and Stimulation 79 SAND CONTROL Gravel packs require There is a good bond between casing and formation, The perforations be large and free of debris, and that the gravel pack sand is Evenly placed around the screen And not mixed with formation sand or dirty completion fluid. GEOPET Well Completion and Stimulation 80 SAND CONTROL Sand consolidation techniques are best applied to shorter completion intervals. Careful mixing and injecting of the plastic resins is important to prevent the mixture from hardening either too far into the formation from the wellbore or inside the casing. Although some permeability is lost in this technique, no restrictions to flow are placed inside the casing as is the case in gravel packing. This is attractive if future downhole work is anticipated and the wellbore may need to be cleaned out. GEOPET Well Completion and Stimulation 81 SAND CONTROL “Frac and Pack” completion methods combine hydraulic fracturing and gravel packing into a single well treatment. They are designed to create relatively short, highly conductive fractures in reservoirs of moderate to high permeability. Frac and pack techniques have come into wide use, and in some areas have largely supplanted the more conventional sand control methods described above. GEOPET Well Completion and Stimulation 82 SAND CONTROL Areas of application include - bypassing near-wellbore formation damage that can’t be removed with acid treatments. - increasing formation support of casing in reservoirs that have formation compacting tendencies. - vertically connecting productive intervals in thin, laminated sand- shale sequences. - Improving productivity in some low-permeability reservoirs - alleviating problems caused by high wellbore differential pressure. GEOPET Well Completion and Stimulation 83 SAND CONTROL The decision to complete a well with sand control is not always easy. For example, in a formation where sand production may occur, the completion designer may risk the cost of a future workover in order to save the immediate expense of a gravel pack. This may be particularly true if multiple producing zones in the well will require future work down hole. Of course, the cost of remedial work to clean out and gravel-pack a sanded-up well may be much higher than if the work had been done during the original completion. This is particularly true at some offshore locations where the cost of simply moving a work over rig on to a producing structure can be enormous. With sand control, as with other facets of the completion procedure, decision making is dependent on a number of factors. GEOPET Well Completion and Stimulation 84 Completion Components GEOPET Well Completion and Stimulation 85 Well Head Reservoir Packer Safety Valve Gas Lift Valve X-mas Tree Tubing hanger Production Tubing Perforation Hydraulic Control Line Pump Out Plug Sump Oil Well After Completion COMPLETION COMPONENTS GEOPET Well Completion and Stimulation 86 30’’ CASING 9 5/8’’ CASING 20’’ CASING 13 3/8’’ CASING 7’’ LINER PRODUCTION TUBING RESEVOIR SEA BED PLATFORM Only this casing is visible from outside Production casing (9 5/8) WELL HEAD EQUIPMENT COMPLETION COMPONENTS GEOPET Well Completion and Stimulation 87 The parts of a downhole equipment are: Gas Lift Valve Safety Valve Hydraulic Control Line Pump Out Plug Packer DOWNHOLE EQUIPMENT GEOPET Well Completion and Stimulation 88 DOWNHOLE EQUIPMENT Packer Packer is a device consisting of a sealing device, a holding or setting device and an inside passage for fluids. It expands externally to seal the well bore. It helps in blocking the fluids through the annular space between the pipe and the well bore wall. Packers use flexible, electrometric elements that expand. It is set hydraulically from the surface. GEOPET Well Completion and Stimulation 89 DOWNHOLE EQUIPMENT Gas Lift Valve The gas lift valve is a device installed on a gas lift cylinder or mandrel. This device is used to control the flow of gas between the exterior and interior of well tubing. It consists of an inlet, outlet, a main valve, a main chamber and so on. The design of the side pocket is such that the components that are installed do not obstruct the flow of production. This enables access to the well bore and the other components of completion. GEOPET Well Completion and Stimulation 90 DOWNHOLE EQUIPMENT Safety Valve A safety valve is a device that is installed in the upper well bore to provide emergency closure of the channels that produce oil. The valve has a housing and a movable valve element that controls the flow of fluid in the well. GEOPET Well Completion and Stimulation 91 DOWNHOLE EQUIPMENT Hydraulic Control Line Hydraulic control line is a device filled with hydraulic fluid and connected to a hydraulic fluid source. Hydraulic control line is used to operate the safety valve. When the control line is pressurized up to a certain pressure limit, the safety valve opens. Its one end connects at the top of the safety valve and the other end to a pressurizing panel at the surface. It is lowered along with the safety valve while lowering the tubing string during completion. GEOPET Well Completion and Stimulation 92 Well Head The surface termination of a wellbore that incorporates facilities for installing casing hangers during the well construction phase is the well head. The well head is installed on top of the casing before starting to drill. It has two or three sections. Each section has two flanges to facilitate the connections at both the ends. SURFACE CONTROL EQUIPMENTS KẾT THÚC
File đính kèm:
bai_giang_co_so_ki_thuat_dau_khi_chuong_7_well_completion_an.pdf